-
- News
- Books
Featured Books
- pcb007 Magazine
Latest Issues
Current IssueInventing the Future with SEL
Two years after launching its state-of-the-art PCB facility, SEL shares lessons in vision, execution, and innovation, plus insights from industry icons and technology leaders shaping the future of PCB fabrication.
Sales: From Pitch to PO
From the first cold call to finally receiving that first purchase order, the July PCB007 Magazine breaks down some critical parts of the sales stack. To up your sales game, read on!
The Hole Truth: Via Integrity in an HDI World
From the drilled hole to registration across multiple sequential lamination cycles, to the quality of your copper plating, via reliability in an HDI world is becoming an ever-greater challenge. This month we look at “The Hole Truth,” from creating the “perfect” via to how you can assure via quality and reliability, the first time, every time.
- Articles
- Columns
- Links
- Media kit
||| MENU - pcb007 Magazine
Estimated reading time: 7 minutes
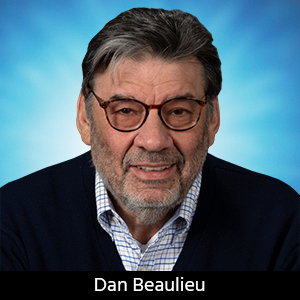
A Conversation with... ASC's Dave Lackey
American Standard Circuits (ASC) is one of the fastest growing PCB shops in North America. Technology is a key factor contributing to its growth. A few years ago, when Anaya Vardya became CEO of the company, he decided, along with owner Gordhan Patel, the way to grow and thrive in this economy was to drive the company toward not only high-technology, but a wide variety of technologies, from rigid to flex-rigid boards, metal-backed and RF boards, as well as other new technologies using new materials and laminates.
Vice President of Business Development and Technical Sales David Lackey is the company's resident guru when it comes to flex and rigid-flex technology. I recently sat down with him to discuss the technology and its importance to American Standard’s growth and industry growth in general.
Dan Beaulieu: Dave, good talking to you today. Thanks for taking the time. Tell me about your company, especially when it comes to flex and rigid-flex.
Dave Lackey: ASC has been manufacturing PCBs since 1988 and over seven years ago we began building flex and rigid-flex PCBs, a very good direction for us. We are starting to see a lot of interest from our customers--they are trying to get away from wire and incorporate a more reliable connection using flex circuits. We do simple, single-layer flex with LPI or cover-layer up to high-layer-count rigid flex. We keep a fair amount of flex materials in stock and warehoused locally to allow us to respond to quick-turn opportunities in the flex market delivering product in less than five days on many occasions. Our goal is to make it as easy as possible for our customers to design in rigid-flex boards into their products.
Beaulieu: What do you mean by that?
Lackey: Well, in the past, customers had a hard time finding good rigid-flex suppliers. They considered it a hassle to even try to buy flex boards so they designed around them, even though the ultimate product would have benefited by having flex boards. They told us about this and we set about working on being not only the best, but the easiest flex supplier to deal with in North America.
Beaulieu: Dave, can you tell me about your background in the industry? I know you've been around for a number of years and I am always interested in knowing how people got to where they are.
Lackey: I've been doing this for quite a while. I've been manufacturing PCBs since 1980 and have worked in various shops including the captive shop that used to be at Northrop Grumman. A fair amount of my experience has been in shops with military certifications and higher technology. Apart from flex and rigid-flex, I also have a lot of experience building metal-core boards and PCB’s requiring thermal management solutions. Having worked in most departments throughout the years, I've developed a strong engineering background and am knowledgeable in most industry technologies. I spend most of my time in sales now and my background allows me to work not only with buyers, but design engineers and quality and manufacturing personnel as well. This approach tends to satisfy most of the customers' request or questions without having to deal with multiple visits, e-mails, or calls and give customers answers on the spot.
Beaulieu: So your role is more technical sales or maybe applications engineering?
Lackey: Yes, that is correct. Having been the general manager at many PCB facilities, including ASC, I have a strong understanding of not only what our facility needs to be successful, but also what our customers expect from us a supplier of PCBs.
Beaulieu: So ASC is able to handle just about all flex requirements?
Lackey: Pretty much--although we can’t be everything for everybody. American Standard rarely turns away from an opportunity. One of the challenges with flex and rigid-flex is material handling and processing without damaging the product--this is critical. Since we have dealt with fragile and thin-core RF materials for so many years this was a definite advantage. We have developed way to handle the material making sure that it is not damaged during the process. Even though this seems to be a simple thing, it's not...I can assure you. Another concern is registration. Getting good registration on flex boards is very difficult, but because we have invested in all of the necessary equipment and tools, we are in a position to deal with it. In the end, our success is due primarily to our having committed to extensive training on handling and processing of thin cores and we continue to invest in the people and equipment necessary for serving the flex marketplace.
Beaulieu: How has flex technology evolved over the years?
Lackey: I started building flex circuits in 1983. The biggest difference I see between then and now is that there's a lot more rigid-flex now than in the past, which allows designers to utilize BGA and fine-pitch devices on the rigid area yet have the flexibility to use the flex portion to package their devices in confined areas. As we've seen through technology, packaging of electronic devices tends to get smaller and lighter. Flex circuits are a perfect solution to accomplish both. Other changes are the availability of more flex laminate manufacturers and different materials that meet UL criteria, allowing for adhesive-less builds. Additionally, some of the press pad and release materials used for bonding of cover layers and flex multilayers have improved over the years, allowing for improved conformal adhesion to the circuitry and removal of entrapped air along with reduction of adhesive flow onto pads.
Beaulieu: Can you tell us about your customers? What sort of flex applications are out there?
Lackey: We see a wide variety of requirements from our customers, from military and medical devices to simple, single-layer flexes connecting one device to another.
Beaulieu: What advantages does rigid-flex have over normal rigid boards?
Lackey: Packaging and reliability. Rigid-flex boards allow for tighter packaging and the means of connecting multiple devices together without using bulky connectors and multiple PCBs. You ultimately end up with a more reliable product that can be accommodated in tight spaces. Many designers may feel the overall cost of a rigid-flex PCB verses using multiple rigid boards, connectors, and wires is not worth pursuing; however, in many studies we did for our customers depending on the design and use of a rigid-flex replacement the total overall cost and certainly the reliability is usually justifiable.
Beaulieu: What are the major differences between building a flex or rigid-flex board as opposed to building a traditional rigid board?
Lackey: The major differences, other than some varying processes, are registration concerns and handling. Registration is a concern on all PCBs, but given the nature of flex material in itself having proper registration equipment and tools is a major necessity. Handling of the material in itself is a significant challenge. Special material handling carts or trays and training your operators in how to deal with these fragile layers is a must.
Beaulieu: Where do you see the industry going when it comes to flex technology?
Lackey: It's definitely growing. It comes down to reliability of a flex or rigid-flex circuit used as a connector verses wires and the ability to put together a tighter cleaner package for devices. A well laid out design utilizing flex or rigid flex can not only provide the necessary reliability, but also reduces assembly time and rework.
Beaulieu: Why should customers come to you for their flex and rigid-flex boards?
Lackey: In addition our experience and ability to provide a quality flex product we have the ability to do quick-turn builds when necessary. We offer solutions to our customers and their design and packaging engineers who might need assistance with material selections (what can and cannot be done with flex circuits) and we always keep cost in mind. Our goal is to be a total solutions provider not only with our flex offering, but with all of our technologies as well. No customer is too small for American Standard. We have a well-staffed group of talented engineers and a number of outside resources to assist customers early on in the design phase and oftentimes offer alternative options upon receiving a finished design as a method of reducing cost or providing a solution that can provide increased yields.
Beaulieu: Dave, thanks for talking with me today. I appreciate the time you took out of our busy schedule.
Lackey: No problem, Dan. Thank you.Not many companies can do all that American Standard Circuits can and this is why they are succeeding while other companies are struggling. But there is a lesson for all of us here: If we want to succeed in the PCB business we must put the customer first.
For more information, visit www.asc-i.com or contact Dave Lackey.
More Columns from It's Only Common Sense
It’s Only Common Sense: Why Failure Is an Opportunity for GrowthIt’s Only Common Sense: Stop Chasing New Customers and Start Keeping the Ones You Have
It’s Only Common Sense: Sales as a Team Sport
It’s Only Common Sense: How to Win Back Lost Customers
It’s Only Common Sense: Knowing When to Walk Away
It’s Only Common Sense: Customer Service Is Sales in Disguise
It’s Only Common Sense: Your Guide to Better Time Management
It’s Only Common Sense: Selling to Today's Generation of Buyers