-
-
News
News Highlights
- Books
Featured Books
- smt007 Magazine
Latest Issues
Current IssueIntelligent Test and Inspection
Are you ready to explore the cutting-edge advancements shaping the electronics manufacturing industry? The May 2025 issue of SMT007 Magazine is packed with insights, innovations, and expert perspectives that you won’t want to miss.
Do You Have X-ray Vision?
Has X-ray’s time finally come in electronics manufacturing? Join us in this issue of SMT007 Magazine, where we answer this question and others to bring more efficiency to your bottom line.
IPC APEX EXPO 2025: A Preview
It’s that time again. If you’re going to Anaheim for IPC APEX EXPO 2025, we’ll see you there. In the meantime, consider this issue of SMT007 Magazine to be your golden ticket to planning the show.
- Articles
- Columns
Search Console
- Links
- Media kit
||| MENU - smt007 Magazine
No Time for a Board Spin? Selective Solder Mask Removal
January 6, 2016 | Bob Wettermann, BEST Inc.Estimated reading time: 2 minutes
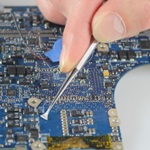
What do you do when you need solder mask removed quickly? What do you do when you get the boards back from the shop and there’s a missing pad, or your design team did not catch the design error in the pad or trace area, resulting in mask where it’s not supposed to be? Perhaps the test group tells you the RF shields need to have the trace opened up in order to pass the testing, but there are literally thousands of boards in the supply chain needing this modification. In these cases solder mask needs to be removed—usually in a hurry—in order to fix these problems.
Outside of re-spinning the board and starting over, there are several processes that can selectively remove solder mask in a controlled and consistent fashion. Some are better controlled than others and include mechanical abrasion, chemical etching, and micro and laser ablation.
Several factors will help determine the method to use including the type of solder mask, and where the area of interest is located. Other factors are the quantity of PCBs, the amount of solder mask needing removal and whether the circuit boards are bare boards or are populated with components.
Grinding and Scraping
One of the most straightforward methods of mask removal is via scraping or grinding of the soldermask. Since solder mask is only a little more than 1mil in thickness it does not require a large mechanical force to scrape it off. With either the use of a knife, scraper, pick or eraser, thin layers of mask can be removed by a skilled and certified repair technician. A multitude of equipment rework stations containing drills, grinders, rotating brushes, and the like are commercially available that the rework technician can use.
There are several drawbacks to this process, namely operator fatigue on large projects, and the lack of repeatability when ultra fine dimensional requirements need to be adhered to. Even with steady hands and fabricated masks the tolerances that can be held by skilled personnel is to ±10 mils. In addition, the depth control using this technique is very poor and underlying laminate or copper layers may be damaged as there is a lack of depth control. The positive aspects of this method are that no special set-up is required and it can be done by almost anyone for prototype or low-volume rework.
Another method that can control the depth of the cut is through the use of a milling machine to remove the solder mask. It is a more precise technique for removing solder mask than using a manually-controlled depth cut of a hand grinding tool. Since high-speed cutters are used when milling, precision depth control is essential since the cutters will tend to pull into the coating and may penetrate into the board surface.
Not damaging the underlying laminate is the key risk in using this approach. Turning the milling cutter in the opposite direction can be an effective technique for controlling the depth. Operator skill and experience as well as board fixturing are paramount to making this technique work.
Editor's Note: This article originally appeared in the December 2015 issue of SMT Magazine.
Suggested Items
KYZEN to Focus on Aqueous Cleaning and Stencil Cleaning at SMTA Juarez
05/20/2025 | KYZEN'KYZEN, the global leader in innovative environmentally responsible cleaning chemistries, will exhibit at the SMTA Juarez Expo and Tech Forum, scheduled to take place Thursday, June 5 at the Injectronics Convention Center in Ciudad Jarez, Chihuahua.
Koh Young Installs 24,000th Inspection System at Top 20 EMS
05/14/2025 | Koh YoungKoh Young, the global leader in True 3D measurement-based inspection and metrology solutions, proudly announces the installation of its 24,000th inspection system at a Top 20 Global EMS in Thailand.
Indium’s Karthik Vijay to Present on Dual Alloy Solder Paste Systems at SMTA’s Electronics in Harsh Environments Conference
05/06/2025 | Indium CorporationIndium Corporation Technical Manager, Europe, Africa, and the Middle East Karthik Vijay will deliver a technical presentation on dual alloy solder paste systems at SMTA’s Electronics in Harsh Environments Conference, May 20-22 in Amsterdam, Netherlands.
SolderKing Achieves the Prestigious King’s Award for Enterprise in International Trade
05/06/2025 | SolderKingSolderKing Assembly Materials Ltd, a leading British manufacturer of high-performance soldering materials and consumables, has been honoured with a King’s Award for Enterprise, one of the UK’s most respected business honours.
Knocking Down the Bone Pile: Gold Mitigation for Class 2 Electronics
05/07/2025 | Nash Bell -- Column: Knocking Down the Bone PileIn electronic assemblies, the integrity of connections between components is paramount for ensuring reliability and performance. Gold embrittlement and dissolution are two critical phenomena that can compromise this integrity. Gold embrittlement occurs when gold diffuses into solder joints or alloys, resulting in mechanical brittleness and an increased susceptibility to cracking. Conversely, gold dissolution involves the melting away of gold into solder or metal matrices, potentially altering the electrical and mechanical properties of the joint.