-
- News
- Books
Featured Books
- smt007 Magazine
Latest Issues
Current IssueIntelligent Test and Inspection
Are you ready to explore the cutting-edge advancements shaping the electronics manufacturing industry? The May 2025 issue of SMT007 Magazine is packed with insights, innovations, and expert perspectives that you won’t want to miss.
Do You Have X-ray Vision?
Has X-ray’s time finally come in electronics manufacturing? Join us in this issue of SMT007 Magazine, where we answer this question and others to bring more efficiency to your bottom line.
IPC APEX EXPO 2025: A Preview
It’s that time again. If you’re going to Anaheim for IPC APEX EXPO 2025, we’ll see you there. In the meantime, consider this issue of SMT007 Magazine to be your golden ticket to planning the show.
- Articles
- Columns
Search Console
- Links
- Media kit
||| MENU - smt007 Magazine
A Review of the Opportunities and Processes for Printed Electronics (Part 5): The Future of PE
June 26, 2015 | Happy Holden, PCB Technologist-RetiredEstimated reading time: 11 minutes
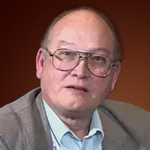
Flexible thin-film solar cells on plastic film have enormous potential. New applications will take advantage of their attributes of being lightweight and flexible. Applications include solar cells on T-shirts and jackets, modules on cars, boats and light aircraft, mobile and camping energy and novel toys like LED night kites. Since these materials can be tailored to shapes, architectural drapes and roof and wall coatings are all practical.
Figure 1: OE-A roadmaps give a best guess on how rapidly the PE market will develop.
Batteries/energy storage
An energy technology that is complementary and compatible with flexible solar cells is thin flexible batteries made in similar ways to CIGS thin-film PC devices. There are electrodes in the battery, but instead of generating electricity, electrolytes will store electricity. Zinc manganese dioxide (ZnMnO2) is a typical electrolyte, as is lithium-ion (Li-ion).
The novelty of these inexpensive batteries is that they can be eco-friendly, single-use and disposable without causing pollution, releasing any toxic compounds or combusting. They can be used in innovations such as cosmetic teeth whitening, anti-aging electric wrinkle care and moisturizing, electrophoresis hair removal, RFID, toys and even medicine delivery.
Thin flexible batteries can be made out of simple paper (as thin as 0.6mm) using a spacer that is made largely of cellulose and printed with carbon nanotubes with electrolytes that are soaked into the paper. The batteries are available in 1.5, 3, 4.5 and 6V at 4.5mAh/cm2 and weigh less than a gram. They can have a shelf life of three years and can operate at temperatures ranging from -20°C to 60°C. These green batteries are produced by screen printing, disposable and free of toxic chemicals. They cannot overheat, explode or cause burns and are non-toxic and non-flammable. Power Paper of Israel has perfected this technology. There are other companies producing thin flexible batteries.
The most exciting of these new developments is from Planar Energy, a spin-off of the US National Renewable Energy Center in Colorado. Their solid-state nanofilm electrolysis technology produces conductivity metrics equivalent to liquid electrolytes with three times the energy density of current Li-ion batteries and cost less than half the price per kilowatt hour. Their roll-to-roll deposition process is called SPEED (Streaming Protocol for Electroless Electrochemical Deposition). Thin-film nanomaterials are deposited sequentially on the flexible substrate, resulting in lower costs and increased control compared to vacuum deposition.
Low cost e-paper and other PE displays continue to be a major research focus. In addition to OLED technology on flex, there is also electrophoretic, electrochromic and electroluminescent displays. OLED displays are used in mobile phones. They use Universal Display's phosphorescent red, green and blue OLED materials, which have been proven to significantly reduce power consumption in numerous glass-based AMOLED products.
Figure 2: Displays.
The displays use an active matrix array of thin-film transistors fabricated on DuPont Teijin Films Teonex film using substrate handling and processing technologies developed at the Flexible Display Center (FDC) at Arizona State University. Versions using transistors made with both low-temperature amorphous silicon and higher performance indium gallium zinc oxide have been produced.
It was previously thought that amorphous silicon backplanes were unsuitable for OLED due to stability problems. However, Ignis Innovation has solved the stability problems, paving the way for this first product.
"The performance is equivalent to polysilicon AMOLED. The product also incorporates Ignis’s latest all-in-one driver chip for amorphous silicon AMOLED, which is the first of its kind in today's AMOLED market," says Paul Arsenault, president and CEO. "This opens the door for RiTdisplay and other manufacturers to make state-of-the-art AMOLED displays using existing amorphous silicon equipment that is currently being used for LCD. This is the start of a new era where AMOLED displays can be made in much greater volumes, and with lower cost, than they are today with polysilicon."
Ignis Innovation is the leading provider of technology that makes AMOLED displays last longer, look better and cost less. Ignis works with display manufacturers to improve AMOLED displays using innovative circuit designs, driving algorithms and embedded software.
RiTdisplay, established in 2000, is the first company in Taiwan devoted in OLED research and development and manufacturing. It is currently the only company capable of manufacturing both OLED and polymer light-emitting diode (PLED) products. By adopting a customer-oriented marketing strategy together with the most advanced technology capability, RiTdisplay offers the most advanced display products to meet the demand in a variety of applications.
The different OLED manufacturing process lends itself to several advantages over flat-panel displays made with LCD technology.
Lower cost in the future
OLEDs can be printed onto any suitable substrate by an inkjet printer or even by screen printing, theoretically making them cheaper to produce than LCD or plasma displays. However, fabrication of the OLED substrate is more costly than that of a TFT LCD, until mass production methods lower cost through scalability. Roll-to-roll vapor deposition methods for organic devices allow mass production of thousands of devices per minute for minimal cost. However, this technique can induce problems due to the challenges associated with manufacturing multilayer devices.
Page 1 of 3
Suggested Items
Incap Helps Develop Future Talent in Robotics and Engineering in Finland
05/21/2025 | IncapIncap Corporation continues to invest in the next generation of technology professionals in Finland through its involvement in two national initiatives focused on technical and vocational education.
Jabil, AVL Collaborate on Design and Manufacturing Solutions for Automotive and Transportation Customers
05/21/2025 | BUSINESS WIREJabil Inc., a global manufacturing solutions provider to market-leading automakers, announced it has signed a memorandum of understanding (MOU) with AVL Software and Functions GmbH, the e-drive and software center of AVL List GmbH.
Altus, Danutek Expand Partnership with LPKF to Offer Laser Plastic Welding Solutions
05/21/2025 | Altus GroupAltus Group, a leading supplier of capital equipment and service support for the electronics manufacturing sector in the UK and Ireland, and its sister company Danutek, which serves Central and Eastern Europe, are expanding their technology offering through an enhanced partnership with LPKF, a specialist in laser-based manufacturing solutions.
Deca Announces Agreement with IBM to Bring High-Density Fan-Out Interposer Production to North America
05/20/2025 | Deca TechnologiesDeca Technologies announced the signing of an agreement with IBM to implement Deca’s M-Series™ and Adaptive Patterning® technologies in IBM’s advanced packaging facility in Bromont, Quebec.
Global PCB Connections: Rigid-flex and Flexible PCBs—The Backbone of Modern Electronics
05/20/2025 | Jerome Larez -- Column: Global PCB ConnectionsIn the past decade, flex and rigid-flex PCB technology has become the fastest-growing market segment. As an increasing number of PCB companies develop the capabilities to fabricate this technology, PCB designers are becoming comfortable incorporating these designs into their products.