-
- News
- Books
Featured Books
- smt007 Magazine
Latest Issues
Current IssueSpotlight on India
We invite you on a virtual tour of India’s thriving ecosystem, guided by the Global Electronics Association’s India office staff, who share their insights into the region’s growth and opportunities.
Supply Chain Strategies
A successful brand is built on strong customer relationships—anchored by a well-orchestrated supply chain at its core. This month, we look at how managing your supply chain directly influences customer perception.
What's Your Sweet Spot?
Are you in a niche that’s growing or shrinking? Is it time to reassess and refocus? We spotlight companies thriving by redefining or reinforcing their niche. What are their insights?
- Articles
- Columns
- Links
- Media kit
||| MENU - smt007 Magazine
Estimated reading time: 4 minutes
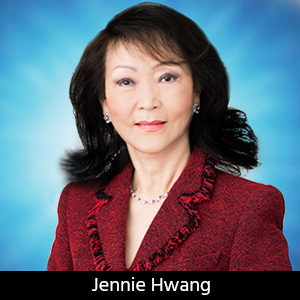
Reliability of Lead-Free System: Part II, The Role of Creep
Editor's Note: This column originally appeared in the September 2011 issue of SMT Magazine.
Like other materials, solder joints do wear out during their service life. This degradation process is unavoidable. The objective of solder joint reliability is to make sure that solder joints do not degrade to the level that loses its required functionality--be it electrical, thermal or mechanical--under a designated service life and anticipated service environments.
Barring other extraneous causes, this solder joint intrinsic degradation process engages two scientific phenomena--fatigue and creep. (For the purpose of this discussion, other extraneous causes include the improperly formed solder joints due to wetting problem, inadequate process issue, surface finish-induced problem at or near the interface, such as Au-embrittlement, and other intermetallic issues, etc.)
However, for the real-world performance of electronics, the solder joint intrinsic degradation, and, thus, an eventual failure, is hardly a creep failure or a fatigue failure--instead, it is the result of interactive fatigue and creep. The mechanisms of creep and fatigue are expected to operate in a competitive, alternative or mutually-promoting manner, depending on the service conditions that combine both the external climate and the in-circuit operation environment. In the commonly-adopted accelerated temperature cycling test, the creep and fatigue processes also operate interactively. From an engineering perspective, one can consider the degradation phenomenon as either creep-aggravated fatigue or fatigue-accelerated creep.
Separately, each of these two phenomena is associated and controlled by a different set of parameters in micro-structural, as well as atomic-level, material properties.
In contrast to fatigue, solder creep is defined as a time-dependent deformation, which is irreversible and global.
When stress is applied and sustained, solder responds with an instantaneous strain in the elastic and/or plastic region. As time progresses, solder may continue to deform in a time-dependent manner and eventually fail. Theoretically, this time-dependent deformation can occur at a temperature above the absolute zero, albeit very slowly. In the low-temperature region, the creep strain is very limited and deformation normally does not lead to eventual rupture. The strain accumulates in a logarithmic rate. In the high-temperature region, the creep curve departs from the logarithmic relationship (Book: [ISBN 0 901 150 401] “Environment-Friendly Electronics – Lead-Free Technology,” Electrochemical Publications, LTD, Great Britain, 2001, pp. 73-77, 182.)
A typical creep curve (deformation versus time) comprises three stages--primary, secondary and tertiary. In the primary stage, the transient strain rate decreases rapidly from a very large initial value due to structural alterations when a solder deforms. The secondary creep prevails at the temperature above the half of the alloy’s melting temperature and correlates well with the self-diffusion process. The dislocation climb or glide is generally considered to be the rate-determining step. The creep rate in this stage reaches a steady state, as a result of a balance between two competing metallurgical processes--strain hardening and recovery (a softening effect). The more the solder is plastically deformed, the more difficult it becomes to continue the deformation. The work hardening operates through the generation and the interaction between dislocation defects acting as obstacles to further the deformation process. At higher temperatures, work hardening may be partially- or fully-counteracted by recovery. Under this condition, a time-dependent, thermally-activated, strain-energy-releasing softening process occurs. The deformation reaches a dynamic steady state in which the rate of work hardening is equal to the rate of recovery.
The actual shape of a creep curve varies with the stress level applied and the temperature exposed; some creep curves may not display all three stages. (Publication: Jennie S. Hwang, “Solder Joint Reliability – Can Solder Creep?” International Symposium of Microelectronics, 1989, pp. 38-45.) The creep curves for a variety of lead and lead-free alloy systems were obtained (Book: [ISBN 0-07-031749-6] “Modern Solder Technology for Competitive Electronics Manufacturing,” McGraw-Hill, New York, 1996, pp. 84-96).
When the softening effect and rising stress overcome the strain hardening, the tertiary stage sets in, where the creep rate accelerates until the rupture occurs. This stage is normally associated with structural changes such as the onset of recrystallization, coarsening and formation of internal cracks and/or voids that are precursors to fracture.
Solder joints in electronics are exposed to the conditions that induce both fatigue and creep processes, and they operate interactively. Simply put, this environment can be considered as creep under cyclic thermal loading or fatigue under high temperature. This interactive nature between creep and fatigue complicates the solder joint degradation behavior and the underlying failure mechanism.
The next column in this series will discuss the predominating parameters and conditions that promote either of the two failure mechanisms--creep-aggravated fatigue or fatigue-accelerated creep.
Dr. Hwang, a pioneer and long-standing contributor to SMT manufacturing since its inception as well as to the lead-free development, has helped improve production yield and solved challenging reliability issues. Among her many awards and honors, she has been inducted into the WIT International Hall of Fame, elected to the National Academy of Engineering and named an R&D-Stars-to-Watch. Having held senior executive positions with Lockheed Martin Corporation, Sherwin Williams Co., SCM Corporation and IEM Corporation, she is currently CEO of H-Technologies Group providing business, technology and manufacturing solutions. She is a member of the U.S. Commerce Department’s Export Council, and serves on the board of Fortune 500 NYSE companies and civic and university boards. She is the author of 300+ publications and several textbooks and an international speaker and author on trade, business, education and social issues. Contact her at (216) 577-3284; e-mail JennieHwang@aol.com.
More Columns from SMT Perspectives and Prospects
SMT Perspectives and Prospects: Warren Buffett’s Perpetual Wisdom, Part 2SMT Perspectives and Prospects: Warren Buffett’s Perpetual Wisdom, Part 1
SMT Perspectives and Prospects: Artificial Intelligence, Part 5: Brain, Mind, Intelligence
SMT Perspectives and Prospects: Artificial Intelligence, Part 4—Prompt Engineering
SMT Perspectives and Prospects: The AI Era, Part 3: LLMs, SLMs, and Foundation Models
SMT Perspectives and Prospects: A Dose of Wisdom
SMT Prospects and Perspectives: AI Opportunities, Challenges, and Possibilities, Part 1
SMT Perspectives and Prospects: Critical Materials—A Compelling Case, Part 3