Under Pressure: New Technique Could Make Large, Flexible Solar Panels More Feasible
May 17, 2016 | Pennsylvania State UniversityEstimated reading time: 1 minute
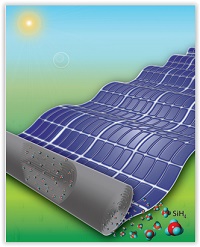
A new, high-pressure technique may allow the production of huge sheets of thin-film silicon semiconductors at low temperatures in simple reactors at a fraction of the size and cost of current technology. A paper describing the research by scientists at Penn State University publishes on May 13, 2016, in the journal Advanced Materials.
"We have developed a new, high-pressure, plasma-free approach to creating large-area, thin-film semiconductors," said John Badding, professor of chemistry, physics, and materials science and engineering at Penn State and the leader of the research team. "By putting the process under high pressure, our new technique could make it less expensive and easier to create the large, flexible semiconductors that are used in flat-panel monitors and solar cells and are the second most commercially important semiconductors."
Thin-film silicon semiconductors typically are made by the process of chemical vapor deposition, in which silane -- a gas composed of silicon and hydrogen -- undergoes a chemical reaction to deposit the silicon and hydrogen atoms in a thin layer to coat a surface. To create a functioning semiconductor, the chemical reaction that deposits the silicon onto the surface must happen at a low enough temperature so that the hydrogen atoms are incorporated into the coating rather than being driven off like steam from boiling water. With current technology, this low temperature is achieved by creating plasma -- a state of matter similar to a gas made up of ions and free electrons -- in a large volume of gas at low pressure. Massive and expensive reactors so large that they are difficult to ship by air are needed to generate the plasma and to accommodate the large volume of gas required.
"With our new high-pressure chemistry technique, we can create low-temperature reactions in much smaller spaces and with a much smaller volume of gas," said Badding. "The reduced space necessary allows us, for the first time, to create semiconductors on multiple, stacked surfaces simultaneously, rather than on just a single surface. To maximize the surface area, rolled-up flexible surfaces can be used in a very simple and far more compact reactor. The area of the resulting rolled-up semiconducting material could, upon further development, approach or even exceed a square kilometer."
Suggested Items
Knocking Down the Bone Pile: Addressing End-of-life Component Solderability Issues, Part 4
07/16/2025 | Nash Bell -- Column: Knocking Down the Bone PileIn 1983, the Department of Defense identified that over 40% of military electronic system failures in the field were electrical, with approximately 50% attributed to poor solder connections. Investigations revealed that plated finishes, typically nickel or tin, were porous and non-intermetallic.
STMicroelectronics, Metalenz Sign a New License Agreement to Accelerate Metasurface Optics Adoption
07/14/2025 | STMicroelectronicsSTMicroelectronics, a global semiconductor leader serving customers across the spectrum of electronics applications and Metalenz, the pioneer of metasurface optics, announced a new license agreement.
Digital Twin Concept in Copper Electroplating Process Performance
07/11/2025 | Aga Franczak, Robrecht Belis, Elsyca N.V.PCB manufacturing involves transforming a design into a physical board while meeting specific requirements. Understanding these design specifications is crucial, as they directly impact the PCB's fabrication process, performance, and yield rate. One key design specification is copper thieving—the addition of “dummy” pads across the surface that are plated along with the features designed on the outer layers. The purpose of the process is to provide a uniform distribution of copper across the outer layers to make the plating current density and plating in the holes more uniform.
Global PCB Connections: Embedded Components—The Future of High-performance PCB Design
06/19/2025 | Jerome Larez -- Column: Global PCB ConnectionsA promising advancement in this space is the integration of embedded components directly within the PCB substrate. Embedded components—such as resistors, capacitors, and even semiconductors—can be placed within the internal layers of the PCB rather than mounted on the surface. This enables designers to maximize available real estate and improve performance, reliability, and manufacturability.
Preventing Surface Prep Defects and Ensuring Reliability
06/10/2025 | Marcy LaRont, PCB007 MagazineIn printed circuit board (PCB) fabrication, surface preparation is a critical process that ensures strong adhesion, reliable plating, and long-term product performance. Without proper surface treatment, manufacturers may encounter defects such as delamination, poor solder mask adhesion, and plating failures. This article examines key surface preparation techniques, common defects resulting from improper processes, and real-world case studies that illustrate best practices.