-
- News
- Books
Featured Books
- pcb007 Magazine
Latest Issues
Current IssueSales: From Pitch to PO
From the first cold call to finally receiving that first purchase order, the July PCB007 Magazine breaks down some critical parts of the sales stack. To up your sales game, read on!
The Hole Truth: Via Integrity in an HDI World
From the drilled hole to registration across multiple sequential lamination cycles, to the quality of your copper plating, via reliability in an HDI world is becoming an ever-greater challenge. This month we look at “The Hole Truth,” from creating the “perfect” via to how you can assure via quality and reliability, the first time, every time.
In Pursuit of Perfection: Defect Reduction
For bare PCB board fabrication, defect reduction is a critical aspect of a company's bottom line profitability. In this issue, we examine how imaging, etching, and plating processes can provide information and insight into reducing defects and increasing yields.
- Articles
- Columns
- Links
- Media kit
||| MENU - pcb007 Magazine
Estimated reading time: 5 minutes
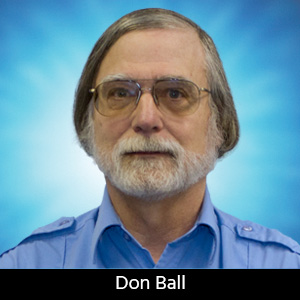
The Chemical Connection: Common Misconceptions in Wet Processing
Initially, I thought an April Fool’s column would be fun this month. I could highlight some of the crazier ideas and misconceptions I’ve witnessed over the years from potential customers and we could all have a good laugh. For example, there was a first-time buyer of a ferric chloride etcher (with no regeneration system) who was astonished to learn that he had to put fresh etchant in the system occasionally to maintain production.
Upon further reflection, I realized that a column that makes fun of one’s potential customers might not be a particularly astute move. However, thinking about the misconception that the ferric chloride etcher would last forever made me realize there are many common misconceptions about etching and wet processing, which would make for a more worthwhile column.
One common misconception is that changing to a different etch chemistry will change the overall etch uniformity of the system being used. Some etch parameters, such as etch rate or etch factor, may change, but the etch profile across the width of the panel will not. Those areas that etch a little more or a little less than others on the panel will still etch a little faster or slower in the same places and with the same proportions, no matter the etchant. For a variety of reasons, the most common change is from acidic cupric chloride to alkaline cupric chloride (alkaline etch). One may expect double the etch rate and better etch factors (although not necessarily), but not a smoother etch profile. This is more dependent on the physical rather than the chemical parameters of the etcher setup. There are reasons one might contemplate changing etch chemistries but getting a better etch uniformity should not be one of them.
Etch factors (the ratio of downward etch to sideways etch, or how straight the sidewalls are) have become more important with the trend toward narrower lines and spaces. Ideas to improve etch factors abound, but here are some of the more common misconceptions that are worth keeping in mind, as they could save you time.
Ferric vs. Cupric
An early misconception was that etching copper with ferric chloride produced better etch factors than cupric chloride. Early on, almost all circuit boards etched copper using ferric chloride because that’s how it had always been done. As circuit board production increased logarithmically in the early years, most manufacturers switched to cupric as the etchant of choice because it could be regenerated, maintaining a constant etch rate and greatly reducing disposal costs. Almost immediately, the issue of which etchant provided the best etch factor was raised and still comes up in discussions today. However, in the mid-1990s, extensive design-of-experiment testing with a manufacturer of lead frames made it clear there was no difference in etch factor between the two. Later tests with circuit boards confirmed this. Sorry guys, simply switching to ferric chloride for your etch factor-critical boards will not solve your problem.
Fan vs. Cone Nozzles
Another misconception almost as old as the industry is that using fan nozzles rather than cone nozzles to deliver the etchant to the board surface results in better etch factors. Again, the lead frame tests showed no difference between the two nozzles. A test using fan nozzles to etch from the top and cones from the bottom revealed no difference in etch factor, either visually or microscopically. Again, sorry, but simply switching to a different nozzle won’t solve your etch factor problem.
Is Alkaline Etchant Better?
While not a misconception, the idea that alkaline etchant will automatically improve your etch factor is not always true. You must run at the lowest pH possible, the highest specific gravity possible within the suggested range, and use a minimum ammonium chloride-to-copper ratio: 2 moles NH4Cl/mole Cu (typical chloride-to-copper ratio is 2.4 to 2.5: 1). This provides the best etch factor but also the slowest etch rate. As you raise the pH and lower the specific gravity to increase etch rate, you lower the etch factor until it is possible to have an etch factor as low as 1:1 (etching as fast sideways as downward). So, you do get a better etch factor with alkaline etch, but it’s not automatic.
This lack of understanding occurred when we replaced an ancient alkaline etcher from a competitor at a company. We immediately received complaints that low etch factors on the new etcher were causing problems. We visited the company and discovered they had two major customers: one with boards with PTFE substrates, the other with normal fiberglass substrates that needed straighter etched sidewalls for whatever frequency those boards were controlling.
When the etchant was configured for the best etch factor (pH 8.0), the other customer’s boards had a grayish coating left on the PTFE substrates. When they adjusted the etchant so as not to leave a coating on the PTFE after etching (pH 8.3), the etch factors were too low to pass specifications for the other customer’s boards.
When I tried to explain this, I was told, “We never had this problem on the old etcher.” The process engineer for the etchant supplier was called in and agreed with my analysis (a pleasant surprise). Again, we were told, “We never had this problem on the old etcher.” We were both familiar with the old etcher and neither of us could see why it would get better etch factors than the new etcher. The problem was eventually solved by adding a mild acid rinse to the line to take care of the gray residue on the PTFE substrates. I later learned the reason they had never had a problem with the old etcher was because they never checked etch factors until they received the new etcher.
There are many more misconceptions about etching and other wet processing steps, but these are the ones I hear about repeatedly.
This column originally appeared in the April 2025 issue of PCB007 Magazine.
More Columns from The Chemical Connection
The Chemical Connection: Sales Organization from a Capital Equipment PerspectiveThe Chemical Connection: Through-glass Vias in Glass Substrates
The Chemical Connection: Reducing Defects in Circuit Board Production
The Chemical Connection: Surface Finishes for PCBs
The Chemical Connection: Earthquakes, Astronauts, and Aquatics—A Lighter Look at the Past
The Chemical Connection: Better Fabs Attract a Better Workforce
The Chemical Connection: Can Changing Spray Nozzles Improve My Etch Quality?
The Chemical Connection: Getting the Best from Your Cupric Chloride Etchant