Building a Better Mousetrap, From the Atoms Up
March 7, 2016 | University of ConnecticutEstimated reading time: 6 minutes
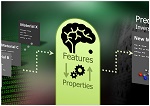
For most of human history, the discovery of new materials has been a crapshoot. But now, UConn researchers have systematized the search with machine learning that can scan millions of theoretical compounds for qualities that would make better solar cells, fibers, and computer chips. The search for new materials may never be the same.
No one knows why an early metallurgist decided to smelt a hunk of tin into some copper, but the resulting bronze alloy was harder and more durable than any material previously known. Most materials experimentation over the ensuing 7,000 years has been similarly random, guided largely by philosophy and chemical intuition.
But in a world that contains at least 95 stable elements – the basic building blocks of matter – the number of possible combinations is enormous, and experimentation is an awfully inefficient way to find what you’re looking for.
Enter UConn materials scientist Ramamurthy ‘Rampi’ Ramprasad. Instead of randomly mixing chemicals to see what they do, Ramprasad designs them rationally, using machine learning to figure out which atomic configurations make a polymer a good electrical conductor or insulator.
A polymer is a large molecule made of many repeating building blocks. Polymers are very common in both living and man-made materials. Probably the most familiar example is plastics, and the wide variation in plastics – which can be hard, soft, stretchy, brittle, spongy, clear, opaque or translucent – gives an inkling of how diverse polymers in general can be.
Polymers can also have diverse electronic properties. For example, they can be very good insulators – preventing electrons, and thus electric current, from traveling through them – or good conductors, allowing electricity to pass through them freely. And what controls all these properties is mainly how the atoms in the polymer connect to each other. But until recently, no one had systematically related properties to atomic configurations.
So Ramprasad and his colleagues decided to do just that. First, they would analyze known polymers, using laborious but accurate quantum mechanics-based calculations to figure out which arrangements of atoms confer which properties, and quantify those atomic-level relationships via a string of numbers that fingerprint each polymer. Once they had those, they could have a computer search through any number of theoretical polymers to figure out which ones might have which properties. Then anyone looking for a polymer with a certain property could quickly scan the list and decide which theoretical polymers might be worth trying.
Many polymers are made of building blocks containing just a few atoms. They look like this:
Yikrazuul – own work, public domain)" height="220" width="499">Polyurea, a common plastic. In this diagram, N is nitrogen, H hydrogen, and O oxygen. R stands in for any number of chemicals that could slightly alter the polymer, but the repeating NH-O-NH-O is the basic structure. Most polymers look like that, made of carbon (C), H, N and O, with a few other elements thrown in occasionally. (By Yikrazuul – own work, public domain)
For their project, Ramprasad’s group looked at polymers made of just seven building blocks: CH2, C6H4, CO, O, NH, CS, and C4H2S. These are found in common plastics such as polyethylene, polyesters, and polyureas. An enormous variety of polymers could theoretically be constructed using just these building blocks; Ramprasad’s group decided at first to analyze just 283, each composed of a repeated four-block unit.
They started from basic quantum mechanics, and calculated the three-dimensional atomic and electronic structures of each of those 283 four-block polymers. This is not trivial: calculating the position of every electron and atom in a molecule with more than two atoms takes a powerful computer a significant chunk of time, which is why they did it for only 283 molecules.
Once they had the three-dimensional structures, they could calculate what they really wanted to know: each polymer’s properties. They calculated the band gap, which is the amount of energy it takes for an electron in the polymer to break free of its home atom and travel around the material, and the dielectric constant, which is a measure of the effect an electric field can have on the polymer. These properties translate to how much electric energy each polymer can store in itself. The researchers used established techniques that have long been known. They take a prohibitive amount of computing time, which is why it’s so hard to evaluate materials this way.
Ramprasad’s group then went one step further. They wanted a shorthand system that a computer could use to look at the building blocks of a polymer and how they connect to each other, and make educated guesses about its properties.
Computers deal with numbers, so first they had to define each polymer as a string of numbers, a sort of numerical fingerprint. Since there are seven possible building blocks, there are seven possible numbers, each indicating how many of each block type are contained in that polymer. But a simple number string like that doesn’t give enough information about the polymer’s structure, so they added a second string of numbers that tell how many pairs there are of each combination of building blocks, such as NH-O or C6H4-CS. Still not quite enough information, so they added a third string that described how many triples, like NH-O-CH2, there were. They arranged these strings as a three-dimensional matrix, which is a convenient way to describe such strings of numbers in a computer.
Then they let the computer go to work. Using the library of 283 polymers they had laboriously calculated using quantum mechanics, the machine compared each polymer’s numerical fingerprint to its band gap and dielectric constant, and gradually ‘learned’ which building block combinations were associated with which properties. It could even map those properties onto a two-dimensional matrix of the polymer building blocks.
Page 1 of 2
Suggested Items
The Evolution of Picosecond Laser Drilling
06/19/2025 | Marcy LaRont, PCB007 MagazineIs it hard to imagine a single laser pulse reduced not only from nanoseconds to picoseconds in its pulse duration, but even to femtoseconds? Well, buckle up because it seems we are there. In this interview, Dr. Stefan Rung, technical director of laser machines at Schmoll Maschinen GmbH, traces the technology trajectory of the laser drill from the CO2 laser to cutting-edge picosecond and hybrid laser drilling systems, highlighting the benefits and limitations of each method, and demonstrating how laser innovations are shaping the future of PCB fabrication.
Day 2: More Cutting-edge Insights at the EIPC Summer Conference
06/18/2025 | Pete Starkey, I-Connect007The European Institute for the PCB Community (EIPC) summer conference took place this year in Edinburgh, Scotland, June 3-4. This is the third of three articles on the conference. The other two cover Day 1’s sessions and the opening keynote speech. Below is a recap of the second day’s sessions.
Day 1: Cutting Edge Insights at the EIPC Summer Conference
06/17/2025 | Pete Starkey, I-Connect007The European Institute for the PCB Community (EIPC) Summer Conference took place this year in Edinburgh, Scotland, June 3-4. This is the second of three articles on the conference. The other two cover the keynote speeches and Day 2 of the technical conference. Below is a recap of the first day’s sessions.
Preventing Surface Prep Defects and Ensuring Reliability
06/10/2025 | Marcy LaRont, PCB007 MagazineIn printed circuit board (PCB) fabrication, surface preparation is a critical process that ensures strong adhesion, reliable plating, and long-term product performance. Without proper surface treatment, manufacturers may encounter defects such as delamination, poor solder mask adhesion, and plating failures. This article examines key surface preparation techniques, common defects resulting from improper processes, and real-world case studies that illustrate best practices.
RF PCB Design Tips and Tricks
05/08/2025 | Cherie Litson, EPTAC MIT CID/CID+There are many great books, videos, and information online about designing PCBs for RF circuits. A few of my favorite RF sources are Hans Rosenberg, Stephen Chavez, and Rick Hartley, but there are many more. These PCB design engineers have a very good perspective on what it takes to take an RF design from schematic concept to PCB layout.