Happy’s Essential Skills: The Need for Total Quality Control (Six Sigma and Statistical Tools): Part 1
January 13, 2016 | Happy HoldenEstimated reading time: 11 minutes
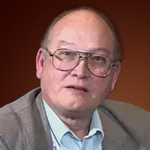
In this first of many columns covering my "Twenty-Five Essential Skills Every Engineer Needs to Learn," I will expand on each of those skills. To read the introduction to this series, which published in the January issue of The PCB Magazine, click here. As a quick recap, here are the 25 skills that I will be writing about over the next 18 months or so, to publish every three weeks or so in the PCB007 Daily Newsletter (if you are not yet a subscriber, click here to have the newsletter delivered to your inbox for free):
1. TQC/six sigma/statistics/curve fitting
2. Problem solving
3. Design of experiments
4. FMEA
5. Information research on the Internet
6. Technical writing
7. Product/process life cycles
8. Learning curve/learning theory
9. Figure of merit/shared vision
10. Design for manufacturing/assembly
11. Managing management time
12. Project/program management
13. Benchmarking
14. Engineering economics/ROI/BET
15. Roadmapping
16. Quality functional deployment (House of Quality)
17. Automation strategy/CIM
18. Computer aided manufacturing
19. Recruiting and interviewing
20. METRICS—dimensional analysis
21. 10-Step business plan
22. Programmed instruction/long distance learning
23. Lean manufacturing/JIT/TOC
24. Technology awareness
25. Predictive engineering
Let's get started. The first topic is one of the most important: Total Quality Control (including six sigma, and statistical tools).
Total Quality Control (TQC)
Total Quality Control is the philosophy of continuous process improvement through statistical techniques and a commitment to excellence. TQC are systems for optimizing production based on ideas developed by Japanese industries since the 1950s. This term has evolved into Total Quality Management (TQM) and Six Sigma (6σ). The system, which blends Western and Eastern ideas, began with the concept of quality circles, in which groups of 10–20 workers were given responsibility for the quality of the products they produced. It gradually evolved into various techniques involving both workers and managers to maximize productivity and quality, including close monitoring of staff and excellent customer service.
The concept of kaizen—the notion that improvement must involve all members of a company—is central to TQC. It aims to radically transform the organization through progressive changes in the attitudes, practices, structures, and systems.
Figure 1: Key links between quality, productivity and customer satisfaction.
Total quality control transcends the product quality approach, involves everyone in the organization, and encompasses its every function: administration, communications, distribution, manufacturing, marketing, planning, and training.
TQC views an organization as a collection of processes. It maintains that organizations must strive to improve continuously these processes by incorporating the knowledge and experiences of workers. The simple objective of TQC is "Do the right things, right the first time, every time." True improvements in quality of products and services have multiple positive effects on an organization, as shown in Figure 1: lower costs, lower prices, and increased customer satisfaction. Although originally applied to manufacturing operations, and for a number of years only used in that area, TQC is now becoming recognized as a generic management tool, just as applicable in service and public sector organizations. There are a number of evolutionary offshoots, like Six-Sigma, with different sectors creating their own versions from the common ancestor. TQC is the foundation for activities that include:
• Commitment to leadership by senior management and empowerment of all employees, from the top down
• Meeting of customer requirements
• Reduction of development cycle times
• Just in Time/demand flow manufacturing
• Improvement teams
• Reduction of product and service costs
• Systems to facilitate improvement
• Line management ownership
• Employee involvement and empowerment
• Recognition and celebration
• Challenging quantified goals and benchmarking
• Focus on processes/improvement plans
• Specific incorporation in strategic planning
This shows that TQC must be practiced in all activities, by all personnel, in manufacturing, marketing, engineering, R&D, sales, purchasing, and HR, etc.[1].
Page 1 of 4
Testimonial
"Our marketing partnership with I-Connect007 is already delivering. Just a day after our press release went live, we received a direct inquiry about our updated products!"
Rachael Temple - AlltematedSuggested Items
The Art and Science of PCB Floor Planning: A Comprehensive Guide
08/14/2025 | Cory Grunwald and Jeff Reinhold, Monsoon SolutionsPCB design is an intricate and crucial part of developing electronic products. One of the foundational stages of PCB design is floor planning, a phase where the placement of components and the flow of signals are meticulously mapped out. A good floor plan ensures that the PCB performs well, is easy to manufacture, and meets all mechanical and electrical requirements. We’ll explore the essential aspects of floor planning, from its objectives and process to the challenges that designers face.
Advint and SanRex Expand High-Performance DC Rectifier Access for North American PCB Fabricators
08/12/2025 | Advint IncorporatedAdvint Incorporated has entered a strategic partnership with SanRex Corporation, enhancing access to industrial-grade DC rectifiers for the US printed circuit board industry. With a legacy of power innovation and performance across the globe, SanRex rectifiers are available through Advint’s proficient distribution network.
Advint and Sayron Bring Advanced Rectifier Solutions to High-Reliability PCB Manufacturers
08/01/2025 | Advint IncorporatedAdvint Incorporated has partnered with Sayron, a leading global rectifier manufacturer, to supply cutting-edge IGBT-based DC rectifiers to high-performance PCB manufacturers across North America and beyond. Sayron’s precision-engineered rectifiers align with the stringent requirements of advanced PCB processes.
Trouble in Your Tank: Metallizing Flexible Circuit Materials—Mitigating Deposit Stress
08/04/2025 | Michael Carano -- Column: Trouble in Your TankMetallizing materials, such as polyimide used for flexible circuitry and high-reliability multilayer printed wiring boards, provide a significant challenge for process engineers. Conventional electroless copper systems often require pre-treatments with hazardous chemicals or have a small process window to achieve uniform coverage without blistering. It all boils down to enhancing the adhesion of the thin film of electroless copper to these smooth surfaces.
Magnalytix’s Dr. Mike Bixenman to Guide PDC at SMTA High-Reliability Cleaning and Conformal Coating Conference
07/31/2025 | MAGNALYTIXMagnalytix, providing real-time reliability solutions for electronics manufacturing, is excited to announce that Dr. Mike Bixenman will present the professional development course “The Effects of Flux Residues and Process Contamination on the Reliability of the Electronic Assembly” on Wednesday, Aug. 13 at 9:00 AM CST to open the second day of the STMA High-Reliability Cleaning and Conformal Coating Conference.