-
- News
- Books
Featured Books
- pcb007 Magazine
Latest Issues
Current IssueInventing the Future with SEL
Two years after launching its state-of-the-art PCB facility, SEL shares lessons in vision, execution, and innovation, plus insights from industry icons and technology leaders shaping the future of PCB fabrication.
Sales: From Pitch to PO
From the first cold call to finally receiving that first purchase order, the July PCB007 Magazine breaks down some critical parts of the sales stack. To up your sales game, read on!
The Hole Truth: Via Integrity in an HDI World
From the drilled hole to registration across multiple sequential lamination cycles, to the quality of your copper plating, via reliability in an HDI world is becoming an ever-greater challenge. This month we look at “The Hole Truth,” from creating the “perfect” via to how you can assure via quality and reliability, the first time, every time.
- Articles
- Columns
- Links
- Media kit
||| MENU - pcb007 Magazine
Estimated reading time: 4 minutes
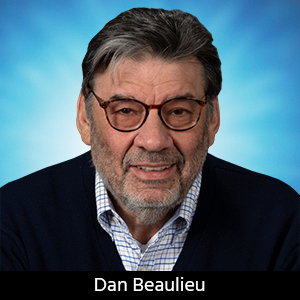
It's Only Common Sense: Where's All the Talent Gone?
Editor's Note: To listen to Dan's weekly column, as you've always done in the past, click here. For the written transcript, keep reading...When I started in this business so many years ago, calculators were the size of anchors and computers were kept in glass booths and worked by wizards in white coats, and our industry had plenty of 20-, 30-, and 40-year olds who knew how to build boards. These folks not only knew how to build boards, but they also knew the science of building boards.
I was fortunate enough to begin my career at a Rockwell International facility called Maine Electronics. When I went to work there, Rockwell had just bought the company, Maine Research, from a genius named Dmitri Grabbe. Some considered Maine Research, and then Maine Electronics, the most advanced circuit board fabricator in the world.
We were building high-tech boards for the Minuteman, the F-111, the Motorola Viking Program, and all the boards that went into the Shuttle guidance system since Rockwell was, of course, the prime contractor on that program.
Rockwell decided to close their California PCB facility and move to Maine for two reasons: Better technology and more competitive wages. Back then companies looked for their “China” in other parts of the country and if you were a manufacturer in California, states like Maine were your China.
Because our company had its start as a research facility, Grabbe staffed it with the smartest people he could find. Many of them stayed there after he sold the company and went to work for Rockwell. Then again, because Maine Electronics was replacing the California board shop, many of their people, especially the technical people from that division, moved to Maine to work at our facility.
This meant that we had a tremendous technical talent base at our company. We had people with degrees in chemistry, electronics, and physics running around our facility and exposing those of us who were just starting out to a great deal of knowledge about our technology and our industry. Many of the young men and women I started with at Maine Electronics eventually ended up working for companies such as Honeywell and Martin Marietta in technical positions (yours truly excluded--I decided to take a different non-technical path, but I owe much of what I know to those experts). These professionals went on to provide valuable technical experience to the companies--both OEMs and other board fabricators--they went to work for.
And ours was not a unique situation--not by a long shot. Other companies such as Photocircuits, the original Advanced Circuits in Minnesota, Graphico in Canada, and a number of others were also pushing the technology envelope with educated, technical professionals leading the way and developing what is today a mature $50 billion dollar industry. They made the industry what it is today--from the first multilayer to the first plated through-hole, from controlled impedance to blind and buried vias.
Flash forward to a couple of weeks ago, when a friend and I were talking about finding technical help for his board shop. I brought up these people, these professionals we grew up with. At one point, I even used the word “methodizer.” Remember that title? We both agreed we had to find people like that to fill the opening he had in his company. But after doing the math, we realized that such people were long gone. If they were in their 30s and 40s when we were in our 20s, and that was 30 or so years ago, unless they were still working in their 80s, they were gone.
Then we thought about the people we knew in the business today and realized that those of us who were in our 20s then are hitting our 60s now and there are very few people behind us. If we look around, we might spot some in their early 50s and maybe a few in their late 40s, but after that..well, after that it gets pretty scary. If you look back over your shoulder today, you’re not going to find too many young people following in your footsteps.
This is a big problem for the PCB industry in America. When you talk to young people today you seldom, if ever, hear any of them say, “When I grow up, I want to work in a printed circuit board shop.” Or “I’m going to college so that I can learn how to build printed circuit boards."
We can worry about Asian competition and we can worry about not having enough business or we can worry about our North American vendor base, but the biggest challenge we face is that of getting new blood into our companies. We must face the challenge of getting young people interested in being a part of our industry and in all facets of our industry, not only technology, but operations, quality, and sales. What are we going to do about this? Do you have any ideas? If you have found a way to meet this challenge I’d love to hear from you.
Meanwhile, I’m going to dedicate the next two columns to this subject. Next week’s column will address how we can find and train young people to grow in our companies. Two weeks from now I’d like to be able to publish any ideas sent in by readers--it would be good to hear from you for a change.
This is an issue we must face now, before it’s too late. Think about it and we’ll talk more in the weeks to come.
We need to do something about this if we're going to preserve our future. It’s only common sense.
More Columns from It's Only Common Sense
It’s Only Common Sense: Why Failure Is an Opportunity for GrowthIt’s Only Common Sense: Stop Chasing New Customers and Start Keeping the Ones You Have
It’s Only Common Sense: Sales as a Team Sport
It’s Only Common Sense: How to Win Back Lost Customers
It’s Only Common Sense: Knowing When to Walk Away
It’s Only Common Sense: Customer Service Is Sales in Disguise
It’s Only Common Sense: Your Guide to Better Time Management
It’s Only Common Sense: Selling to Today's Generation of Buyers