-
-
News
News Highlights
- Books
Featured Books
- pcb007 Magazine
Latest Issues
Current IssueSales: From Pitch to PO
From the first cold call to finally receiving that first purchase order, the July PCB007 Magazine breaks down some critical parts of the sales stack. To up your sales game, read on!
The Hole Truth: Via Integrity in an HDI World
From the drilled hole to registration across multiple sequential lamination cycles, to the quality of your copper plating, via reliability in an HDI world is becoming an ever-greater challenge. This month we look at “The Hole Truth,” from creating the “perfect” via to how you can assure via quality and reliability, the first time, every time.
In Pursuit of Perfection: Defect Reduction
For bare PCB board fabrication, defect reduction is a critical aspect of a company's bottom line profitability. In this issue, we examine how imaging, etching, and plating processes can provide information and insight into reducing defects and increasing yields.
- Articles
- Columns
- Links
- Media kit
||| MENU - pcb007 Magazine
Estimated reading time: 4 minutes
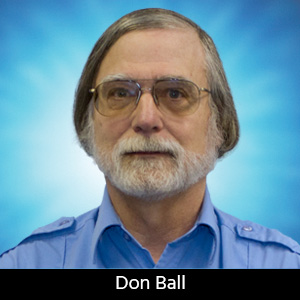
The Chemical Connection: Better Fabs Attract a Better Workforce
Workforce problems are almost as great an issue in PCB manufacturing today as the product quality and reliability of the increasingly complex circuit boards now in demand. I believe they are directly related. A quality workforce makes it easier to produce a quality product. Unfortunately, as an industry, we have not done a good job of attracting quality young people for today’s production requirements.
I’m not an expert in personnel management and don’t have any simple solutions. However, throughout my career, I have visited hundreds of PCB shops around the world and have seen the good, the bad, and the really ugly. Here are my insights on what works and doesn’t work to attract and keep a quality workforce.
The first thing I notice during a visit to a PCB production facility is the working conditions in the production areas. Invariably, good shops are clean, well-lit and well-ventilated. Staff clean up spills immediately and wipe down equipment by the end of the day, if not more frequently. Conversely, the bad and ugly shops are almost always dank and dirty, with who knows what all over the floors, and the outsides of equipment encrusted with chemicals. If you are a young person with salable skills, which shop would you prefer to accept a job offer from? I have visited many shops I wouldn’t work in, even if offered double or triple my current salary. I’ve also noticed that a neat and organized workplace contributes to employee morale and a willingness to go the extra mile to keep production running. That’s why the first thing needed to attract and keep skilled labor is a safe and clean workplace.
Workplace conditions have been contingent on the attitude of the upper management in the shops I have visited. In the good shops, management cares about the health and safety of their employees. They are hands-on and familiar with their production processes. They have written procedures for equipment operation and maintenance and contingencies (for spills, leaks, etc.), and make sure everyone knows those procedures. They know a well-organized workplace is more profitable in the long run.
In the not-so-good shops I have visited, management is more concerned about getting the maximum amount of product out the door in the shortest possible time and counting their profits. They don’t tolerate things that slow down this process (equipment maintenance, cleanup, etc.) and put them off until something breaks. At that point, panic ensues, and there is a lot of running around and yelling until somehow they resolve the problem. Then, they resume maximum production until something else breaks. Employees see management only cares about getting goods out the door. Consequently, they eventually see their chief priority as completing their shift with as few problems or exertion as possible, so they can leave immediately when their shift ends. I’ve found a poorly kept workplace leads to a poorly motivated workforce with little incentive to do any more than is absolutely necessary to keep their jobs.
However, once we have a workplace that is reasonably clean and safe and may attract and keep skilled workers, how and where do we find them? There are no college courses in PCB production and, to the best of my knowledge, no formal training programs or trade schools to teach the skills to become a productive PCB employee. So, where can you find experienced workers, and once you hire them, what kind of training programs can you offer them?
One source may be your suppliers. They have already seen more problems and solutions in their specialized processes than you can imagine. Most will provide a training program in those processes, either in-house or at the supplier’s facility. Some may also provide formal training courses for their specialties in their facilities, or through webinars at a modest price.
Many of the best shops I have visited have some type of mechanism for passing on skills and knowledge from experienced people. Usually, it’s as an apprenticeship, although it’s often not called that. Employees do not move to a new job, promotion, or retirement until they have trained their replacement, so it takes some foresight and planning from the management to implement this. If this doesn’t happen, it puts more strain on the company.
I have found things are smoother when the operators have some understanding of the processes. I’ve seen too many cases where operators kept feeding panels into the etcher and producing scrap simply because they didn’t realize there was a problem. Most of the processes in producing a circuit board are not that complicated and don’t require a college degree to understand them.
Most of the successful shops I have seen combine training offered by their suppliers with internal training and promotion. They then trust those workers to recognize potential problems and bring them to the attention of their supervisors before things get out of hand.
Many of the not-so-good shops try to cut expenses by reducing the number of skilled (and higher-paid) workers to a bare minimum, depending on them to direct lower-paid unskilled workers. This seldom works because spreading skilled supervisors too thin overwhelms and burns them out. Minimum-wage workers don’t care because every problem is above their wage level (and I find it hard to fault them for this). I don’t believe you can produce high-tech products with minimum-wage labor.
Finding and training skilled workers requires companies to train them to become more invested in the industry. When they are invested, workers will want to advance their skills, seek promotions, and help train others. It’s a symbiotic process, and it works when everyone is aligned with the same goals.
This column originally appeared in the January 2025 issue of PCB007 Magazine.
More Columns from The Chemical Connection
The Chemical Connection: Sales Organization from a Capital Equipment PerspectiveThe Chemical Connection: Through-glass Vias in Glass Substrates
The Chemical Connection: Reducing Defects in Circuit Board Production
The Chemical Connection: Common Misconceptions in Wet Processing
The Chemical Connection: Surface Finishes for PCBs
The Chemical Connection: Earthquakes, Astronauts, and Aquatics—A Lighter Look at the Past
The Chemical Connection: Can Changing Spray Nozzles Improve My Etch Quality?
The Chemical Connection: Getting the Best from Your Cupric Chloride Etchant