Banknote Check with Ultra-fast Line Scan Sensor
June 2, 2015 | Fraunhofer IBMTEstimated reading time: 3 minutes
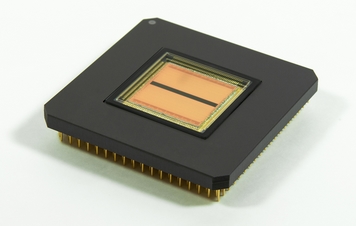
Speed and accurate image reproduction are the alpha and omega of quality inspection in security printing. Conventional image sensors are limited in this regard. Fraunhofer researchers have developed an ultrafast line scan sensor that delivers high-quality images and identifies banknotes with faulty safety features.
In the first half 2014 alone, nearly 25,000 counterfeit euro notes worth EUR 1.5 million were registered, according to information by the Deutsche Bundesbank. In order to make the criminal work of counterfeiters more difficult, banknotes are equipped with special security features. These include tiny structures that are not visible to the naked eye, such as holograms with a tilt effect. This results in the subject changing when it is looked at from different perspectives. Through the use of special cameras, quality checks during printing are intended to ensure that these features are free of errors on each banknote.
The AIT Austrian Institute of Technology is a leader in the international market in the production of such test systems for security printing. For the development of a new sensor, the Austrian research institution has brought the Fraunhofer Institute for Microelectronic Circuits and Systems IMS in Duisburg on board. This is because the sensors which are currently available have meanwhile reached their limits: their speed is often not enough to check quality in real-time during the production process.
Camera takes 200,000 color images per second
With the 60-line sensor that the Duisburg experts have developed, these drawbacks are now a thing of the past: “Our sensor is twice as fast as currently available solutions, while providing high-quality images in very high resolution,” explains Werner Brockherde from the IMS. The sensor detects the bills – like a scanner does – line by line when they come off the press. The camera takes up to 200,000 color images per second, with exposures of millionths of a second. Software compares the recorded images to a desired image and identifies banknotes with faulty safety features. In order to achieve the high speed, the IMS researchers have integrated an individual readout chain on the chip for each pixel column. In addition, they have developed special photo pixels, thanks to which conventional optics can be used, despite the short exposure times. In each pixel column, the three colors red, green and blue are recorded at the same time and over the entire pixel area. This allows high-quality color reproduction. Another special feature of the sensor is that the high number of lines makes it possible to detect objects from different perspectives. “As a result, surface structures in 3D, such as the tilt effects of holograms, can also be checked for the first time,” says Brockherde.
The special architecture of the sensor opens up room for further applications. Thanks to the large number of lines, its wavelength spectrum can still be expanded – up to the UV or infrared light range. That would be interesting for the recycling of plastics, as well, where the sensor could identify shredded materials according to their color information, thereby facilitating separation. With the ability to analyze 3D surfaces, it is also suitable for the quality control of different materials in industrial production.
Another field of application is the study of the rails or contact wires of trains: Even at a speed of around 300 km/h, the sensor could provide razor-sharp images with a resolution of up to 0.4 mm and, thus, detect the tiniest hairline cracks. Near-Earth satellites, which are equipped with such a sensor and which orbit the Earth at a speed of 26,000 kilometers per hour, could take color photographs of the earth’s surface with a resolution of 3 centimeters.
The market launch of the new sensor which is at the heart of the AIT test camera is scheduled for the end of 2015.
Suggested Items
Federal Electronics Adds AS9100 Certification to Hermosillo, Mexico Facility, Expanding Aerospace & Defense Capabilities
05/20/2025 | Federal ElectronicsFederal Electronics, a leader in providing advanced electronic manufacturing services, has officially added AS9100 certification to its Hermosillo, Mexico facility, further aligning its operations with the quality standards required by the aerospace and defense industries.
Creation Technologies Celebrates Ribbon Cutting of Expanded Denver Product Realization Center
05/19/2025 | Creation TechnologiesCreation Technologies, an end-to-end, scalable Specialty Global Electronic Manufacturing Services provider, proudly celebrated the official ribbon-cutting ceremony of its newly expanded Denver Product Realization Center on Monday, May 12, 2025.
K & F Electronics Invests in Workforce Training with IPC-A-610
05/15/2025 | K & F ElectronicsIn a strategic move to prioritize employee development and uphold quality standards, K & F Electronics, a third-generation, family-owned printed circuit board (PCB) manufacturer based in Fraser, Michigan, used a recent period of reduced production to certify its employees in IPC-A-610, the industry standard for the acceptability of electronic assemblies.
Canadian Circuits Inc. Unveils Rapid Prototype PCB Assembly Service to Accelerate Innovation
05/14/2025 | Canadian Circuits, Inc.Canadian Circuits Inc. (CCI), a leading provider of high-quality, made-in-Canada, Printed Circuit Board (PCB) solutions, is proud to announce the launch of its Prototype PCB Assembly (PCBA) service. This new offering enhances CCI’s commitment to empowering engineers and OEMs by accelerating the journey from concept to product launch with precision and efficiency in electronics manufacturing.
Breaking Down Barriers: The Connectivity of Machines in SMT Production Lines
05/14/2025 | Bill Cardoso, Creative ElectronAs the world increasingly moves toward erecting trade barriers, we find ourselves in a paradox. Across the globe, the rise in tariffs and protectionist policies is creating a more fragmented global economy, with nations seeking to insulate themselves from external economic pressures. However, within the confines of the SMT production line, the trend is moving in precisely the opposite direction—toward greater connectivity, integration, and collaboration. Rather than isolating one machine from another, SMT production lines are increasingly interconnected, with data being shared across various stages of the process to improve quality, efficiency, and defect detection.