Photochemical Metallization Allows the Manufacture of Touchscreens in a Single Step
April 13, 2016 | INMEstimated reading time: 3 minutes
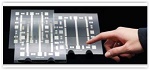
Leibniz Institute for New Materials are presenting a new process that, in a single step, allows manufacture of conductive paths that are just a few micrometers in width on flexible foils. As a result, new designs for appliances with flexible or even rollable displays will be possible.
In order for touchscreens on smartphones and tablets to function, microscopically fine conductor paths are required on their surfaces. When the users' fingers tip on or wipe over them, electrical circuits open and close, thus making the different functions of the smartphone possible. At the edges of the appliances, these microscopic circuit paths come together to form larger conductive paths. Until now, these different conductive paths had to be manufactured in several steps in time-consuming processes. The research scientists at INM – Leibniz-Institute for New Materials are now presenting a new process that, in a single step, allows manufacture of conductive paths that are just a few micrometers in width on carrier materials such as glass but also on flexible foils. On plastic foil, in particular, manufacture using the roll-to-roll process thus becomes particularly efficient. As a result, new designs for appliances with flexible or even rollable displays will be possible.
The researchers will be presenting their results from 25 to 29 April 2016 in Hall 2 at the stand B46 of the Hannover Messe in the context of the leading trade fair for R&D and Technology Transfer.
For the new process, the developers use a process known as photochemical metallization: When a photoactive layer is irradiated by UV light, colorless silver compounds are transformed into electrically conductive metallic silver. Several methods can be applied to transfer the silver compound in paths or other structures on plastic foil or glass. In this way, paths of varying sizes down to the smallest size of a thousandth of a millimeter can be achieved. By irradiating these with UV light, corresponding conductive paths are created.
“First, the foils are coated with a photoactive layer of metal oxide nanoparticles,” Peter William de Oliveira, Head of Optical Materials explained. “After that we apply the colorless, UV-stable silver compound.” By irradiation of this sequence of layers, the silver compound disintegrates on the photoactive layer and the silver ions are reduced to form metallic, electrically conductive silver. Oliviera added that this process offered several benefits: Since it is fast, flexible, variable in size, inexpensive and environmentally friendly, further process steps for post-treatment became unnecessary.
This basic principle allows conductive paths to be created very individually. “There are three different possibilities we can use depending on the requirements: `Writing conductive paths` using UV lasers is the process which is particularly suitable for the initial customized prototype manufacture and testing the new design of the conductive path. However, for mass production, this method is too time-consuming,” the physicist de Oliveira explained.
Photomasks that are only permeable for UV light at the desired positions can also be used for structuring. “For a `semi-continuous process` they are particularly suitable for applying the conductive paths on glass,” the materials expert says.
The researchers are currently working intensely on a third method, the usage of transparent stamps. “These stamps push out the silver compound mechanically; conductive paths then only occur where there is still silver compound,” de Oliveira stated. Since the stamps are made of a soft plastic, they can be arranged on a roll. Because they are transparent, researchers at INM are now working on embedding the UV source directly in the roll. “Thus, the initial steps for a roll-to-roll process would already have been taken,” the Head of Optical Materials group concluded. It would therefore be possible to manufacture conductive path structures of various sizes on foils on a large scale.
Suggested Items
The Pulse Design: Constraints for the Next Generation
07/16/2025 | Martyn Gaudion -- Column: The PulseIn Europe, where engineering careers were once seen as unpopular and lacking street credibility, we have been witnessing a turnaround in the past few years. The industry is now welcoming a new cohort of designers and engineers as people are showing a newfound interest in the profession.
Copper Price Surge Raises Alarms for Electronics
07/15/2025 | Global Electronics Association Advocacy and Government Relations TeamThe copper market is experiencing major turbulence in the wake of U.S. President Donald Trump’s announcement of a 50% tariff on imported copper effective Aug. 1. Recent news reports, including from the New York Times, sent U.S. copper futures soaring to record highs, climbing nearly 13% in a single day as manufacturers braced for supply shocks and surging costs.
Symposium Review: Qnity, DuPont, and Insulectro Forge Ahead with Advanced Materials
07/02/2025 | Barb Hockaday, I-Connect007In a dynamic and informative Innovation Symposium hosted live and on Zoom on June 25, 2025, representatives from Qnity (formerly DuPont Electronics), DuPont, and Insulectro discussed the evolving landscape of flexible circuit materials. From strategic corporate changes to cutting-edge polymer films, the session offered deep insight into design challenges, reliability, and next-gen solutions shaping the electronics industry.
Indium Corporation Expert to Present on Automotive and Industrial Solder Bonding Solutions at Global Electronics Association Workshop
06/26/2025 | IndiumIndium Corporation Principal Engineer, Advanced Materials, Andy Mackie, Ph.D., MSc, will deliver a technical presentation on innovative solder bonding solutions for automotive and industrial applications at the Global Electronics A
Gorilla Circuits Elevates PCB Precision with Schmoll’s Optiflex II Alignment System
06/23/2025 | Schmoll MaschinenGorilla Circuits, a leading PCB manufacturer based in Silicon Valley, has enhanced its production capabilities with the addition of Schmoll Maschinen’s Optiflex II Post-Etch Punch system—bringing a new level of precision to multilayer board fabrication.