-
- News
- Books
Featured Books
- smt007 Magazine
Latest Issues
Current IssueSupply Chain Strategies
A successful brand is built on strong customer relationships—anchored by a well-orchestrated supply chain at its core. This month, we look at how managing your supply chain directly influences customer perception.
What's Your Sweet Spot?
Are you in a niche that’s growing or shrinking? Is it time to reassess and refocus? We spotlight companies thriving by redefining or reinforcing their niche. What are their insights?
Moving Forward With Confidence
In this issue, we focus on sales and quoting, workforce training, new IPC leadership in the U.S. and Canada, the effects of tariffs, CFX standards, and much more—all designed to provide perspective as you move through the cloud bank of today's shifting economic market.
- Articles
- Columns
- Links
- Media kit
||| MENU - smt007 Magazine
New Solar Absorber Could Improve Efficiency of Solar Thermal Technology
June 15, 2016 | MITEstimated reading time: 3 minutes
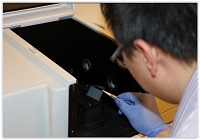
A team of researchers at MIT and the Masdar Institute of Science and Technology has discovered a low-cost way to significantly increase the amount of solar energy that can be converted into heat, via a device called a solar absorber. This advance should help make sustainable technologies that rely on solar heat more efficient and affordable.
“Our research team has developed a simple and cost-effective fabrication technique to create solar absorbers that can harness a greater share of the solar spectrum, thus increasing their efficiencies, while also maintaining low emission levels,” says TieJun Zhang, assistant professor of mechanical and materials engineering at the Masdar Institute, a graduate-level engineering university in the United Arab Emirates.
Zhang co-authored the paper that describes this research, which was published this month in the journal Advanced Optical Materials. The work contributes to a larger Masdar Institute-MIT research project, which is aimed at developing a solar-powered combined electrical power plant and cooling system.
The MIT and Masdar Institute Cooperative Program helped launch the Masdar Institute in 2007. Research collaborations between the two institutes address global energy and sustainability issues, and seek to develop research and development capabilities in Abu Dhabi.
Nicholas X. Fang, professor of mechanical engineering at MIT and co-principal investigator of the project, said: “We are very excited that this MIT-Masdar Institute collaboration has led to new insights in the emerging field of plasmonics, which quantifies the interactions between the electromagnetic field and free electrons in a metal. By trapping sunlight with plasmonics, the solar absorber developed by our team can achieve higher efficiency levels. We look forward to testing the overall solar conversion efficiency of the coating materials in the next step of our research.”
The team’s novel fabrication technique involves patterning a solar absorber with tiny holes with diameters less than 400 nanometers — roughly 1/200 the width of a human hair — cut into the absorber at regular intervals.
The tiny holes penetrate the entire absorber, greatly enhancing the range of solar energy that can be absorbed. Close to 90 percent of all the wavelengths of light that reach Earth’s surface are absorbed by the device. Unlike traditional solar absorbers, this absorber requires very little material and consists of only two layers: a semiconductor film and a reflective metallic layer, with a total thickness of 170 nanometers.
“This idea can be applied to most conventional solar absorbers. With this unique patterning, the absorbers can be boosted to harvest more solar energy from the ultraviolet and visible regions of the electromagnetic spectrum,” says Masdar Institute postdoc Jin You Lu, the paper’s lead author along with MIT postdoc Sang Hoon Nam.
To optimize a solar absorber's efficiency, it is desirable to maximize the solar absorption and reduce the thermal radiation of heat from the absorber. However, it is challenging to create a solar absorber that can absorb a high level of sunlight while maintaining low thermal radiation losses. As the solar absorber takes in more energy, its temperature increases, causing it to lose energy in the form of thermal radiation.
The sweet spot of a solar absorber then, is that point when optimal levels of sunlight are absorbed with the least amount of energy escaping back into the atmosphere through radiation. Lu believes they may have found this sweet spot.
“By taking advantage of the ultrathin film coatings and patterning, we are able to maximize the absorption spectrum while keeping the solar absorber’s emission levels quite low,” Lu explained.
The team is now working to optimize the system with alternative metals such as aluminum, copper, or silver, for the reflective metallic layer, which will reduce the costs of the solar absorber even further.
Testimonial
"Advertising in PCB007 Magazine has been a great way to showcase our bare board testers to the right audience. The I-Connect007 team makes the process smooth and professional. We’re proud to be featured in such a trusted publication."
Klaus Koziol - atgSuggested Items
Global PCB Connections: Understanding the General Fabrication Process—A Designer’s Hidden Advantage
08/14/2025 | Markus Voeltz -- Column: Global PCB ConnectionsDesigners don’t need to become fabricators, but understanding the basics of PCB fabrication can save you time, money, and frustration. The more you understand what’s happening on the shop floor, the better you’ll be able to prevent downstream issues. As you move into more advanced designs like HDI, flex circuits, stacked vias, and embedded components, this foundational knowledge becomes even more critical. Remember: the fabricator is your partner.
MKS’ Atotech to Participate in IPCA Electronics Expo 2025
08/11/2025 | AtotechMKS Inc., a global provider of enabling technologies that transform our world, announced that its strategic brands ESI® (laser systems) and Atotech® (process chemicals, equipment, software, and services) will showcase their latest range of leading manufacturing solutions for printed circuit board (PCB) and package substrate manufacturing at the upcoming 17th IPCA Show to be held at Pragati Maidan, New Delhi from August 21-23, 2025.
MKS Showcases Next-generation PCB Manufacturing Solutions at the Thailand Electronics Circuit Asia 2025
08/06/2025 | MKS Instruments, Inc.MKS Inc, a global provider of enabling technologies that transform our world, today announced its participation in Thailand Electronics Circuit Asia 2025 (THECA 2025), taking place August 20–22 at BITEC in Bangkok.
Point2 Technology, Foxconn Interconnect Technology Partner to Revolutionize AI Cluster Scalability with Terabit-Speed Interconnect
08/06/2025 | BUSINESS WIREPoint2 Technology, a leading provider of ultra-low-power, low-latency mixed-signal SoC solutions for multi-terabit interconnect, and Foxconn Interconnect Technology (FIT), a global leader in precision interconnect solutions, have signed a Memorandum of Understanding (MOU) to accelerate the commercialization of next-generation Active RF Cable (ARC) and Near Pluggable e-Tube (NPE) solutions.
Advancing Electrolytic Copper Plating for AI-driven Package Substrates
08/05/2025 | Dirk Ruess and Mustafa Oezkoek, MKS’ AtotechThe rise of artificial intelligence (AI) applications has become a pivotal force driving growth in the server industry. Its challenging requirements for high-frequency and high-density computing are leading to an increasing demand for development of advanced manufacturing methods of package substrates with finer features, higher hole densities, and denser interconnects. These requirements are essential for modern multilayer board (MLB) designs, which play a critical role in AI hardware. However, these intricate designs introduce considerable manufacturing complexities.