New Way for Stabilizing Battery Recharge
July 18, 2016 | Cornell UniversityEstimated reading time: 3 minutes
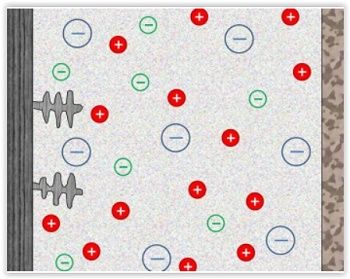
It seems like fairly simple physics: If you construct a barrier that’s stronger than the material trying to penetrate it, the barrier should work.
That is the prevailing wisdom guiding the science of high-capacity rechargeable batteries that use reactive metals as the negative electrode: The membrane that separates the two electrodes should ideally be made of something that’s at least as strong as the metal itself.
“Because of the relatively high modulus [strength] of lithium metal at room temperature, it’s been thought for some time that the only membranes that can enable stable battery operation are ceramics,” said Lynden Archer, the James A. Friend Family Distinguished Professor of Engineering in the School of Chemical and Biomolecular Engineering (CBE).
“Unfortunately, few ceramics are conductive enough to meet other requirements of rechargeable batteries – including fast transport of ions, reasonable cost and manufacturability,” he said. “The status quo understanding has created a technological roadblock in our ability to engineer better batteries.”
However, Archer and a team of Cornell scientists – including doctoral student Mukul Tikekar and CBE professor Donald L. Koch – are defining new paths toward such batteries. Their paper, “Stabilizing electrodeposition in elastic solid electrolytes containing immobilized anions,” was published July 15 in the journal Science Advances.
The work proposes an approach that challenges conventional wisdom: tethering anions (negatively charged ions) in an elastic membrane of any strength could stabilize the battery through non-mechanical means. Tethered anions provide stability to any electrochemical cell that uses reactive metals as electrodes by reducing the electric field at the metal electrode, enhancing stability during recharge.
The team’s latest research builds on its previous work focused on addressing challenges to the design and safety of high-energy batteries, especially those based on metals, such as lithium, that are prone to failure due to tree-like growths called dendrites. These growths can cause short circuits, which can lead to not only the premature end of a battery’s life, but also explosion and fire.
A logical way to slow the sequence of events that lead to a dendrite-induced short is by increasing the strength of the membrane separating the two electrodes, which is the basis of current practice.
“A more fundamental approach would be to understand and thereby stop the nucleation event that produces the dendrites in the first place,” Archer said.
“And the lack of viable ways to reach the present targets of stability and conductivity also underscores the need for solutions outside the box,” Tikekar added.
The new paper shows that when a battery is operated at low power output, positive ions in the battery electrolyte diffuse freely throughout the separator. But at higher currents, negative ions migrate away from the region near the metal electrode, creating a depletion zone, which initiates dendrite formation.
By permanently tethering anions to the membrane, the depletion zone may be neutralized, preventing the chain of events that results in battery failure. This prediction, from Tikekar’s calculations, has already been confirmed experimentally, and the strategies for stabilizing deposition of metals revealed by his analysis has added significantly to the toolset available to materials scientists.
“While tethering anions can slow the development of dendrites, it is the combination of elastic stresses with fixed anions that leads to the complete suppression of dendrites,” Koch said.
Particularly exciting for the group: This method can apply not only to lithium but to other materials, such as sodium and aluminum.
“It turns out that pretty much any battery that uses an energetic anode has this problem [of dendrite growth],” Tikekar said. “And so the fact that in a single framework we can capture the physics that are in part responsible for it and propose methods for addressing it, it’s kind of a big deal. We hope to deepen our understanding by devising experiments to test the model more rigorously.”
The research reported in the Science Advances paper was supported as part of the Energy Materials Center at Cornell, an Energy Frontier Research Center funded by the U.S. Department of Energy.
Suggested Items
Indium to Showcase Innovative Materials Powering AI Technology at Productronica China
03/25/2025 | Indium CorporationAs a proven leader in Metal-Based Thermal Interface materials solutions for future-forward technologies, Indium Corporation will proudly showcase its portfolio of thermal interface materials (TIMs) that enabling AI advancements at Productronica China, March 26-28, in Shanghai, China.
Electroninks' MOD and iSAP Game Changers
03/25/2025 | Marcy LaRont, PCB007 MagazineElectroninks, a prominent player in particle-free conductive inks, recently announced an exciting new range of metal-complex inks for ultra high density interconnect (UHDI) technology. At the SMTA UHDI Symposium in January, Mike Vinson, COO of Electroninks, gave a presentation on this line of MOD inks, which are versatile and suitable for a range of applications that require ultra-dense, miniaturized, and high-frequency technology. Mike says his technology is a game changer and will revolutionize UHDI circuit fabrication.
Curtiss-Wright Wins Rheinmetall Contracts for Vehicle Stabilization Systems
03/25/2025 | Curtiss-Wright CorporationCurtiss-Wright Corporation announced that it has been awarded multiple contracts to provide its turret drive aiming and stabilization technology to Rheinmetall for use on the German Army's Boxer Heavy Weapon Carrier and the Hungarian Ministry of Defence (MoD’s) Lynx infantry fighting vehicles (IFV).
Boulder Scientific Company Completes Investments to serve Polyolefins, Electronics, Aerospace and Defense Sectors
03/14/2025 | PRNewswireBoulder Scientific Company (BSC) announces completion of several investments at its Mead and Longmont, Colorado manufacturing facilities to support customers in the polyolefins, electronics, aerospace and defense sectors.
Rheinmetall Begins MASS Assembly in Australia to Support Royal Australian Navy
03/10/2025 | RheinmetallRheinmetall Defence Australia has begun assembling the first Multi Ammunition Soft Kill System (MASS) ship protection systems in Australia for installation on Royal Australian Navy ships.