Stretchable Ceramics Made by Flame Technology
June 9, 2015 | Kiel UniversityEstimated reading time: 2 minutes
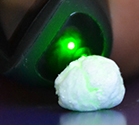
Synthesizing nanoscale materials takes place within high-tech laboratories, where scientists in full-body suits keep every grain of dust away from their sensitive innovations. However, scientists at Kiel University proved that this is not always necessary. They have successfully been able to transfer the experience from furnace to laboratory while synthesizing nanoscale materials using simple and highly efficient flame technology. This “baking” of nanostructures has already been a great success using zinc oxide. The recent findings concentrate on tin oxide, which opens up a wide field of possible new applications. The material scientists published their latest research data in today’s issue (Friday, 5 June) of the renowned scientific journal Advanced Electronic Materials.
Metal oxides in bulk form are generally brittle, which limits their desired utilizations. Their one-dimensional (1D) structures, such as belt-like nanostructures, exhibit much more application potential because of their high surface to volume ratio. This ratio induces extraordinary physical and chemical properties, including a high degree of bendability. “However, 1D nanostructures are still difficult to use, because integrating them in real devices is a challenging task. To overcome this issue, we have developed three-dimensional (3D) macroscopic material from 1D tin oxide belt-like nanostructures. The resulting ceramic networks exhibit most of the nanoscale properties, including flexibility. It can therefore be freely utilized for any desired application. We are very pleased that our recently introduced flame transport synthesis method on the basis of zinc oxide now enables the simple synthesis of interconnected 3D networks from tin oxide”, says Dr Yogendra Kumar Mishra, group leader of the working group “Functional Nanomaterials” at Kiel University, and main author of the study.
“The fascinating part is the structure of the single belt-like nanostructures delivered by this synthesis on the basis of tin oxide crystal structure. In contrast to ceramic produced with zinc oxide, which leads to very short tetrapod structures, tin oxide gives long, flat structures. They are just like fettucine”, compares Professor Rainer Adelung, Chairperson of the Functional Nanomaterials group. “And these long flat noodles grow together in a very specific way: In the oven used for the synthesis, temperatures stay just below the melting point of tin oxide. Thus, the noodles find specific interconnection points by kinetics instead of thermodynamics. Each junction is forced into a well-defined angle following strict geometric principles, which are based on so-called twinning defects, as further confirmed by simulation studies”, adds Professor Lorenz Kienle, Chairperson of the Synthesis and Real Structure group. The structural design of the tin oxide 3D network, meaning the grown-together noodles, was investigated in detail using transmission electron microscopy.
“The 3D networks from tin oxide exhibit interesting features, such as electrically conducting, high temperature stable, very soft and stretchable architecture, and could thus be interesting for several technological applications”, says Dr Mishra. For example, a portable electronic sensing device has already been fabricated. And, according to Mishra, it demonstrates significant potential for UV light or gas sensing applications. “Until now, we have tested sensing applications. Further potential applications could also be flexible and stretchable electronic devices, luminescent actuators, batteries, smart cloths or sacrificial templates for the growth of new materials.” This work has been performed in co-operation with Professor Ion Tiginyanu and his team members from the Technical University of Moldova, Moldova.
The three Kiel scientists know: “Development of such 3D network materials from tin oxide, with geometry determining defects made by flame transport synthesis at Kiel University is a very interesting step forward into the future of nanostructure growth and applications.”
Suggested Items
Bell to Build X-Plane for Phase 2 of DARPA Speed and Runway Independent Technologies (SPRINT) X-Plane Program
07/09/2025 | Bell Textron Inc.Bell Textron Inc., a Textron Inc. company, has been down-selected for Phase 2 of Defense Advanced Research Projects Agency (DARPA) Speed and Runway Independent Technologies (SPRINT) X-Plane program with the objective to complete design, construction, ground testing and certification of an X-plane demonstrator.
Nolan’s Notes: Moving Forward With Confidence
06/03/2025 | Nolan Johnson -- Column: Nolan's NotesWe’re currently enjoying a revitalized and dynamic EMS provider market with significant growth potential. Since December 2024, the book-to-bill has been extremely strong and growing. Starting with a ratio of 1.24 in December, book-to-bill has continued to accelerate to a 1.41 in April. Yet, there is a global economic restructuring taking place. To say that the back-and-forth with tariffs and trade deals makes for an uncertain market is an understatement. While we may be in a 90-day tariff pause among leading economic nations, the deadline is quickly approaching and that leaves many of you feeling unsettled about what to expect.
Mycronic High Flex Changes Division Name to PCB Assembly Solutions
05/20/2025 | MycronicMycronic AB, the leading Sweden-based electronics assembly solutions provider, announced that its division formerly known as High Flex will now operate under the name PCB Assembly Solutions.
SolderKing Achieves the Prestigious King’s Award for Enterprise in International Trade
05/06/2025 | SolderKingSolderKing Assembly Materials Ltd, a leading British manufacturer of high-performance soldering materials and consumables, has been honoured with a King’s Award for Enterprise, one of the UK’s most respected business honours.
Foxconn's Tiger Leap Combining Nature and Technology in Ecological Roof Garden
04/23/2025 | FoxconnHon Hai Technology Group, the world's largest technology manufacturing and service provider, has actively responded to the United Nations Sustainable Development Goals (SDGs).