-
- News
- Books
Featured Books
- smt007 Magazine
Latest Issues
Current IssueMoving Forward With Confidence
In this issue, we focus on sales and quoting, workforce training, new IPC leadership in the U.S. and Canada, the effects of tariffs, CFX standards, and much more—all designed to provide perspective as you move through the cloud bank of today's shifting economic market.
Intelligent Test and Inspection
Are you ready to explore the cutting-edge advancements shaping the electronics manufacturing industry? The May 2025 issue of SMT007 Magazine is packed with insights, innovations, and expert perspectives that you won’t want to miss.
Do You Have X-ray Vision?
Has X-ray’s time finally come in electronics manufacturing? Join us in this issue of SMT007 Magazine, where we answer this question and others to bring more efficiency to your bottom line.
- Articles
- Columns
Search Console
- Links
- Media kit
||| MENU - smt007 Magazine
Step-by-Step - Step 10: Rework & Repair
November 21, 2007 | Bob Wettermann, BEST Inc.Estimated reading time: 6 minutes
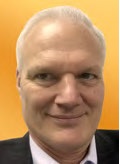
Rework done correctly should meet the specifications and requirements of the original PCB acceptability criteria. The focus of rework is to reprocess the PCB using original or equivalent processing. On the other hand, repair comprehensively refers to modifications completed on the PCB assembly that do not comply with the original design or fabrication criteria. They do not generally meet the specifications and acceptability criteria of the original assembly; however, the PCB is restored to functional capability. Industry standards for rework processes and procedures are catalogued in IPC 7711, while the repair processes are assembled in IPC 7721. Both rework and repair are part of the manufacturing process flow as electronic assembly yields are not 100%.
Rework
There are several methods of supplying the proper thermal energy for reworking soldered connections on a PCB. The most common approach is conductive heating (such as a soldering iron), whereby heat is generated from either a resistive or inductive element and transfers directly to the solder to bring it to its melting point. This approach is cost-effective for most thru-hole and SMT hand-soldering rework operations. Convective heating relies on a hot-air source to heat the part indirectly and is widely used for area-array devices. Infrared (IR) and laser sources are more specialized with IR being an efficient way to reflow the solder on dark-colored packages, which absorb energy into the solder joint, without disturbing smaller adjacent devices with undesired air flow. Laser sources are appropriate when neighboring parts are heat-sensitive or when speed and throughput are of the essence. Resistive heating is used in tweezer handpieces for quickly reflowing passive devices.
Coating removal prior to rework and repair continues to challenge rework operators. There are several widely used methods to remove coatings so that parts can be separated from PCBs, or boards repaired.
One challenge in reworking thru-hole devices has risen to greater prominence due to increased lead-free alloy processing: copper pad dissolution. Excessive solder-contact times, especially when reworking on thicker boards, is a major cause. For proper hole fill and fillet forming during second-pass rework soldering, the correct dwell times for rework, especially with silver/tin/copper (Sn/Ag/Cu - SAC) solder, need to be used.
Figures 1a and b: Damaged traces can be returned to “as new” condition.
SMT rework is fraught with challenges. PCBs are getting denser, with complex stacked and leadless devices appearing with greater frequency. These present innate rework challenges by their mere nature and design. Area-array device (like BGA) rework is further complicated by lead-free shrinking the process window. BGAs with underfill are very time-consuming to rework, and many times the rework process itself is a yield detractor.
Stacked-die rework provides companies with the ability to rework the various stacked packages being adopted in more applications than just the memory-module arena. The process can separate die from one another, or the complete package from the substrate/interposer. The problem here is the ability to control airflow rate, direction, and temperature gradients to such an extent that the stack separates in the required location.
The key to successful leadless-device (i.e. LGA, QFN, and MLF) rework is proper solder paste printing of land areas. The user needs to have extensive experience in stencil design, even when large ground planes exist on the device. At times this type of rework can be accomplished by “bumping” the lands using a polyimide stencil. Larger thermal ground planes, which often sit in the center pad of the QFN or LGA, require the right stencil design. One must take care to have the correct solder volume so as to not let the part float up and off of the board in the center with the perimeter I/Os containing opens.
Higher lead-free solder alloy processing temperatures will bring a few associated consequences to both the BGA and board being reworked. The first of these is that the top of the component body temperature is very close to the rated maximum temperature of the device. Most lead-free BGAs have been qualified to withstand 250°-260°C. In most cases, the top component temperature will be very close to this range, so insuring that this limit is not exceeded is critical to avoid damaging the component. These elevated temperatures will have side effects for the parts on the underside of and nearby to the device being reworked. These include nearby parts being skewed, neighboring parts being discolored or destroyed, or back-side parts falling off.
Lead-free Impact
The move to lead-free alloys has created several challenges for reworking PCBs. Precise thermal management becomes even more critical. Process temperatures in excess of 220°C are reaching the maximum-allowed limit for most components and must be carefully regulated, especially in second reflow post-rework. As most SMT devices will not self-center during lead-free reflow, initial alignment and subsequent package-to-substrate placement become more demanding. More precise placement of area-array devices is required as alloy spread is reduced. When the soldering temperature increases, the coefficient of thermal expansion (CTE) mismatch between the laminate material, the glass fiber, and the copper will exert greater stresses on the copper, potentially causing failures by cracking copper traces or plated vias. Higher rework processing temperatures - approximately 30°-40°C higher - may impact other components that are close to their melting or softening points.
Mixed-alloy Rework
Electronic assemblers must ensure that their material controls are sufficient to produce both tin/lead and lead-free products concurrently, without cross-contamination. Concurrent processing of tin/lead and lead-free products requires that there are process controls in place to prevent processing tin/lead assemblies using the lead-free hand-soldering tools, and vice versa.
There are several challenges in reworking PCBs in a mixed-alloy environment. Namely, assemblers must deal with materials segregation between lead-bearing and lead-free soldering areas, the segregation of lead-free and lead-bearing components in inventory, and tighter control and tracking of moisture-sensitive devices (MSDs). In a per-job approach, each job has materials that are “checked out” from a material control area. For example, the appropriate paste flux, solder paste, and solder wick are released from the material control area for each specific job. Solder technicians can then rinse their soldering iron tip with lead-free solder, gradually reducing lead contamination levels until the same tools can be reused without contaminating an assembly. Most BGAs have a two-fold increase in MSD level compared to their tin/lead counterparts, so MSD control is critical for lead-free processing. Increased internal package-lid pressures will increase the corresponding frequency and magnitude of moisture-related damage. These are just some of the major processing challenges in a mixed-alloy rework environment.
Repair
Several common repairs are getting more complex and requiring higher skill levels due to shrinking board dimensions in modern devices. Land and trace dimensions continue to decrease, with 10-mil or smaller trace patterns that are harder to handle and manipulate into position during the repair process. BGAs lands that are lifted can be 0.020" square and smaller, requiring dexterous technicians to perform repairs.
The impact of mixed-alloy repair environments also has caused users to look at controlling materials and equipment. All of the circuit frames used for trace and pad repair must be compatible with the selected alloy. Furthermore, the materials used for repairs, such as replacement mask, must be able to withstand the higher lead-free processing temperatures.
Bob Wettermann, CIT, BEST Inc., may be contacted at 3603 Edison Place, Rolling Meadows IL 60008; (847) 797-9250; bwet@solder.net.