-
- News
- Books
Featured Books
- pcb007 Magazine
Latest Issues
Current IssueInventing the Future with SEL
Two years after launching its state-of-the-art PCB facility, SEL shares lessons in vision, execution, and innovation, plus insights from industry icons and technology leaders shaping the future of PCB fabrication.
Sales: From Pitch to PO
From the first cold call to finally receiving that first purchase order, the July PCB007 Magazine breaks down some critical parts of the sales stack. To up your sales game, read on!
The Hole Truth: Via Integrity in an HDI World
From the drilled hole to registration across multiple sequential lamination cycles, to the quality of your copper plating, via reliability in an HDI world is becoming an ever-greater challenge. This month we look at “The Hole Truth,” from creating the “perfect” via to how you can assure via quality and reliability, the first time, every time.
- Articles
- Columns
- Links
- Media kit
||| MENU - pcb007 Magazine
Estimated reading time: 5 minutes
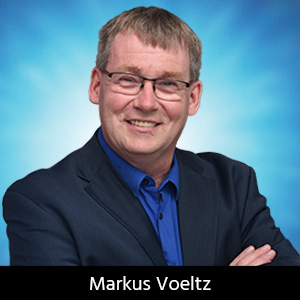
Global PCB Connections: Let the Spec Fit the Board, Not Just the Brand
If you’ve ever seen an excellent PCB quote delayed, or worse, go cold because of a single line on the fab print, you’re not alone. Often, that line reads something like, “Use 370HR only,” or “IT-180A required.” These and other brand-name materials are proven performers, but unless your design needs that specific resin system (say, for RF performance, thermal reliability, or stringent CAF resistance), you may inadvertently be holding your job hostage.
The Problem With Over-Specifying
We train PCB designers to protect the integrity of the product. They want reliability, repeatability, and no surprises on the back end. However, sometimes in the name of safety, we make things harder than they need to be. Over-specifying a material when the respective IPC material specification and class can do the job can put your project in a chokehold, because the PCB fabricator may not stock that exact brand in all core and Cu thickness combinations. Or they used to, but they’ve switched vendors. Or their Asia partner can't source it without a six-week lead time and a minimum buy. Suddenly, that simple “no-brainer” call-out causes days of back-and-forth, engineering holds, or worse, your job gets no-bid. That’s not a vendor problem; it’s a communication problem, and it starts at the drawing.
When a Material Spec Becomes a Roadblock
We see it all the time. A well-intentioned designer using the last successful build as a template carries over the exact stackup and material notes because it worked before. However, what worked with one fabricator in one location may not work across all shops, particularly in global sourcing, where lead times, inventories, and preferred vendors vary widely.
Let’s say you’re a U.S.-based OEM. Your domestic fabricator loves Isola and stocks 370HR and I-Speed in volume. Your drawing says “370HR only,” and they agree. However, when the design shifts to an offshore supplier for production scaling, where fabricators are generally aligned with Shengyi, Ventec, or Panasonic materials, you have now introduced an avoidable friction point. Most offshore fabricators will place the order on hold pending material substitute approvals. The hold can cause critical and unnecessary time delays. Worse, they’ll substitute without telling you.
The Smart Play: Define Performance, Not Brand
IPC-4101 is the industry-standard specification for base materials used in rigid multilayer boards. It includes slashsheets (like /21, /24, /98, /126, etc.) that define resin type, Tg (glass transition temperature), Td (decomposition temperature), CTE, and other critical attributes without locking you into a brand name. For example, if your only concern is a Tg at 170°C, instead of saying, “Use Isola 370HR,” you could specify: “Material to meet or exceed IPC-4101/126. Min Tg: 170°C. UL 94V-0 rated.” That gives your fabricator the freedom to use what they already stock, whether that’s from Isola, Shengyi, Panasonic, Ventec, or NanYa, as long as it meets the performance envelope. This flexibility speeds up quoting, lowers cost, and avoids holds.
When Should You Call Out a Specific Brand?
There are times when brand specificity is critical:
- RF designs where you’ve tuned for a known dielectric constant and dissipation factor—say, Rogers 4350B or Taconic materials
- UL compatibility when your OEM UL file is tied to a specific vendor and stackup
- Thermal reliability of mission-critical environments where material history is part of the validation process
- CAF or high-voltage insulation requirements, for which certain proprietary resins are known to outperform
In these cases, naming the brand is smart, but that’s the exception, not the rule.
Global Sourcing Makes This Even More Important
We work with customers across the globe—from the U.S. to Taiwan, Korea, Europe, and China. One of the most consistent themes is, “The drawing told us what brand to use, but never why.” That puts everyone in an awkward spot. Do we quote with caveats for material lead times? Are we okay to substitute the material using an IPC-4101 equivalent? Do we hold the job and impact the committed ship date?
Some fabricators will skip quoting altogether because they assume the design is not a good fit. That’s not a great way to build strategic supply chain partnerships. However, if your drawing uses IPC material classifications and defines the intent of your performance targets, not just the brand, you widen your pool of viable and quality suppliers.
Example: The Eight-layer Dilemma
Let’s say you have an eight-layer design for an industrial controller. Your last prototype shop used IT-180A, so you write, “Use IT-180A or equivalent” in the notes. That’s not bad, but what’s “equivalent?” One fab might say, “Great, our Shengyi S1000-2 matches.” Another might say, “We need permission to cross.” Another might go back to the customer with 10 questions. Instead, use language like: “Material to meet IPC-4101/126. Minimum Tg 170°C, Td > 330°C. UL 94V-0. Compatible with lead-free assembly.” This gives the fab everything they need and the freedom to move quickly. You’ll still get a reliable board with less back-and-forth questioning.
Let Engineering, Not Habit, Define the Need
Engineers love to document. We’re process-driven creatures, but sometimes our process carries over details that no longer serve the project. A callout made three years ago for one build becomes tribal knowledge, then standard practice, then policy. This is an excellent example of how over-specification happens. The next time you release a fab drawing, ask yourself, “Am I calling out this brand because it’s needed, or because it’s familiar?” If it’s the latter, consider shifting to IPC classifications. Your supply chain partners will thank you, and your project will move faster.
Closing Thoughts: Don’t Let the Label Stop the Line
Materials matter, but so does momentum. We all want consistent performance, excellent yields, and long field life, but we also want speed, flexibility, and scalable sourcing. Define what you need the board to do, not what brand the resin comes from, unless it’s truly non-negotiable. Global supply chains are agile, but only when your documentation is, too.
So, the next time you spec a board, don’t just write a material. Write a mission. Define the performance. Let your fab shop bring their best option to the table, and you’ll be one step closer to a globally scalable build.
Jerome Larez is a field application engineer and director of technical sales with CEE PCB.
More Columns from Global PCB Connections
Global PCB Connections: Understanding the General Fabrication Process—A Designer’s Hidden AdvantageGlobal PCB Connections: Embedded Components—The Future of High-performance PCB Design
Global PCB Connections: Rigid-flex and Flexible PCBs—The Backbone of Modern Electronics
Global PCB Connections: The Next Wave of HDI PCBs– How Design Engineers Can Stay Ahead
Global PCB Connections: A Field Engineer’s Perspective on the Top 10 Trends to Watch
Global PCB Connections: How Technology Can Level the Playing Field
Global PCB Connections: The Future of HDI PCBs
Global PCB Connections: Following DFM Rules Leads to Better Boards