Estimated reading time: 5 minutes
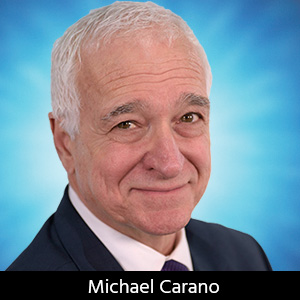
Contact Columnist Form
Trouble in Your Tank: Yield Improvement and Reliability
There’s a simple rule of business in manufacturing: “It is all about yields.”
Higher yields for your products allow for increased profits and satisfied customers. When there are lower yields, overall cost to manufacture increases, and the additional time and strain on the factory floor affect the entire operation. Lower yields are often the result of “process drift,” when critical process parameters and specialized plating additives fall outside their acceptable ranges. While this may still allow, for example, for a circuit board to pass the electrical test, process drift and out-of-specification parameters will invite reliability failures at some point when the electronic system is in service.
In my prior columns on technology, defect analysis, and prevention, I discussed not only the type of defects and their causes but also how to prevent them.
TGW (Things go Wrong)
Inevitably, things occasionally go wrong. That doesn’t mean yield loss and reliability failures are acceptable. There is always some fallout. However, use of certain tools (process audits, statistical process control, etc.), analytical controls, proper training (and constant re-training of personnel), and use of IPC test methods go a long way to enhance yields and long-term reliability.
Defining Quality
Quality can mean different things to different people—from customer satisfaction and meeting specifications to value. However, meeting requirements is no longer sufficient in today’s high-tech arena. We must always strive to improve beyond simply adhering to specifications or blueprints. Think of quality as meeting a target condition (see examples in the IPC-600 and IPC-610 acceptability documents). By tightening quality requirements, companies then concentrate on getting close to the target condition. In other words, minimize those situations where nonconformances arise and the product is defective. As is well-defined in IPC-600 and IPC-610, the target is the ideal condition.
Strategies to Improve Yields and Reliability
Here are four strategies that will benefit fabricators:
- Training and certification
- Statistical process control/FMEA
- Online real-time analysis/control of processes
- Test vehicles/thermal reliability methods
Training and Certification
Invest in training and certification through IPC. There are many programs available, including online training and certification programs through IPC Edge.
The first programs you should consider are:
- IPC-600
- IPC-610
- IPC-6012
- IPC-6013
- IPC-6015
In addition, consider IPC’s many certification and training programs. Become a Certified IPC Trainer (CIT) or a Certified IPC Specialist (CIS).
Statistical Process Control (SPC)
SPC is a critical tool that can be used to control and improve any process. Look at any process as a system that has inputs, outputs, and operating parameters. Operating conditions and parameters are variables that can change and affect the quality and reliability of the product. It’s important to monitor and control these process variables to meet the customer’s requirements. Using SPC will drive the ongoing optimization of these systems and processes.
SPC is particularly valuable in studying various manufacturing systems. As with any process, there is variability, which is to be expected. No two things are the same. The goal is to minimize this variability to consistently achieve the target condition and minimize the natural width of the process. You want to tighten the variation around the target condition. From there, it’s possible to calculate the Process Capability Index (Cpk). Understanding and measuring Cpk for all processes will allow for a high-quality manufacturing operation.
Online Realtime Analysis/Control of Processes
One cannot stress enough the importance of maintaining tight control of the manufacturing processes. This includes, but is not limited to:
- Plating solutions
- Rinse water cleanliness
- Proper operating temperatures
- pH control of processes
Relying on periodic wet analysis once or so per shift is not the answer to building a quality-focused organization. Although we automate some processes like etching and electroless copper, many processes still rely on simple wet analytical methods that lack comprehensive data for accuracy and consistency.
One very important method is to have tight controls on the electroplating processes. Invest in real-time analysis instruments, as shown in Figure 1.
This electroplating bath analyzer (EBA) is accurate and easy to implement. It provides precise control of electroplating solutions. The system from Technic, Inc. uses both AC and DC voltammetry in a chemometric approach (a chemical discipline that uses statistics, formal logic, and mathematics to extract critical information). This eliminates interferences from matrix effects that can skew analytical data and results.
With rinse water cleanliness, don’t underestimate the potential for cross-contamination on circuit boards that will lead to failures such as electromigration or simply less reliable plating and surface finishing. Insufficient rinsing after solderable finishes will lead to assembly failures, and the potential for field failures such as corrosion. A low-cost investment in conductivity probes will monitor the effectiveness of the rinsing and minimize excess water usage.
Finally, monitoring the pH of key processes such as resist development will minimize situations where incomplete development and/or resist residues remain within tight lines and spaces. The concern here is opens and shorts.
Test Vehicles/Thermal Reliability Methods
Designing test vehicles to mimic circuit board designs is necessary to ensure product reliability. Then employing one or more of the IPC test methods below provides further opportunity to improve processes.
IPC published a test method designed to screen blind vias after boards have been manufactured. The convection reflow simulation test method (IPC-TM-650 2.6.27B) exposes the PWB to the highest temperature extremes it will encounter during reflow assembly. Unlike other IPC test methods, IPC-TM-650 2.6.27B uses continuous resistance monitoring of daisy chains during convection reflow to detect failures in real time. The acceptance criterion is a less than 5% increase in resistance using the first cycle’s peak temperature resistance as the reference value.
Complement convection resistance testing with air-to-air thermal shock testing (IPC-TM-650 2.6.7.2C). Identical test coupons (IPC-2221B D coupon) and test systems are suitable for these methodologies. The 5% acceptance criterion remains, despite measuring resistance only once per cycle at the high-temperature extreme. The test conditions are limited by the material parameters (Tg minus 10°C) and the reflow temperature (25°C below peak).
Figure 2 (IPC-TM-650 2.6.27) shows the D-coupon setup used for reliability testing.
Quality is everyone’s business and job. Take no shortcuts.
This column originally appeared in the May 2025 issue of PCB007 Magazine.
More Columns from Trouble in Your Tank
Trouble in Your Tank: Minimizing Small-via Defects for High-reliability PCBsTrouble in Your Tank: Metallizing Flexible Circuit Materials—Mitigating Deposit Stress
Trouble in Your Tank: Can You Drill the Perfect Hole?
Trouble in Your Tank: Causes of Plating Voids, Pre-electroless Copper
Trouble in Your Tank: Organic Addition Agents in Electrolytic Copper Plating
Trouble in Your Tank: Interconnect Defect—The Three Degrees of Separation
Trouble in Your Tank: Things You Can Do for Better Wet Process Control
Trouble in Your Tank: Processes to Support IC Substrates and Advanced Packaging, Part 5