-
- News
- Books
Featured Books
- pcb007 Magazine
Latest Issues
Current IssueInventing the Future with SEL
Two years after launching its state-of-the-art PCB facility, SEL shares lessons in vision, execution, and innovation, plus insights from industry icons and technology leaders shaping the future of PCB fabrication.
Sales: From Pitch to PO
From the first cold call to finally receiving that first purchase order, the July PCB007 Magazine breaks down some critical parts of the sales stack. To up your sales game, read on!
The Hole Truth: Via Integrity in an HDI World
From the drilled hole to registration across multiple sequential lamination cycles, to the quality of your copper plating, via reliability in an HDI world is becoming an ever-greater challenge. This month we look at “The Hole Truth,” from creating the “perfect” via to how you can assure via quality and reliability, the first time, every time.
- Articles
- Columns
- Links
- Media kit
||| MENU - pcb007 Magazine
Estimated reading time: 11 minutes
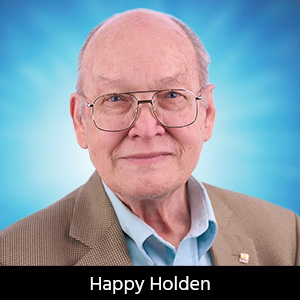
Contact Columnist Form
The Need for Total Quality Control (Six Sigma and Statistical Tools), Part 1
In this first of many columns covering my "Twenty-Five Essential Skills Every Engineer Needs to Learn," I will expand on each of those skills. To read the introduction to this series, which published in the January issue of The PCB Magazine, click here. As a quick recap, here are the 25 skills that I will be writing about over the next 18 months or so, to publish every three weeks or so in the I-Connect007 Daily Newsletter (if you are not yet a subscriber, click here to have the newsletter delivered to your inbox for free):
1. TQC/six sigma/statistics/curve fitting
2. Problem solving
3. Design of experiments
4. FMEA
5. Information research on the Internet
6. Technical writing
7. Product/process life cycles
8. Learning curve/learning theory
9. Figure of merit/shared vision
10. Design for manufacturing/assembly
11. Managing management time
12. Project/program management
13. Benchmarking
14. Engineering economics/ROI/BET
15. Roadmapping
16. Quality functional deployment (House of Quality)
17. Automation strategy/CIM
18. Computer aided manufacturing
19. Recruiting and interviewing
20. METRICS—dimensional analysis
21. 10-Step business plan
22. Programmed instruction/long distance learning
23. Lean manufacturing/JIT/TOC
24. Technology awareness
25. Predictive engineering
Let's get started. The first topic is one of the most important: Total Quality Control (including six sigma, and statistical tools).
Total Quality Control (TQC)
Total Quality Control is the philosophy of continuous process improvement through statistical techniques and a commitment to excellence. TQC are systems for optimizing production based on ideas developed by Japanese industries since the 1950s. This term has evolved into Total Quality Management (TQM) and Six Sigma (6σ). The system, which blends Western and Eastern ideas, began with the concept of quality circles, in which groups of 10–20 workers were given responsibility for the quality of the products they produced. It gradually evolved into various techniques involving both workers and managers to maximize productivity and quality, including close monitoring of staff and excellent customer service.
The concept of kaizen—the notion that improvement must involve all members of a company—is central to TQC. It aims to radically transform the organization through progressive changes in the attitudes, practices, structures, and systems.
Figure 1: Key links between quality, productivity and customer satisfaction.
Total quality control transcends the product quality approach, involves everyone in the organization, and encompasses its every function: administration, communications, distribution, manufacturing, marketing, planning, and training.
TQC views an organization as a collection of processes. It maintains that organizations must strive to improve continuously these processes by incorporating the knowledge and experiences of workers. The simple objective of TQC is "Do the right things, right the first time, every time." True improvements in quality of products and services have multiple positive effects on an organization, as shown in Figure 1: lower costs, lower prices, and increased customer satisfaction. Although originally applied to manufacturing operations, and for a number of years only used in that area, TQC is now becoming recognized as a generic management tool, just as applicable in service and public sector organizations. There are a number of evolutionary offshoots, like Six-Sigma, with different sectors creating their own versions from the common ancestor. TQC is the foundation for activities that include:
• Commitment to leadership by senior management and empowerment of all employees, from the top down
• Meeting of customer requirements
• Reduction of development cycle times
• Just in Time/demand flow manufacturing
• Improvement teams
• Reduction of product and service costs
• Systems to facilitate improvement
• Line management ownership
• Employee involvement and empowerment
• Recognition and celebration
• Challenging quantified goals and benchmarking
• Focus on processes/improvement plans
• Specific incorporation in strategic planning
This shows that TQC must be practiced in all activities, by all personnel, in manufacturing, marketing, engineering, R&D, sales, purchasing, and HR, etc.[1].
Principles of TQC
The key principles[2] of TQC are:
1. Management Commitment
Top management has to drive any system as large or as complex as TQC. Until management makes that commitment, a bottoms-up approach of sending engineers or workers to SPC or quality classes will not take root. My experience with this started when our group VP introduced TQC to his staff. He gave each of them a personal project and then had each of them train their staff after which they gave out individual projects. This 4 Episodes of TQC was labeled LUTI for Learn, Use, Teach, Individualize, and so forth, down through the structure until it got to the individual supervisor and worker.
2. Process Improvement
The TQC Improvement Circle or PDCA steps are used in a continuous manner to assess the current situation, propose and implement solutions, test effectiveness of the solution, and standardize the process on those solutions that are found effective (Figure 2). Data is used to prioritize the improvements on which to work.
• Plan (drive, direct)
• Do (deploy, support, participate)
• Check (review)
• Act (recognize, communicate, revise)
Figure 2: TQC Improvement Circle consisting of plan-do-check-act.
3. Employee Empowerment
• Training
• Suggestion scheme
• Measurement and recognition
• Excellence teams
4. Fact-Based Decision Making
• SPC (statistical process control)
• DOE, FMEA
• The 6 statistical tools
• TOPS (Ford 8D—team-oriented problem solving)
Continuous Improvement
• Systematic measurement and focus on CONQ
• Excellence teams
• Cross-functional process management
• Attain, maintain, improve standards
Customer Focus
• Supplier partnership
• Service relationship with internal customers
• Never compromise quality
• Customer-driven standards
The Concept of Continuous Improvement by TQC
TQC is mainly concerned with continuous improvement in all work, from high-level strategic planning and decision-making, to detailed execution of work on the shop floor. It stems from the belief that mistakes can be avoided and defects can be prevented. It leads to continuously improving results, in all aspects of work, because of continuously improving capabilities, people, processes, technology and machine capabilities.
Continuous improvement must deal not only with improving results, but more importantly with improving capabilities to produce better results in the future. The five major areas of focus for capability improvement are demand generation, supply generation, technology, operations and people capability.
Figure 3: TQC central principles and what it is NOT.
A central principle of TQC (voiced by Dr. Deming) is that people may make mistakes, but most of them are caused, or at least permitted, by faulty systems and processes. This means that the root cause of such mistakes can be identified and eliminated, and repetition can be prevented by changing the process[3]. There are three major mechanisms of prevention:
1. Preventing mistakes (defects) from occurring (mistake-proofing or poka-yoke).
2. Where mistakes cannot be absolutely prevented, detecting them early to prevent them from being passed down the value-added chain (inspection at source or by the next operation).
3. Where mistakes recur, stopping production until the process can be corrected, to prevent the production of more defects (stop in time).
Implementation Principles and Processes
A preliminary step in TQC implementation is to assess the organization's current reality. Relevant preconditions have to do with the organization's history, its current needs, precipitating events leading to TQC, and the existing employee quality of working life. If the current reality does not include important preconditions, TQC implementation should be delayed until the organization is in a state in which TQC is likely to succeed. Fundamental is that TQC has to be "driven from the top" and includes those principles shown in Figure 3. When Dr. Deming would come to a company to lecture, he insisted the front row consisted of the company president and executives, otherwise, he said, "It is not worth my time!"
If an organization has a track record of effective responsiveness to the environment, and if it has been able to change successfully the way it operates when needed, TQC will be easier to implement. If an organization has been historically reactive and has no skill at improving its operating systems, there will be both employee skepticism and a lack of skilled change agents. If this condition prevails, a comprehensive program of management and leadership development may be instituted. A management audit is a good assessment tool to identify current levels of organizational functioning and areas in need of change. An organization should be healthy before beginning TQC. If it has significant problems such as a very unstable funding base, weak administrative systems, lack of managerial skill, or poor employee morale, TQC would not be appropriate[4].
However, a certain level of stress is probably desirable to initiate TQC. People need to feel a need for a change. Kanter (1983) addresses this phenomenon by describing building blocks, which are present in effective organizational change. These forces include departures from tradition, a crisis or galvanizing event, strategic decisions, individual "prime movers," and action vehicles. Departures from tradition are activities, usually at lower levels of the organization, which occur when entrepreneurs move outside the normal ways of operating to solve a problem. A crisis, if it is not too disabling, can also help create a sense of urgency, which can mobilize people to act. In the case of TQC, this may be a funding cut or threat, or demands from consumers or other stakeholders for improved quality of service. After a crisis, a leader may intervene strategically by articulating a new vision of the future to help the organization deal with it. A plan to implement TQC may be such a strategic decision. Such a leader may then become a prime mover, who takes charge in championing the new idea and showing others how it will help them get where they want to go. Finally, action vehicles are needed and mechanisms or structures to enable the change to occur and become institutionalized[5].
TQC Tools
Data collection and analysis tools are required to document and improve the process. Here are a few (as well as Figure 4), but this is not the complete list (other topics will be addressed in future columns):
• Pareto charts
• Cause & effect diagrams (Fishbone)
• Multi-vary charts (histograms, dot diagrams, correlation/scatter plots)
• Design of experiment
• Process optimization
• Control charts
• Process capability indices (Cp, Cpk)
• PPM
Figure 4: TQC data collection and analysis tools: process flow charts, fishbone 'cause and effect' charts, histograms, Pareto charts, correlation and scatter plots, and control charts.
Steps in Managing the Transition
Beckhard and Pritchard (1992) have outlined the basic steps in managing a transition to a new system such as TQC: identifying tasks to be done, creating necessary management structures, developing strategies for building commitment, designing mechanisms to communicate the change, and assigning resources.
Task identification would include a study of present conditions (assessing current reality, as described above); assessing readiness, such as through a force field analysis; creating a model of the desired state, in this case, implementation of TQC; announcing the change goals to the organization; and assigning responsibilities and resources. This final step would include securing outside consultation and training, and assigning someone within the organization to oversee the effort. This should be a responsibility of top management. In fact, the next step—designing transition management structures—is also a responsibility of top management. In fact, Cohen and Brand (1993) and Hyde (1992) assert that management must be heavily involved as leaders rather than relying on a separate staff person or function to shepherd the effort. An organization-wide steering committee to oversee the effort may be appropriate. Developing commitment strategies was discussed above in the sections on resistance and on visionary leadership[6].
To communicate the change, mechanisms beyond existing processes will need to be developed. Special, all-staff meetings attended by executives, sometimes designed as input or dialogue sessions, may be used to kick off the process, and TQC newsletters may be an effective ongoing communication tool to keep employees aware of activities and accomplishments.
Management of resources for the change effort is important with TQC because outside consultants will usually be required. Choose consultants based on their prior relevant experience and their commitment to adapting the process to fit unique organizational needs. While consultants will be invaluable with initial training of staff and TQC system design, employees (management and others) should be actively involved in TQC implementation, perhaps after receiving training in change management which they can then pass on to other employees. A collaborative relationship with consultants and clear role definitions and specification of activities must be established.
Summary
In summary, first assess preconditions and the current state of the organization to make sure the need for change is clear and that TQC is an appropriate strategy. Leadership styles and organizational culture must be congruent with TQC. If they are not, this should be worked on or TQC implementation should be avoided or delayed until favorable conditions exist.
Remember that this will be a difficult, comprehensive, and long-term process. Leaders will need to maintain their commitment, keep the process visible, provide necessary support, and hold people accountable for results. Use input from stakeholders (clients, referring agencies, funding sources, etc.) as much as possible; and, of course, maximize employee involvement in design of the system[7].
Always keep in mind that TQC should be purpose-driven. Be clear on the organization's vision for the future and stay focused on it. TQC can be a powerful technique for unleashing employee creativity and potential, reducing bureaucracy and costs, and improving service to clients and the community.
TQC encourages participation amongst shop floor workers and managers. There is no single theoretical formalization of total quality, but Deming, Juran and Ishikawa provide the core assumptions, as a "...discipline and philosophy of management which institutionalizes planned and continuous... improvement ... and assumes that quality is the outcome of all activities that take place within an organization; that all functions and all employees have to participate in the improvement process; that organizations need both quality systems and a quality culture."
CLICK HERE TO DOWNLOAD FIGURES PDF
Footnotes and References
1. Hyde, A. (1992). "The Proverbs of Total Quality Management: Recharting the Path to Quality Improvement in the Public Sector." Public Productivity and Management Review, 16(1), 25-37.
2. Martin, L. (1993). "Total Quality Management in the Public Sector," National Productivity Review, 10, 195-213.
3. Gilbert, G. (1992). "Quality Improvement in a Defense Organization." Public Productivity and Management Review, 16(1), 65-75.
4. Tichey, N. (1983). Managing Strategic Change. New York: John Wiley & Sons.
5. Swiss, J. (1992). "Adapting TQC to Government." Public Administration Review, 52, 356-362.
6. Smith, AK. (1993). "Total Quality Management in the Public Sector." Quality Progress, June 1993, 45-48.
7. Hill, Stephen. (1991). "Why Quality Circles Failed but Total Quality Management Might Succeed." British Journal of Industrial Relations, 29(4), 541-568.
Happy Holden has worked in printed circuit technology since 1970 with Hewlett-Packard, NanYa/Westwood, Merix, Foxconn and Gentex. Currently, he is the co-editor, with Clyde Coombs, of the Printed Circuit Handbook, 7th Ed. To contact Holden, click here.
More Columns from Happy’s Tech Talk
Happy’s Tech Talk #42: Applying Density Equations to UHDI DesignHappy’s Tech Talk #41: Sustainability and Circularity for Electronics Manufacturing
Happy’s Tech Talk #40: Factors in PTH Reliability—Hole Voids
Happy’s Tech Talk #39: PCBs Replace Motor Windings
Happy’s Tech Talk #38: Novel Metallization for UHDI
Happy’s Tech Talk #37: New Ultra HDI Materials
Happy’s Tech Talk #36: The LEGO Principle of Optical Assembly
Happy’s Tech Talk #35: Yields March to Design Rules