Watch Out, Silicon Chips. Molecular Electronics Are Coming
July 12, 2016 | ATSEstimated reading time: 3 minutes
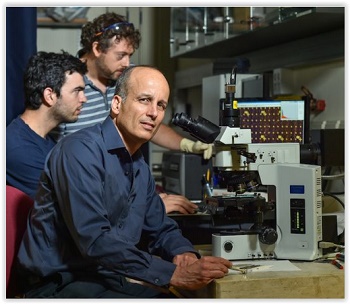
Technion researchers have developed a method for growing carbon nanotubes that could lead to the day when molecular electronics replace the ubiquitous silicon chip as the building block of electronics.
Carbon nanotubes (CNTs) have long fascinated scientists because of their unprecedented electrical, optical, thermal and mechanical properties, and chemical sensitivity. But significant challenges remain before CNTs can be implemented on a wide scale, including the need to produce them in specific locations on a smooth substrate, in conditions that will lead to the formation of a circuit around them.
Led by Prof. Yuval Yaish of the Viterbi Faculty of Electrical Engineering and the Zisapel Nanoelectronics Center at the Technion, the researchers have developed a technology that addresses these challenges. Their breakthrough also makes it possible to study the dynamic properties of CNTs, including acceleration, resonance (vibration), and the transition from softness to hardness.
The method could serve as an applicable platform for the integration of nano-electronics with silicon technologies, and possibly even the replacement of these technologies in molecular electronics.
“The CNT is an amazing and very strong building block with remarkable electrical, mechanical and optical properties,” said Prof. Yaish. “Some are conductors, and some are semiconductors, which is why they are considered a future replacement for silicon. But current methods for the production of CNTs are slow, costly, and imprecise. As such, they generally cannot be implemented in industry.”
Preferential adsorption of p-nitrobenzoic acid on carbon nanotubes. (a) Top: Chemical structure of p-nitrobenzoic acid (pNBA). Bottom: Schematic illustration of the monoclinic unit cell of pNBA powder as extracted from X-ray diffraction analysis. (b,c) Dark field optical microscopy images of pNBA nanocrystals adsorbed along CVD grown carbon nanotubes (CNTs). Scale bar, 50 and 20 µm, respectively. (d) Amplitude image of AFM of a single CNT with a few pNBA nanocrystals along. Scale bar, 1 µm. Inset: height cross sections along the marked lines of the main figure. (e) Dark field optical microscopy image of pNBA nanocrystals after intensive deposition. Note the black voids along the CNT. Scale bar, 20 µm. (f) Dark field optical microscopy image of pNBA nanocrystals adsorb onto commercial dispersed CNTs. Scale bar, 20 µm.
Due to the nanometer size of the CNTs (100,000 times smaller in diameter than the thickness of a human hair) it is extremely difficult to find or locate them at specific locations. Prof. Yaish, and graduate students Gilad Zeevi and Michael Shlafman, developed a simple, rapid, non-invasive and scalable technique that enables optical imaging of CNTs. Instead of depending upon the CNT chemical properties to bind marker molecules, the researchers relied on the fact that the CNT is both a chemical and physical defect on the otherwise flat and uniform surface. It can serve as a seed for the nucleation and growth of small, but optically visible nanocrystals, which can be seen and studied using a conventional optical microscope (CNTs, because of their small size, are too small to be seen in this way). Since the CNT surface is not used to bind the molecules, they can be removed completely after imaging, leaving the surface intact, and preserving the CNT’s electrical and mechanical properties.
“Our approach is the opposite of the norm,” he continued. “We grow the CNTs directly, and with the aid of the organic crystals that coat them, we can see them under a microscope very quickly. Then image identification software finds and produces the device (transistor). This is the strategy. The goal is to integrate CNTs in an integrated circuit of miniaturized electronic components (mainly transistors) on a single chip (VLSI). These could one day serve as a replacement for silicon electronics.”
Prof. Yaish also noted that the ability to demonstrate this principle and create world-class devices was made possible by the unique infrastructures available at the Technion clean room facilities in the Wolfson Microelectronics Center, headed by Prof. Nir Tessler.
Suggested Items
Summit Interconnect Hollister Elevates PCB Prototyping with New TiTAN Direct Imaging System from Technica USA
05/01/2025 | Summit Interconnect, Inc.Summit Interconnect’s Hollister facility has recently enhanced its quick-turn PCB prototyping capabilities by installing the TiTAN PSR-H Direct Imaging (DI) system.
New High Power 3D AXI for Power Electronics from Test Research, Inc.
04/17/2025 | TRITest Research, Inc. (TRI), a leading provider of Test and Inspection solutions for the electronics manufacturing industry, proudly announces the launch of the 3D AXI TR7600HP system. Designed for power semiconductor inspection, the TR7600HP enhances accuracy and efficiency in detecting defects in components such as IGBTs, MOSFETs, SiC inverters, and Paladin Connectors.
Real Time with... IPC APEX EXPO 2025: MivaTek is Revolutionizing Circuit Board Manufacturing with DART Technology
04/02/2025 | Real Time with...IPC APEX EXPOBrendan Hogan from MivaTek Global discusses the company's focus on direct imaging for circuit boards and semiconductors. MivaTek is introducing DART technology for dynamic feature size adjustments. This technology enhances precision, improving registration and throughput.
Real Time with... IPC APEX EXPO 2025: Schmoll America—Committed to Supporting Customers
03/31/2025 | Real Time with...IPC APEX EXPOKurt Palmer of Schmoll America and Stephan Kunz of Schmoll Maschinen GmbH had a great show, reporting solid attendance and good opportunities, as Schmoll America celebrates its first anniversary. With a booth full of equipment for attendees to see and touch, they showcased unique products like the Pico laser and X-ray machine, and discussed plans for a new facility.
Technica USA and CBT Introducing TiTAN Hybrid at IPC APEX EXPO 2025
03/18/2025 | Technica USAThe wait is over! Technica and CBT are proud to unveil TiTAN Hybrid, a groundbreaking innovation set to redefine the PCB industry. Designed for unmatched performance, efficiency, and adaptability, this cutting-edge laser imaging technology brings the future to you—today.