-
- News
- Books
Featured Books
- smt007 Magazine
Latest Issues
Current IssueMoving Forward With Confidence
In this issue, we focus on sales and quoting, workforce training, new IPC leadership in the U.S. and Canada, the effects of tariffs, CFX standards, and much more—all designed to provide perspective as you move through the cloud bank of today's shifting economic market.
Intelligent Test and Inspection
Are you ready to explore the cutting-edge advancements shaping the electronics manufacturing industry? The May 2025 issue of SMT007 Magazine is packed with insights, innovations, and expert perspectives that you won’t want to miss.
Do You Have X-ray Vision?
Has X-ray’s time finally come in electronics manufacturing? Join us in this issue of SMT007 Magazine, where we answer this question and others to bring more efficiency to your bottom line.
- Articles
- Columns
Search Console
- Links
- Media kit
||| MENU - smt007 Magazine
Solder Paste vs. Flux-only Attachment for BGA Rework
January 5, 2005 | Bob Wettermann, BEST Inc.Estimated reading time: 9 minutes
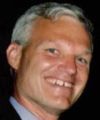
The area array rework process has a real dichotomy between its practical aspects and process theory. From a strict process-engineering standpoint, the proper method for reworking these devices calls for duplicating the original manufacturing process very closely. Following this guideline implies that the device to be reworked should be placed and reflowed using solder paste, and the board/device should be subjected to a very controlled temperature profile, such as those found in modern multiple zone reflow ovens. In addition, the solder paste printing process should be uniform and controlled such as in an automated stencil printing process. Process variables such as squeegee speed, squeegee pressure and snap-off velocity should be closely monitored and controlled. Devices often are placed using only “tacky flux” smeared across the bottom side of the site being reworked. More often, the reworked devices are reflowed using a hot air source with a top-side-only controlled heating source. Proper rework procedures, which should mimic the original manufacturing process to ensure the reliability of the reworked device, have taken a backseat to expediency.
Paste Application Methods
There are numerous practical solder paste application methods for reworking area array devices. The most common method used to selectively apply solder paste in reworking is using a metal or one-time-use plastic film stencil. After the device is removed and the site is prepared, the stencil serves to selectively apply solder paste to the various land patterns or sites on the PCB. These stencils have hole patterns corresponding to the land patterns of the PCB. Solder paste is pushed manually through these apertures using a small squeegee blade. A rework technician will attempt to control as many of the rework paste printing variables as possible, including squeegee pressure, stencil/board release speed and uniformity of solder paste deposition speed. These variables, even with an experienced rework technician at the controls, can only be controlled to a limited extent and is a function of the experience level of the operator. However, the problems of warped PCBs can lead to a poor gasket being formed between the bottom of the stencil and the PCB, leading to “smearing” of the solder paste patterns. Problems in improper perpendicular “lift off” of the squeegee from the site location, as well as the lack of a consistent solder paste volume in each of the apertures, also can lead to shorting between balls, opens and other solder attachment problems. A newer method of solder paste printing in which a polyimide pressure-sensitive tape with hole patterns serves as a semi-permanent stencil on the PCB takes away all of the operator variability (Figure 1). Because the stencil becomes a permanent embodiment of the PCB (like a label), the apertures can be filled with consistent solder paste volumes, and there are no issues related to the perpendicular “lift off,” especially from warped boards. The polyimide material between each of the solder balls also serves to prevent solder shorts. Limitations of this technique include the inability to clean underneath the BGA or CSP, and potentially reduces the ability of the cleaning operation and the ability to perform optical inspection.
Figure 1. Semi-permanent BGA rework stencil speeds reworking process.
Another technique that can be used to selectively apply solder paste to a device rework area is applying solder paste onto the device instead of the board. This technique uses special fixtures and stencils surrounding the part underside while solder paste is printed onto the device prior to placement. This technique allows devices located in high-density areas of the PCB to be reworked. However, costly proprietary fixture systems can limit this technique. Solder paste also can be applied by a dispensing system that lays precisely controlled volumes of solder paste in specifically pre-programmed X-Y locations on a PCB. This method deposits and controls the paste deposition. Slow cycle rates, long programming times and solder paste chemistry limitations make this a seldom-used technique.
Flux-only Application Methods
There are several techniques that are used to apply “tacky flux” to the area array device being reworked. The most common technique involves using a syringe to dispense the flux onto the pad areas, followed by “smearing” the flux with a brush or fingertip over the entire surface onto which the part will be placed. This method of applying flux is fast and easy to understand. However, there is risk to the long-term reliability of this interconnection as excessive flux residue may reduce the surface resistivity of the PCB surface. Semi-permanent, metal or plastic stencils can be used to apply the flux. This results in flux being deposited only where it is needed. The use of the semi-permanent stencil electrically isolates each of the pads as the polyimide wells act as dielectric barriers between each of the pads. Dipping the part into the flux and placing it onto the PCB also can accomplish this flux-only application (Figure 2). All of these flux-only applications have shortfalls as they cannot compensate for the lack of co-planarity in either the part or the PCB. They instead must rely on the solder volume of the device balls only to make up for changes in planarity. Because more opens can result, this, in turn, leads to a reduction in the reliability of the solder joint.
Figure 2. Flux dipping of BGA.
This study was meant to determine the reliability affects of using either the solder paste or flux-only attachment method in the BGA rework process. Also, the study was commissioned to determine what effect the presence of a semi-permanent stencil had on the reliability of a reworked BGA.
Testing
The test method for this study included measuring resistance values of reworked stencil-printed BGA test samples made both with and without the semi-permanent stenciling method after thermal shock cycles. These same tests were carried out using a flux-only reworked BGA.
Each of the test cards was exposed to a thermal shock exposure test. Test cards were cycled between -45° and 70° C with a 10-min. per segment and a 40-min. per cycle dwell. Between each of the 500 cycles, there was a transition time of less than 15 seconds. Each of the daisy-chain segments were monitored and manually measured for resistance values initially, and at intervals up to 500 cycles. A 20% increase in the resistance of any segment constituted a failure.
After 500 thermal shock cycles, it was noted that the standard flux-only attachment group was the only group with failures, having 24 of 80 circuits fail and failure on four out of five cards.
Surface insulation resistance (SIR) test measurements were performed and compared on samples both with and without the semi-permanent stencils. There was no degradation in the SIR test results in either the solder paste or the semi-permanent stencil printed samples.
There was an observed reliability difference between the use of solder paste and flux-only attachment methods in the rework process (Table 1). This has been observed in other studies and is likely the result of additional solder volume in the solder paste printing process.
The data indicates that after 500 thermal shock cycles there was no detrimental impact on interconnect reliability in the case of semi-permanent stencil reworked vs. standard-paste application reworked BGAs (Table 2). Additional testing or more cycles would help to determine if there are any differences in reliability between the metal stencil solder paste printing rework process and its semi-permanent counterpart.
Flux-only: A Reduction in Solder Joint Reliability
There are several key points to keep in mind with respect to the use of flux only in the rework process that can cause the reliability of the reworked joint to be compromised. These include, but are not limited to, solder joint size, standoff height underneath the package and the lack of height compensation for the part or board co-planarity.
The size of the solder joint will be smaller after reworking the part with flux only compared to a paste-print attached part. Decreased solder volumes of BGA joints have been shown to have lower mechanical reliability than those with greater volumes.
The standoff height from the bottom of the part to the surface of the PCB is reduced when using the flux-only attachment technique. The resulting reduction in heat dissipation causes the part to heat up locally and experience greater thermal stress, thereby reducing the expected solder joint life.
Another reason that the use of flux-only in the BGA rework process reduces the longevity of the interconnect life is that it fails to make up for the differences in planarity. If either the part or the PCB becomes warped due to unevenness in heating, either surface can be non-planar. With the reliance on only the solder ball volume to compensate for a lack of planarity, the likelihood of an open connection increases.
Paste: Better Performance for Reworked Parts
There are several reasons for the improved performance of paste-printed reworked BGAs compared to their flux-only attached counterparts such as increased solder volume and compensation for the lack of part or board co-planarity in solder attachment.
Increased solder paste volumes due to the use of the solder paste attachment process have several advantages in the BGA rework process. Several studies have indicated that a greater standoff distance between the part and the PCB leads to more efficient localized heat dissipation as a part goes through its thermal cycles1.
Increased solder paste volume can also increase PCB co-planarity defects. Thinner PCB substrates, localized ground plains or uneven heating of the PCB during the rework process can all lead the board to warp. Large BGA package sizes, as well as poor quality control in solder ball dimensions, also can cause co-planarity discrepancies along the part underside. Poor co-planarity in either the PCB or the part surface can lead to opens or uneven collapse, and even no connects after reflow. Increased solder paste volumes overcome these height differentials in the rework process, which leads to more reliable interconnects.
Semi-permanent Stencils
The semi-permanent solder paste printing technique lets users realize the reliability of solder paste printing while experiencing the convenience of the flux-only attachment process. This study indicates that there are no differences between the interconnect reliability of a metal stencil and semi-permanent stenciling technique. Solder paste “skips” or insufficient solder paste volume, as well as poor part co-planarity are mentioned in the “Top Ten Causes of BGA Assembly Defects” as the main causes of BGA placement defects2. Greater volumes afforded by the semi-permanent stenciling technique provide for an improved standoff distance and a more reliable joint. In addition, the semi-permanent stenciling technique helps compensate for differences in the part and board co-planarity effects.
The difference in rework process time between a flux-only and a semi-permanent solder paste printing rework job is negligible. The negatives of paste screening on the board for rework include limited room for local screening, poor print releases when lifting the rework stencil and the need to clean the rework stencil after each use.3 All of these negatives are overcome with the newer “semi-permanent” stencil method.
The difference in processing time between a flux-only and a semi-permanent solder paste attachment rework job also is negligible. The negative aspects of standard paste screening on the board for rework also are limited room for local screening, poor print releases when lifting the local site stencil and the need to clean the entire PCB. All of these negatives in the solder paste printing process are overcome with the newer “semi-permanent” stencil method, as well as the benefit of a more reliable solder joint.
References
- ”BGA Reliability Characterization Project Temperature Cycling Tests Final Report,” David Love and David Towne, High Density Packaging User Group International, January 1999.
- Digital DNA Motorola BGA Application Guide, Motorola 2003.
- CBGA Surface Mount Assembly and Rework User’s Guide, IBM 2002.
For a complete list of references, please contact the author.
Bob Wettermann, president of BEST, may be contacted at 3603 Edison Place, Rolling Meadows, IL; (847) 797-9250; e-mail: bwet@solder.net.