PhiChem Open House a Success!
March 28, 2016 | Pete Starkey, I-Connect007Estimated reading time: 5 minutes
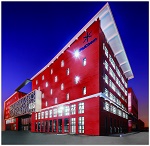
Delighted to be invited to an exclusive preview of the new PhiChem global headquarters and R&D centre in Shanghai’s Baoshan suburb, I joined the VIP group assembled at the PhiChem booth at the CPCA show, made welcome by PhiChem President Dr. Jin Zhang.
An hour’s private bus ride brought us to an immaculately presented site—four brand-new buildings with a total of 500,000 square feet of floor area: administration, pilot plant manufacturing and packaging, warehousing, fronted by a spectacularly impressive six-story laboratory complex, which had taken five years from green-field site to completion.
Gleaming! Through reception and into a display area with glass showcases holding examples of PhiChem’s products and applications, and an appropriate place for Dr. Zhang to begin his explanation of PhiChem’s evolution since he founded the company in 2002.
A graduate chemist, with an MS degree in optics, and many years’ experience in microelectronics packaging and the development of optical and laser materials and components, Jin Zhang gained his doctorate in polymer chemistry at the University of Michigan in the U.S. Recognising the rapid growth in the demand for optical fibres for data and telecoms transmission, and a fundamental requirement for glass fibres to be coated for mechanical protection and enhancement of their optical properties, Dr. Zhang returned to China and began production of UV-curable coating resins in Shanghai. Since 2002, PhiChem has grown to become China’s largest supplier of UV-curable materials to the optical fibre industry and second largest in the world, producing all of its own raw materials and resin precursors.
Dr. Zhang reached into a display cabinet and took a short length of fibre from a large spool, explaining that the widespread use of high bandwidth optical fibre would not have been feasible without the protection afforded by UV-curable coatings. The sample he demonstrated had a coated diameter of 250 microns, the glass itself being half that diameter, and the combination of glass and coating had a tensile strength of five kilograms. Talking of high speed, he remarked that the fibre was coated and cured on-the-fly at 3000 metres per minute!
Page 1 of 3
Testimonial
"Advertising in PCB007 Magazine has been a great way to showcase our bare board testers to the right audience. The I-Connect007 team makes the process smooth and professional. We’re proud to be featured in such a trusted publication."
Klaus Koziol - atgSuggested Items
MacDermid Alpha Electronics Solutions Unveils Unified Global Website to Deepen Customer, Talent, and Stakeholder Engagement
07/31/2025 | MacDermid Alpha Electronics SolutionsMacDermid Alpha Electronics Solutions, the electronics business of Elements Solutions Inc, today launched macdermidalpha.com - a unified global website built to deepen digital engagement. The launch marks a significant milestone in the business’ ongoing commitment to delivering more meaningful, interactive, and impactful experiences for its customers, talent, and stakeholders worldwide.
KOKI to Showcase Analytical Services and New HF1200 Solder Paste at SMTA Guadalajara 2025
07/31/2025 | KOKIKOKI, a global leader in advanced soldering materials and process optimization services, will exhibit at the SMTA Guadalajara Expo & Tech Forum, taking place September 17 & 18, 2025 at Expo Guadalajara, Salón Jalisco Halls D & E in Guadalajara, Mexico.
Weller Tools Supports Future Talent with Exclusive Donation to SMTA Michigan Student Soldering Competition
07/23/2025 | Weller ToolsWeller Tools, the industry leader in hand soldering solutions, is proud to announce its support of the upcoming SMTA Michigan Expo & Tech Forum by donating a limited-edition 80th Anniversary Black Soldering Set to the event’s student soldering competition.
Koh Young Appoints Tom Hattori as President of Koh Young Japan
07/21/2025 | Koh YoungKoh Young Technology, the global leader in True 3D measurement-based inspection solutions, announced the appointment of Tom Hattori as President of Koh Young Japan (JKY).
Silicon Mountain Contract Services Enhances SMT Capabilities with New HELLER Reflow Oven
07/17/2025 | Silicon Mountain Contract ServicesSilicon Mountain Contract Services, a leading provider of custom electronics manufacturing solutions, is proud to announce a significant upgrade to its SMT production capability with the addition of a HELLER 2043 MK5 10‑zone reflow oven to its Nampa facility.