-
- News
- Books
Featured Books
- smt007 Magazine
Latest Issues
Current IssueSupply Chain Strategies
A successful brand is built on strong customer relationships—anchored by a well-orchestrated supply chain at its core. This month, we look at how managing your supply chain directly influences customer perception.
What's Your Sweet Spot?
Are you in a niche that’s growing or shrinking? Is it time to reassess and refocus? We spotlight companies thriving by redefining or reinforcing their niche. What are their insights?
Moving Forward With Confidence
In this issue, we focus on sales and quoting, workforce training, new IPC leadership in the U.S. and Canada, the effects of tariffs, CFX standards, and much more—all designed to provide perspective as you move through the cloud bank of today's shifting economic market.
- Articles
- Columns
- Links
- Media kit
||| MENU - smt007 Magazine
Tin Whisker Risk Assessment of a Tin Surface Finished Connector
March 18, 2015 | David Hillman and Ross Wilcoxon, Rockwell CollinsEstimated reading time: 2 minutes
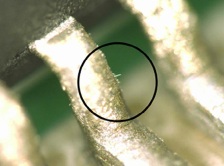
Rockwell Collins initially investigated and qualified Samtec’s SEARAY solder charge connector (hereafter referred to as "the connector") technology with a focus on solder joint integrity. However, the connector in question, which has a matte tin finish on the solder tail, was found to have a potential risk of tin whiskers due to a small region of the connector that was not protected by either solder poisoning or the connector’s mechanical configuration.
An investigation was conducted in accordance with modified JESD201 tin whisker susceptibility protocols to assess the possible tin whisker risk concern. The investigation results, coupled with plating and reflow soldering data inputs, demonstrated that the connector’s tin whisker risk was extremely low and deemed acceptable.
Background
The implementation of the RoHS European Union Directive in 2005 led to the use of pure tin as an accepted surface finish for PCBs and component terminations. A drawback of pure tin surface finishes is the potential to form tin whiskers. Tin whiskers are a metallurgical phenomenon that is associated with tin rich/pure tin materials and has been a topic of intense industry interest.
The acceptance and usage of pure tin by the electronics industry component fabricators is understandable as the pure tin surface finishes are inexpensive, are simple plating systems to operate and have reasonable solderability characteristics. However, the commercial electronics segment, which uses the majority of electronic components, often has product life cycles that are measured in months.
In contrast, high performance/harsh environment electronics typically have product life cycles that are measured in decades and therefore are much more susceptible to the potential long term threat of tin whiskers. Industry studies have shown that pure tin surfaces can be “poisoned” with tin/lead solder provided the tin plating is consumed/converted during the soldering process. With many short components such as resistors or capacitors, the soldering process consistently and repeatedly eliminates any tin whisker risk. However, the component lead geometry, solder paste deposit and component pad dimensions all factor into whether a component can be successfully poisoned by the soldering process.
Connectors are typically not an issue, in terms of solder poisoning, as connector suppliers utilize the connector housing design/configuration to eliminate potential shorting from a tin whisker or ensure that the areas with pure tin surface finishes will be poisoned as part of the soldering process.
Previously, Rockwell Collins completed a connector technology qualification that included the Samtec SEARAY solder charge connector. The connector had very robust thermal cycle solder joint integrity and utilized a matte tin (i.e., pure tin) surface finish on the non-contact pin surfaces. During metallographic cross-sectioning phase of the connector’s qualification effort, it was observed that a region of matte tin was not poisoned during the soldering process nor was the tin whisker shorting potential in this region mitigated by the connector design/configuration. An investigation was conducted to determine if this region of the connector posed a tin whisker risk threat.
Editor's Note: This article originally appeared in the February issue of SMT Magazine.
Testimonial
"In a year when every marketing dollar mattered, I chose to keep I-Connect007 in our 2025 plan. Their commitment to high-quality, insightful content aligns with Koh Young’s values and helps readers navigate a changing industry. "
Brent Fischthal - Koh YoungSuggested Items
MacDermid Alpha Electronics Solutions Unveils Unified Global Website to Deepen Customer, Talent, and Stakeholder Engagement
07/31/2025 | MacDermid Alpha Electronics SolutionsMacDermid Alpha Electronics Solutions, the electronics business of Elements Solutions Inc, today launched macdermidalpha.com - a unified global website built to deepen digital engagement. The launch marks a significant milestone in the business’ ongoing commitment to delivering more meaningful, interactive, and impactful experiences for its customers, talent, and stakeholders worldwide.
KOKI to Showcase Analytical Services and New HF1200 Solder Paste at SMTA Guadalajara 2025
07/31/2025 | KOKIKOKI, a global leader in advanced soldering materials and process optimization services, will exhibit at the SMTA Guadalajara Expo & Tech Forum, taking place September 17 & 18, 2025 at Expo Guadalajara, Salón Jalisco Halls D & E in Guadalajara, Mexico.
Weller Tools Supports Future Talent with Exclusive Donation to SMTA Michigan Student Soldering Competition
07/23/2025 | Weller ToolsWeller Tools, the industry leader in hand soldering solutions, is proud to announce its support of the upcoming SMTA Michigan Expo & Tech Forum by donating a limited-edition 80th Anniversary Black Soldering Set to the event’s student soldering competition.
Koh Young Appoints Tom Hattori as President of Koh Young Japan
07/21/2025 | Koh YoungKoh Young Technology, the global leader in True 3D measurement-based inspection solutions, announced the appointment of Tom Hattori as President of Koh Young Japan (JKY).
Silicon Mountain Contract Services Enhances SMT Capabilities with New HELLER Reflow Oven
07/17/2025 | Silicon Mountain Contract ServicesSilicon Mountain Contract Services, a leading provider of custom electronics manufacturing solutions, is proud to announce a significant upgrade to its SMT production capability with the addition of a HELLER 2043 MK5 10‑zone reflow oven to its Nampa facility.