-
-
News
News Highlights
- Books
Featured Books
- pcb007 Magazine
Latest Issues
Current IssueThe Hole Truth: Via Integrity in an HDI World
From the drilled hole to registration across multiple sequential lamination cycles, to the quality of your copper plating, via reliability in an HDI world is becoming an ever-greater challenge. This month we look at “The Hole Truth,” from creating the “perfect” via to how you can assure via quality and reliability, the first time, every time.
In Pursuit of Perfection: Defect Reduction
For bare PCB board fabrication, defect reduction is a critical aspect of a company's bottom line profitability. In this issue, we examine how imaging, etching, and plating processes can provide information and insight into reducing defects and increasing yields.
Voices of the Industry
We take the pulse of the PCB industry by sharing insights from leading fabricators and suppliers in this month's issue. We've gathered their thoughts on the new U.S. administration, spending, the war in Ukraine, and their most pressing needs. It’s an eye-opening and enlightening look behind the curtain.
- Articles
- Columns
- Links
- Media kit
||| MENU - pcb007 Magazine
New CEO Jeff Waters Outlines his Roadmap for Isola
February 8, 2016 | Barry Matties, I-Connect007Estimated reading time: 26 minutes
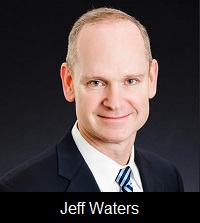
Jeff Waters, Isola’s newly appointed CEO and president, comes to the laminate supplier after more than 25 years in the semiconductor industry, working for companies like Texas Instruments and National Semiconductor. Only a few days into his new job, I met with Jeff to discuss the transition and what we can expect from Isola under his leadership.
Barry Matties: Jeff, you are now the president and CEO of Isola. How does that feel?
Jeff Waters: It feels great. It’s very exciting.
Matties: Just for a little context, why don't you start by sharing a little bit of your background for our readers.
Waters: I started my career working for National Semiconductor in a wafer fab as a process engineer and did that for about four or five years. Then I went over to Japan with a research fellowship with Fujitsu Laboratories and did some semiconductor research there before coming back to go to business school in Chicago. I worked in management consulting for a few years, and then went back to National. This was in the early to mid-'90s, and since then I’ve spent the rest of my time working in semiconductors.
Looking back on it, one of the nice things about working for a company like National Semiconductor or Texas Instruments is that I was exposed to a lot of different kinds of businesses that were in various stages of success and failure—some that were more in their infancy to those that were more mature.
I was running the sales organization in Japan for National, so my family and I were over in Japan for about four years. While we were there, it was announced that Texas Instruments was going to be buying National. I ended up coming back to California with TI and was there for about five months before I left to go to Altera, a semiconductor company in the programmable logic space. About a year ago, Intel announced their intention to acquire Altera and that concluded at the end of December of last year. Very soon thereafter, I made the move to come to Isola as president and CEO.
Matties: What was the appeal about Isola?
Waters: I saw a lot of things that were very exciting and very appealing. The first is that there is a lot of carry-over from my experience in semiconductors into what Isola does. If you look at the end-customers, the OEMs, and even the markets that we serve, they are identical. The communications customers, the automotive customers, even as you go into the data center and other areas—it’s a lot of that same end-market and a lot of the same trends and dynamics that are driving what results in demand for Isola materials.
From a technology perspective, certainly laminates are different from semiconductors, but it's interesting when you look at the way a printed circuit board is put together. It's very similar to the way a semiconductor is put together, but obviously on more of a macro scale than what you have in semiconductors. And even on the material science part of it as well. When I was at National Semiconductor, I spent the majority of my time working in the analog part of the business. Analog is less about massive circuits that are very highly miniaturized and much more about material science and properties of materials that you use to create very interesting operational amplifiers or data converters or signal conditioning chips. I think even from a materials science side of it, there's a comfort level that I have as I look at where Isola is.
Certainly coming out of the semiconductor industry for me is a refreshing change, but it's not something completely foreign. We use a lot of copper in semiconductors and we use a lot of copper here in laminates. There was certainly the industry piece of it that I found compelling.
I think Isola as a company was probably what intrigued me the most, though. It's a company that has a very rich history, as I'm sure you know. It's over a hundred years old. It's seen a lot of twists and turns throughout the years. I think the position and the level of respect that it has out in the customer base was very appealing to me. When you look at the footprint that Isola has, I see that as a great asset that can be leveraged. We've got factories in China, Taiwan, Singapore, North America, and Europe. When you think about the way demand for laminates comes together, there's the OEM side of it and certainly having a manufacturing facility where the OEMs are is a huge advantage. For example, we have a facility in Germany where we have both R&D and manufacturing. When you think about the automotive market, a lot of the innovation comes from Germany and we have a plant with an R&D team that is right there in that backyard.
When you think about the data center and all that's going on in the U.S., we have a plant and R&D engineers on the West Coast sitting right where the market leaders are. Even when you head over to China, where you have also a lot of emergence happening in communications, automotive and other markets, we have plants and R&D people there as well. From an OEM perspective, we're well situated, and from a manufacturing perspective, we're well situated in that we have plants where the PCB fabricators are. For those that put a very high value on quick turnaround and the ability to get what they need very quickly, we have very agile plants that are situated where you'd want them to be. That's something that is very different from the competitor base that we have. I think that's something that we've leveraged, and it's something we can leverage even more as we evolve the company. I saw that as a great asset.
Page 1 of 6
Suggested Items
The Evolution of Picosecond Laser Drilling
06/19/2025 | Marcy LaRont, PCB007 MagazineIs it hard to imagine a single laser pulse reduced not only from nanoseconds to picoseconds in its pulse duration, but even to femtoseconds? Well, buckle up because it seems we are there. In this interview, Dr. Stefan Rung, technical director of laser machines at Schmoll Maschinen GmbH, traces the technology trajectory of the laser drill from the CO2 laser to cutting-edge picosecond and hybrid laser drilling systems, highlighting the benefits and limitations of each method, and demonstrating how laser innovations are shaping the future of PCB fabrication.
Day 2: More Cutting-edge Insights at the EIPC Summer Conference
06/18/2025 | Pete Starkey, I-Connect007The European Institute for the PCB Community (EIPC) summer conference took place this year in Edinburgh, Scotland, June 3-4. This is the third of three articles on the conference. The other two cover Day 1’s sessions and the opening keynote speech. Below is a recap of the second day’s sessions.
Day 1: Cutting Edge Insights at the EIPC Summer Conference
06/17/2025 | Pete Starkey, I-Connect007The European Institute for the PCB Community (EIPC) Summer Conference took place this year in Edinburgh, Scotland, June 3-4. This is the second of three articles on the conference. The other two cover the keynote speeches and Day 2 of the technical conference. Below is a recap of the first day’s sessions.
Preventing Surface Prep Defects and Ensuring Reliability
06/10/2025 | Marcy LaRont, PCB007 MagazineIn printed circuit board (PCB) fabrication, surface preparation is a critical process that ensures strong adhesion, reliable plating, and long-term product performance. Without proper surface treatment, manufacturers may encounter defects such as delamination, poor solder mask adhesion, and plating failures. This article examines key surface preparation techniques, common defects resulting from improper processes, and real-world case studies that illustrate best practices.
RF PCB Design Tips and Tricks
05/08/2025 | Cherie Litson, EPTAC MIT CID/CID+There are many great books, videos, and information online about designing PCBs for RF circuits. A few of my favorite RF sources are Hans Rosenberg, Stephen Chavez, and Rick Hartley, but there are many more. These PCB design engineers have a very good perspective on what it takes to take an RF design from schematic concept to PCB layout.