-
- News
- Books
Featured Books
- pcb007 Magazine
Latest Issues
Current IssueInventing the Future with SEL
Two years after launching its state-of-the-art PCB facility, SEL shares lessons in vision, execution, and innovation, plus insights from industry icons and technology leaders shaping the future of PCB fabrication.
Sales: From Pitch to PO
From the first cold call to finally receiving that first purchase order, the July PCB007 Magazine breaks down some critical parts of the sales stack. To up your sales game, read on!
The Hole Truth: Via Integrity in an HDI World
From the drilled hole to registration across multiple sequential lamination cycles, to the quality of your copper plating, via reliability in an HDI world is becoming an ever-greater challenge. This month we look at “The Hole Truth,” from creating the “perfect” via to how you can assure via quality and reliability, the first time, every time.
- Articles
- Columns
- Links
- Media kit
||| MENU - pcb007 Magazine
Estimated reading time: 4 minutes
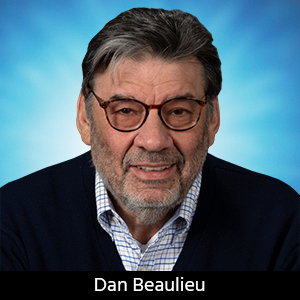
It's Only Common Sense: You Get What You Pay For
Editor's Note: To listen to Dan's weekly column, as you've always done in the past, click here. For the written transcript, keep reading...In last week’s column I discussed the pride some customers have in buying the cheapest products available. For some reason, companies feel they can buy the cheapest parts they can get their hands on and then turn around and tell their customers that the products they produce are the best in the world. No matter how hard you try, you just can’t make filet mignon out of chuck steak--it’s impossible. Just try to make a first-in-class MRI using the cheapest parts you can find.
Any way you cut it, cheap is cheap; and cheap is inferior. With that in mind, I thought it would be interesting, as well as informative, to remind you what you get when you go cheap; when good enough is good enough. Listed below are the true costs that occur when a board is late; when it is rejected and returned to you by a customer; when a board must be rebuilt; or, worst of all, when a field failure occurs.
For those of you who like to bury your head in the sand when buying as cheap as possible, I warn you to turn away. This is not going to be pretty.
What is the Cost of a Late Board?
Customers who buy quick-turn PCBs do so for a reason. They need boards on time and are willing to pay a premium for that service.
When a board is late, the customer:
- Must scrap his schedule;
- Misses the due date to his customer;
- Misses revenue projections;
- Spends more money on overtime to get the boards assembled;
- Must make other plans and pay twice for the boards;
- Possibly misses a product introduction;
- Misses showcasing a product at a trade show;
- Loses out to competitors;
- May hold up a million-dollar shipment for a few thousand cheap circuit boards on which he saved a few hundred dollars;
- Loses credibility with their customer;
- The company buyer loses credibility with his team.
What is the Cost of a Rejected or Returned Board?
All of the above-mentioned issues apply, but everything is much worse:
- It takes additional time to get deposition. That’s why getting CARS in time is so important.
- Time is lost to make new boards.
- The customer could miss time-to-market goals.
- Lost credibility.
- Boards must be replaced faster than ever, free of charge.
- Increased risk of errors when rushing to rebuild boards.
- Reputation comes into question.
- Chances of getting return business from the customer is dramatically decreased.
- The customer’s chance of getting more business is reduced.
What Does it Cost to Rebuild a Board?
The repercussions of losing a part number and having to rebuild a board can be extreme, especially when you specialize in quick-turn PCBs. Consider:
- The cost of the lot to begin with: Materials, labor, and time.
- The cost of the rebuild: Materials, labor, and time.
- Opportunity costs--the rebuild is taking up time that could have been used for another customer.
If the boards are late or you can’t build them in time to meet the delivery date, then:
- You face a loss of premium dollars.
- You’ll pay more to ship the late boards.
- You’ll lose the customer’s good will and possibly lose the customer.
- You could lose your reputation as a great QTA company.
- Your salespeople will have a hard time getting more business from the customer.
- You lose the customer’s confidence.
Then there is the customer. What is the loss to him when he doesn’t receive his product on time?
- Loss of revenue because the customer cannot ship the end-product, a product often worth thousands of dollars more than your boards.
- The possible loss of premium dollars he paid to get components and other commodities in quickly to make deadline.
- Loss of labor time as he brings in people to work on PCBs that aren’t there.
- Loss of reputation.
- Loss of time-to-market, which is so important in new product development.
- Possible loss of marketing expenses; marketing that claimed his product would be delivered on a set date.
To miss a delivery date is a very big deal at any price. Customers pay premium dollars for a reason and often that reason is time.
What do Field Failures Cost?
All of the above, but on double steroids:
- Extremely high visibility (Challenger/ New Boeing Dreamliner).
- Lives possibly lost. It can literally be life or death.
- Medical? Think about it: Do you want field failures in medical devices?
- Your company’s reputation can be destroyed and put you out of business.
So think about these things the next time you’re tempted by price. The next time you’re about to buy that cheap board from Asia--you know the one, the one built buy the cheapest labor money can buy (and still not be considered slavery), ask yourself if this is really the only price you’ll be paying or if you’ll be paying a much higher price in the long run. And then ask yourself if you’re really proud that you were able to use the cheapest parts money can buy to put into your great product. Are you really proud of that?
It’s only common sense.
More Columns from It's Only Common Sense
It’s Only Common Sense: Why Failure Is an Opportunity for GrowthIt’s Only Common Sense: Stop Chasing New Customers and Start Keeping the Ones You Have
It’s Only Common Sense: Sales as a Team Sport
It’s Only Common Sense: How to Win Back Lost Customers
It’s Only Common Sense: Knowing When to Walk Away
It’s Only Common Sense: Customer Service Is Sales in Disguise
It’s Only Common Sense: Your Guide to Better Time Management
It’s Only Common Sense: Selling to Today's Generation of Buyers