-
-
News
News Highlights
- Books
Featured Books
- pcb007 Magazine
Latest Issues
Current IssueSales: From Pitch to PO
From the first cold call to finally receiving that first purchase order, the July PCB007 Magazine breaks down some critical parts of the sales stack. To up your sales game, read on!
The Hole Truth: Via Integrity in an HDI World
From the drilled hole to registration across multiple sequential lamination cycles, to the quality of your copper plating, via reliability in an HDI world is becoming an ever-greater challenge. This month we look at “The Hole Truth,” from creating the “perfect” via to how you can assure via quality and reliability, the first time, every time.
In Pursuit of Perfection: Defect Reduction
For bare PCB board fabrication, defect reduction is a critical aspect of a company's bottom line profitability. In this issue, we examine how imaging, etching, and plating processes can provide information and insight into reducing defects and increasing yields.
- Articles
- Columns
- Links
- Media kit
||| MENU - pcb007 Magazine
Estimated reading time: 5 minutes
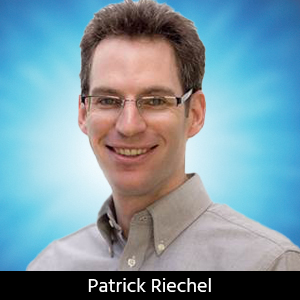
Keeping on Top of Laser Safety
With consumer electronics continuing to get thinner and packed with more functionality, laser processing systems have become a permanent part of the manufacturing landscape. Lasers are used to produce ever-smaller microvias in increasingly delicate flexible and rigid-flex circuits.
Compared to mechanical-based processing solutions, lasers offer advantages such as better control, greater flexibility and more precise manipulation of a wider range of materials. What’s more, laser systems are essentially the only game in town when the application requires hole sizes of less than 100 microns. Taking advantage of the benefits that laser processing has to offer, however, means that those in your plant will need to start paying close attention to safety guidelines related to working in proximity to laser systems.
But what laser safety considerations need to be taken into account and what are the implications? This column delivers two perspectives on the topic: one view from Mike Jennings, Director of Product Marketing for ESI’s Industrial Products Division, and one view from Patrick Riechel, ESI’s Product Manager for PCB. Mike provides the industry veteran, shop floor management perspective while Patrick provides a more contemporary technical perspective.
In this month’s column, Mike and Patrick weigh in on the use of lasers in micromachining (as they will going forward) and offer up insights on laser safety issues.
What is laser safety and why is it so important?
Patrick: Laser safety involves taking a holistic approach from the design of the laser processing system itself through to the implementation of safety practices that follow ANSI and IEC guidelines. When systems, policies and processes are properly designed and implemented, manufacturers can safely operate laser processing systems indefinitely without incident. That really is the goal of laser safety – to be completely safe at all times.
Mike: Sure, we need guidelines and they need to be followed, but we’re talking about human nature here. Where I see people running into problems is when they get complacent. They’ve worked with lasers every day for years and have never had a problem. Then one day, they decide to open a door intending to quickly clean the optics or to simply make an adjustment that will “only take a second,” having lost an appreciation for the risk. All it takes is fumbling for a dropped screwdriver, and their hand or finger could be crossing a high-power beam. Laser safety isn’t something that should be practiced some of the time – it needs to be all the time. It involves people, and safety needs to become a cultural norm.
ANSI guidelines call for manufacturers to have a Laser Safety Officer (LSO). How does an LSO contribute to a safer work environment?
Patrick: As a general rule of thumb, if your organization is using a Class 4 laser, you will need an LSO. All of the laser systems ESI makes use Class 4 lasers. If you are doing PCB manufacturing you are using Class 4 lasers and will need an LSO. The LSO is responsible for keeping up with the latest laser safety guidelines, developing safety procedures and for employee training.
Mike: Your LSO needs to keep safety top of mind for everyone in proximity to the lasers. Your LSO plays an important role in keeping you current with the latest technologies as well as changes to safety standards. Laser safety is something of a moving target as new lasers in different wavelengths and with greater power reach the market. Turnover can be an issue. If your LSO leaves the company, be sure to name another qualified one immediately. If you’re just getting into lasers, I’d recommend bringing in an outside consultant to conduct an audit of your laser safety program. They can also recommend or train a new LSO candidate.
What are some scenarios that represent the greatest risk?
Patrick: It easy to forget that there are non-beam hazards as well. For instance, industrial lasers require high electrical current to power laser excitation hardware. Another risk is fire caused by ignition of flammable materials from accidental exposure to the laser. It’s also important to be aware of collateral radiation, which can take the form of x-ray, ultraviolet, infrared, microwave and radio frequency emissions. Different lasers present different risks that your LSO can help determine and mitigate.
Mike: First of all, remember that these lasers are nothing like the laser in a laser pointer that you use to amuse your cat. The use of high-power, short pulse femtosecond and picosecond lasers in manufacturing increases the need for attention to safety. These lasers concentrate energy with such intensity and in such short durations that an injury can occur before it’s possible to react. That’s why it’s so important to avoid taking shortcuts. People have to develop a healthy respect for the power of these lasers. 100% attention to detail. You can’t have people neglecting their eye protection or overriding lockout mechanisms, even if it’s just to perform a “quick fix” or an “adjustment.”
Eyewear is a critical part of laser safety. What are some factors to keep in mind?
Patrick: Eyewear must be selected for the specific type of laser to block the appropriate wavelength range. All approved laser protective eyewear is rated for optical density, which is what reduces beam power to a safe level. The OD for a set of laser glasses is printed on a label and absolutely must exceed the minimum OD requirement for each laser used in your plant. Be aware too that picosecond lasers require a specific type of eyewear.
Mike: There’s a concept here that people need to understand. Unlike ordinary visible light, laser light is monochromatic, directional and coherent. Consequently, the amount of damage to the eye is independent to the distance the laser beam travels. Just because you can’t see it doesn’t mean you don’t need protection. Everyone within in line of sight of an active laser is at risk and should always be wearing appropriate eye protection, including room occupants.
ANSI recently released new laser safety guidelines. Can you walk us through some of the highlights?
Patrick: The US guidelines for laser safety are provided in the ANSI Z136 series of standards, which can be obtained from the Laser Institute of America. In 2013, the ANSI Z136.9 standard on the safe use of lasers in manufacturing was released. Most of the updates are intended to reflect the growing use of high-powered fiber and short-pulse duration lasers in manufacturing environments.
Mike: Just remember, best practices for laser safety are continually evolving. In order to stay current and to keep your people safe, it’s important that everyone have the latest safety standards on-hand and closely adhere to the guidelines at all times – especially when you think it might not be necessary.
More Columns from Laser Pointers
Laser Pointers: Stepping Up to Laser Processing for Flex, Part 6 — Proper Care and Feeding of Your EquipmentLaser Pointers: Stepping Up to Laser Processing for Flex, Part 5—Process Development
Laser Pointers: Stepping Up to Laser Processing for Flex, Part 4—Installation, Training and Initial Operation
Laser Processing and Telecentricity
Stepping up to Laser Processing for Flex, Part 3: Readiness and Site Preparation
Automate to Innovate in Flex Processing
Stepping Up to Laser Processing for Flex, Part 2: Calculating and Optimizing Production
Stepping Up To Laser Processing for Flex, Part 1: Opportunities and Implications