-
- News
- Books
Featured Books
- smt007 Magazine
Latest Issues
Current IssueMoving Forward With Confidence
In this issue, we focus on sales and quoting, workforce training, new IPC leadership in the U.S. and Canada, the effects of tariffs, CFX standards, and much more—all designed to provide perspective as you move through the cloud bank of today's shifting economic market.
Intelligent Test and Inspection
Are you ready to explore the cutting-edge advancements shaping the electronics manufacturing industry? The May 2025 issue of SMT007 Magazine is packed with insights, innovations, and expert perspectives that you won’t want to miss.
Do You Have X-ray Vision?
Has X-ray’s time finally come in electronics manufacturing? Join us in this issue of SMT007 Magazine, where we answer this question and others to bring more efficiency to your bottom line.
- Articles
- Columns
Search Console
- Links
- Media kit
||| MENU - smt007 Magazine
Divergence in Test Results Using IPC Standard SIR and Ionic Contamination Measurements
August 1, 2016 | Karen Tellefsen, Alpha Assembly SolutionsEstimated reading time: 8 minutes
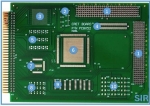
Controlled humidity and temperature controlled surface insulation resistance (SIR) measurements of flux covered test vehicles, subject to a direct current (DC) bias voltage, are recognized by a number of global standards organizations as the preferred method to determine if no-clean solder paste and wave soldering flux residues are suitable for reliable electronic assemblies. The Association Connecting Electronics Industries (IPC), Japanese Industry Standard (JIS), Deutsches Institut fur Normung (DIN) and International Electrical Commission (IEC) all have industry reviewed standards using similar variations of this measurement.
Ionic contamination testing is recognized by the IPC as a standard for evaluating the cleanliness of assemblies that have been subjected to a cleaning process. IPC J-STD001F calls for a cleanliness level of
IPC-TM-650 Method 2.3.25 contains standard test methods for extracting contaminants from circuit boards using heated isopropanol (IPA) / water mixtures. Test method 2.3.25 is commonly referred to as the ROSE (resistivity of solvent extract) test. Previous work1,2 has shown poor correlation between the presence of extractable, corrosive weak organic acids and results from IPC-TM-650 2.3.25 test results, partially due to the lack of solubility of materials found in no-clean fluxes, and the higher SIR values imparted by rosins and resins in modern no-clean soldering materials.
This study will compare the results from testing two solder pastes using the IPC-J-STD-004B IPC TM-650 2.6.3.7 surface insulation resistance test and IPC TM-650 2.3.25 in an attempt to investigate the correlation of ROSE methods as predictors of electronic assembly electrical reliability.
Introduction
Ionic contamination testing has been traced back to work done at the United States Naval Avionics Center in Indianapolis in the early 1970s by Hobson and DeNoon3. This work eventually led to the development of the 1.56 µg/cm2 (10 µg/inch²) NaCl equivalent standard for ionics extracted using an IPA/water mixture. High volume circuit assembly at the time used only wave soldering processes, employing foam fluxers to apply RMA flux followed by a post soldering cleaning process with fluorocarbon solvents.
This ionic contamination limit became part of now defunct Mil Spec P-288094 and Mil STD-2000A, but has been carried through versions A through F of ANSI/J-STD-001. This manual procedure has become more automated with the invention of descriptively branded test equipment such as the Contaminometer, Ionograph and Omega Meter. Although these measuring devices improve the efficiency and accuracy of measuring ionic contamination soluble in alcohol/water mixtures, they also increase the amount of ionic material measured5, 6.
IPC-9202 describes a procedure for qualifying a process for electrical reliability by measuring SIR using IPC TM-650 2.6.3.7 and IPC TM-650 2.3.28 by using the IPC-B-52 test coupon. This coupon is shown in Figure 1. The standard calls for a minimum SIR value of 100MΩ, but only calls for a measure and report of the ionic contamination. The reported ionic contamination then becomes a benchmark for “future trouble shooting or process improvement efforts.”
The experiments carried out in this work were designed to use methodology derived from IPC-9202 to determine if it is possible to have a solder paste that passes SIR standard of >100 MΩ, but fails the ionic contamination level of ANSI/J-STD-001f, and determine if a second solder paste fail the SIR test and pass the ROSE test standard.
Figure 1: IPC B-52 test coupon comprising a SIR test coupon (SIR) and a section for ionic contamination measurements (SIR). Component ID: 1 – TH connector 4 x 24 pins; 2 – Capacitor, 10 pF, 0402 package; 3 – BGA, 256 IO, 1 mm pitch, isolated; 4 – SM connector IEEE 1386, 2 x 16 pins; 5 – Capacitor, 10 pF, 0805 package; 6 – QFP160, 0.65 mm pitch, isolated; 7 – QFP80, 0.5 mm pitch, isolated; 8 – Capacitor, 10 pF, 0603 package; 9 – SOIC16, 1.27 mm pitch, isolated; 10 – Capacitor, 10 pF, 1206 package.
Methodology
Two different SAC305 solder pastes were printed and reflowed on IPC B-52 test coupons (Figure 1). The assembled coupons were broken into two separate test vehicles after the solder pastes were printed, populated and reflowed. The section of the board on the center right was used to measure ionic contamination. The left portion of the test vehicle was used to measure SIR. The four smaller panels on the far right were discarded. A schematic diagram of the Ionograph that was used is depicted in Figure 2. The Ionograph is considered a “dynamic” ROSE measurement in which the extraction solution is continuously passed through ion exchange columns that remove the ionic material in the solution. A conductivity bridge detects ions in solution, and a flow meter measures the volume of solution passing by the conductivity bridge, allowing ionic contamination to be integrated with extraction solution volume.
A second measurement using three IPC-B-24 coupons (usually used for single material SIR measurements) for each of the two pastes was made.
Figure 2: Schematic diagram of the “Ionograph.”
Page 1 of 4
Suggested Items
Bridging the Knowledge Gap in Test: A Conversation with Bert Horner
06/11/2025 | Barry Matties, I-Connect007Bert Horner is a seasoned industry veteran and co-creator of The Test Connection, Inc. (TTCI), a test and inspection company spanning over 45 years. In this candid conversation, Bert reflects on the challenges our industry faces with the retirement of career professionals and the subsequent loss of critical tribal knowledge. As he unveils The Training Connection’s innovative training initiatives, Bert emphasizes the importance of evolving educational programs that align with industry needs, particularly in design for test (DFT), and sheds light on strategies being implemented to foster the next generation of engineers.
IPC Hall of Fame Spotlight Series: Highlighting Bob Neves
06/11/2025 | Dan Feinberg, I-Connect007Many IPC members who have contributed significantly to IPC and our industry have been awarded the IPC Raymond E. Pritchard Hall of Fame (HOF) Award. This Hall of Fame spotlight features industry veteran Bob Neves, who joined IPC in 1986 and was inducted into the IPC Hall of Fame in 2007.
Top Tech in Taiwan: IPC's Blueprint to Advance Smart Manufacturing
06/04/2025 | Sydney Xiao, IPCRenowned as a global hub of innovation and a cornerstone of the electronics industry, Taiwan is leading advancements in technology and manufacturing. A decade ago, IPC established an office in Taiwan, embedding itself deeply in this innovative ecosystem. Now with nearly 200 member companies in the region, IPC remains dedicated to driving standardization, education, and technological progress in Taiwan’s electronics manufacturing sector.
IPC Releases Latest Standards and Revisions Updates
06/05/2025 | IPCEach quarter, IPC releases a list of standards that are new or have been updated. To view a complete list of newly published standards and standards revisions, translations, proposed standards for ballot, final drafts for industry review, working drafts, and project approvals, visit ipc.org/status. These are the latest releases for Q1 2025.
IPC Launches New Wire Harness Design Course Led by Defense Industry Expert
06/03/2025 | I-Connect007 Editorial TeamIPC is expanding its educational offerings with a new online course designed to provide foundational knowledge in wire harness and cable design. The course, Introduction to Wire Harness Design I, is led by a seasoned mechanical engineer and subject matter expert in military cable systems working at FNSS Defense Systems in Turkey.