A Small, Modular, Efficient Fusion Plant
August 10, 2015 | MITEstimated reading time: 5 minutes
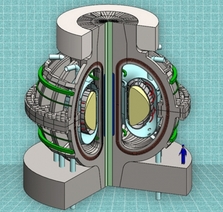
It’s an old joke that many fusion scientists have grown tired of hearing: Practical nuclear fusion power plants are just 30 years away — and always will be.
But now, finally, the joke may no longer be true: Advances in magnet technology have enabled researchers at MIT to propose a new design for a practical compact tokamak fusion reactor — and it’s one that might be realized in as little as a decade, they say. The era of practical fusion power, which could offer a nearly inexhaustible energy resource, may be coming near.
Using these new commercially available superconductors, rare-earth barium copper oxide (REBCO) superconducting tapes, to produce high-magnetic field coils “just ripples through the whole design,” says Dennis Whyte, a professor of Nuclear Science and Engineering and director of MIT’s Plasma Science and Fusion Center. “It changes the whole thing.”
The stronger magnetic field makes it possible to produce the required magnetic confinement of the superhot plasma — that is, the working material of a fusion reaction — but in a much smaller device than those previously envisioned. The reduction in size, in turn, makes the whole system less expensive and faster to build, and also allows for some ingenious new features in the power plant design. The proposed reactor, using a tokamak (donut-shaped) geometry that is widely studied, is described in a paper in the journal Fusion Engineering and Design, co-authored by Whyte, PhD candidate Brandon Sorbom, and 11 others at MIT. The paper started as a design class taught by Whyte and became a student-led project after the class ended.
Power plant prototype
The new reactor is designed for basic research on fusion and also as a potential prototype power plant that could produce significant power. The basic reactor concept and its associated elements are based on well-tested and proven principles developed over decades of research at MIT and around the world, the team says.
“The much higher magnetic field,” Sorbom says, “allows you to achieve much higher performance.”
Fusion, the nuclear reaction that powers the sun, involves fusing pairs of hydrogen atoms together to form helium, accompanied by enormous releases of energy. The hard part has been confining the superhot plasma — a form of electrically charged gas — while heating it to temperatures hotter than the cores of stars. This is where the magnetic fields are so important—they effectively trap the heat and particles in the hot center of the device.
While most characteristics of a system tend to vary in proportion to changes in dimensions, the effect of changes in the magnetic field on fusion reactions is much more extreme: The achievable fusion power increases according to the fourth power of the increase in the magnetic field. Thus, doubling the field would produce a 16-fold increase in the fusion power. “Any increase in the magnetic field gives you a huge win,” Sorbom says.
Tenfold boost in power
While the new superconductors do not produce quite a doubling of the field strength, they are strong enough to increase fusion power by about a factor of 10 compared to standard superconducting technology, Sorbom says. This dramatic improvement leads to a cascade of potential improvements in reactor design.
The world’s most powerful planned fusion reactor, a huge device called ITER that is under construction in France, is expected to cost around $40 billion. Sorbom and the MIT team estimate that the new design, about half the diameter of ITER (which was designed before the new superconductors became available), would produce about the same power at a fraction of the cost and in a shorter construction time.
But despite the difference in size and magnetic field strength, the proposed reactor, called ARC, is based on “exactly the same physics” as ITER, Whyte says. “We’re not extrapolating to some brand-new regime,” he adds.
Another key advance in the new design is a method for removing the the fusion power core from the donut-shaped reactor without having to dismantle the entire device. That makes it especially well-suited for research aimed at further improving the system by using different materials or designs to fine-tune the performance.
In addition, as with ITER, the new superconducting magnets would enable the reactor to operate in a sustained way, producing a steady power output, unlike today’s experimental reactors that can only operate for a few seconds at a time without overheating of copper coils.
Liquid protection
Another key advantage is that most of the solid blanket materials used to surround the fusion chamber in such reactors are replaced by a liquid material that can easily be circulated and replaced, eliminating the need for costly replacement procedures as the materials degrade over time.
“It’s an extremely harsh environment for [solid] materials,” Whyte says, so replacing those materials with a liquid could be a major advantage.
Right now, as designed, the reactor should be capable of producing about three times as much electricity as is needed to keep it running, but the design could probably be improved to increase that proportion to about five or six times, Sorbom says. So far, no fusion reactor has produced as much energy as it consumes, so this kind of net energy production would be a major breakthrough in fusion technology, the team says.
The design could produce a reactor that would provide electricity to about 100,000 people, they say. Devices of a similar complexity and size have been built within about five years, they say.
“Fusion energy is certain to be the most important source of electricity on earth in the 22nd century, but we need it much sooner than that to avoid catastrophic global warming,” says David Kingham, CEO of Tokamak Energy Ltd. in the UK, who was not connected with this research. “This paper shows a good way to make quicker progress,” he says.
The MIT research, Kingham says, “shows that going to higher magnetic fields, an MIT speciality, can lead to much smaller (and hence cheaper and quicker-to-build) devices.” The work is of “exceptional quality,” he says; “the next step … would be to refine the design and work out more of the engineering details, but already the work should be catching the attention of policy makers, philanthropists and private investors.”
The research was supported by the U.S. Department of Energy and the National Science Foundation.
Suggested Items
Elephantech: For a Greener Tomorrow
04/16/2025 | Marcy LaRont, PCB007 MagazineNobuhiko Okamoto is the global sales and marketing manager for Elephantech Inc., a Japanese startup with a vision to make electronics more sustainable. The company is developing a metal inkjet technology that can print directly on the substrate and then give it a copper thickness by plating. In this interview, he discusses this novel technology's environmental advantages, as well as its potential benefits for the PCB manufacturing and semiconductor packaging segments.
Trouble in Your Tank: Organic Addition Agents in Electrolytic Copper Plating
04/15/2025 | Michael Carano -- Column: Trouble in Your TankThere are numerous factors at play in the science of electroplating or, as most often called, electrolytic plating. One critical element is the use of organic addition agents and their role in copper plating. The function and use of these chemical compounds will be explored in more detail.
IDTechEx Highlights Recyclable Materials for PCBs
04/10/2025 | IDTechExConventional printed circuit board (PCB) manufacturing is wasteful, harmful to the environment and energy intensive. This can be mitigated by the implementation of new recyclable materials and technologies, which have the potential to revolutionize electronics manufacturing.
Connect the Dots: Stop Killing Your Yield—The Hidden Cost of Design Oversights
04/03/2025 | Matt Stevenson -- Column: Connect the DotsI’ve been in this industry long enough to recognize red flags in PCB designs. When designers send over PCBs that look great on the computer screen but have hidden flaws, it can lead to manufacturing problems. I have seen this happen too often: manufacturing delays, yield losses, and designers asking, “Why didn’t anyone tell me sooner?” Here’s the thing: Minor design improvements can greatly impact manufacturing yield, and design oversights can lead to expensive bottlenecks. Here’s how to find the hidden flaws in a design and avoid disaster.
Real Time with... IPC APEX EXPO 2025: Tariffs and Supply Chains in U.S. Electronics Manufacturing
04/01/2025 | Real Time with...IPC APEX EXPOChris Mitchell, VP of Global Government Relations for IPC, discusses IPC's concerns about tariffs on copper and their impact on U.S. electronics manufacturing. He emphasizes the complexity of supply chains and the need for policymakers to understand their effects.