-
- News
- Books
Featured Books
- pcb007 Magazine
Latest Issues
Current IssueInventing the Future with SEL
Two years after launching its state-of-the-art PCB facility, SEL shares lessons in vision, execution, and innovation, plus insights from industry icons and technology leaders shaping the future of PCB fabrication.
Sales: From Pitch to PO
From the first cold call to finally receiving that first purchase order, the July PCB007 Magazine breaks down some critical parts of the sales stack. To up your sales game, read on!
The Hole Truth: Via Integrity in an HDI World
From the drilled hole to registration across multiple sequential lamination cycles, to the quality of your copper plating, via reliability in an HDI world is becoming an ever-greater challenge. This month we look at “The Hole Truth,” from creating the “perfect” via to how you can assure via quality and reliability, the first time, every time.
- Articles
- Columns
- Links
- Media kit
||| MENU - pcb007 Magazine
Happy’s Essential Skills: Quality Functional Deployment (QFD)
August 24, 2016 | Happy HoldenEstimated reading time: 10 minutes
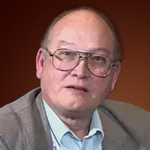
Wikipedia has one of the best definitions of quality function deployment (QFD): “QFD is a method to help transform customer needs (the voice of the customer or VOC) into engineering characteristics (and appropriate test methods) for a product or service. It helps create operational definitions of the requirements, which may be vague when first expressed. It prioritizes each product or service characteristic while simultaneously setting development targets for the product or service.”
As described by Dr. Yoki Akao, who originally developed QFD in Japan in 1966, it is a “method to transform qualitative user demands into quantitative parameters, to deploy the functions forming quality, and to deploy methods for achieving the design quality into subsystems and component parts, and ultimately to specific elements of the manufacturing process.” The author combined his work in quality assurance and quality control points with function deployment used in value engineering.
QFD is designed to help planners focus on characteristics of a new or existing product or service from the viewpoints of market segments, company, or technology-development needs. The technique yields charts and matrices.
Introduction
I came to use QFD when HP was using it as a fundamental piece of its “Product Definition Process.” I attended a two-day QFD course taught by the American Suppliers Institute (ASI) in 1989. It is particularly useful in navigating the various phases of breaking down “Customer Needs and Requirements” into the technical levels of “Technology Planning,” “Product Definitions,” and Roadmaps as seen in Figure 1. It is interrelated to the following past columns:
- 1. Six Sigma
- 7. Project/Program Life Cycle
- 9. Figure of Merit
- 10. DFM/A
- 12. Project/Program Management
- 13. Benchmarking
- 15. Roadmapping
And QFD will influence the following of my future columns:
- 17. Automation/CIM
- 18. Computer-Aided-Manufacturing
- 21. 10-STEP Business Planning
Figure 1: QFD is an essential tool in customer driven product plans and roadmaps.
QFD Processes
Quality Function Deployment consists of four main steps:
- Identify the customer's vital requirements for the product or service and translate them into design requirements.
- Develop a service blueprint of an elegant, effective, and efficient delivery process.
- Evaluate alternative designs.
- Implement the newly designed process for delivery of the product or service
The methodologies of QFD can be quite involved, but are based on the six parts of the “House of Quality” as seen in Figure 2:
- Customer requirements
- Planning matrix
- Technical requirements
- Interrelationships
- Roof
- Targets
Figure 2: Elements of the House of Quality (HOQ).
The House of Quality (a simplification of the 6-part QFD House) is well explained in an article published in the Harvard Business Review, “House of Quality,” by John R. Hauser and Don Clausing[1].
The following is an excerpt from the QFD Tutorial-Webducate publication on the Web[2]:
Customer Requirements—This is generally the first portion of the HOQ matrix to be completed and also the most important. It documents a structured list of a product’s customers’ requirements described in their own words (VOC). This information is usually gathered through conversations with customers in which they are encouraged to describe their needs and problems.
The list of requirements gathered in such an exercise must be structured before its entry into the HOQ. The construction of an affinity diagram can be used to do this.
Planning Matrix—The planning matrix attaches to the right side of the HOQ matrix and serves several purposes. Firstly, it quantifies the customers’ requirement priorities and their perceptions of the performance of existing products. Secondly, it allows these priorities to be adjusted based on the issues that concern the design team. The measures used in this section are generally gathered from customers using a questionnaire. The first and most important measure in this section is the requirement ‘importance weighting.’ This figure quantifies the relative importance of each of the customer requirements (described in the left hand portion of the HOQ matrix) from the customers’ own perspective. This measure is often shown in a column alongside the customer requirement description in the left section of the HOQ matrix. The ‘weightings’ of the customer requirements can use the figure of merit (FOM) process to find their importance.
Technical Requirements—This section of the HOQ matrix is also referred to as the engineering characteristics or ‘voice of the company.’ It describes the product in terms of the company. This information is generated by the QFD design team who identify all the measurable characteristics of the product which they perceive are related to meeting the specified customer requirements. Again, the affinity diagram is applied to interpret these product characteristics. An additional row is often included in this section to illustrate the direction of change in each of these variables, which is considered to result in an improvement in product performance.
Interrelationships—This section forms the main body of the HOQ matrix and can be very time-consuming to complete. Its purpose is to translate the requirements as expressed by the customer into the technical characteristics of the product. Its structure is that of a standard two-dimensional matrix with cells that relate to combinations of individual customer and technical requirements. It is the task of the QFD team to identify where these interrelationships are significant. Each combination of customer and technical requirement is considered in turn by the QFD team.
The level of interrelationship discerned is weighted usually on a four-point scale (high, medium, low, none) and a symbol representing this level of interrelationship is entered into the matrix cell.
Roof—The triangular “roof” matrix of the HOQ is used to identify where the technical requirements that characterize the product support or impede one another. As in the interrelationship section, the QFD team work through the cells in the roof matrix considering the pairing of technical requirements these represent. In using a paired ranking, the question is: “Does improving one requirement cause a deterioration or improvement in the other technical requirement?” Where the answer is a deterioration, an engineering trade-off exists and a symbol is entered into the cell to represent this (usually a cross or “-“). Where improving one requirement automatically leads to an improvement in the other requirement, an alternative symbol is entered into the cell (usually a tick or “+”). Different levels of such positive or negative interaction (e.g., strong/medium/weak) can be indicated using different colored symbols. The information recorded in the roof matrix is useful to the design team in several ways. It highlights where a focused design improvement could lead to a range of benefits to the product.
It also focuses attention on the negative relationships in the design. These can represent opportunities for innovative solutions to be developed which avoid the necessity for such compromises being made.
Targets—This is the final section of the HOQ matrix to be completed and it summarizes the conclusions drawn from the data contained in the entire matrix and the team’s discussions. It is generally made up from three parts:
- 1. Technical priorities
- 2. Competitive benchmarks
- 3. Targets
Technical Priorities—The relative importance of each technical requirement of the product in meeting the customer’s specified needs, can be simply calculated from the weightings contained in the planning and interrelationship matrix sections. Each interrelationship weighting is multiplied by the overall weighting from the planning matrix. These values are then summed down the columns to give a priority score for each technical requirement.
Competitive Benchmarking—Each of the technical requirements that have been identified as important characteristics of the product can be measured both for the company’s own existing product and the available competitive products. This illustrates the relative technical position of the existing product and helps to identify the target levels of performance to be achieved in a new product.
Targets—The final output of the HOQ matrix is a set of engineering target values to be met by the new product design. The process of building this matrix enables these targets to be set and prioritized based on an understanding of customer needs, the competitor performance and the organization’s current performance. The QFD team now need to draw on all this information when deciding on these values.
Page 1 of 2
Testimonial
"The I-Connect007 team is outstanding—kind, responsive, and a true marketing partner. Their design team created fresh, eye-catching ads, and their editorial support polished our content to let our brand shine. Thank you all! "
Sweeney Ng - CEE PCBSuggested Items
MS2 Technologies, LLC/P. Kay Focuses on Central America with First Installation in Honduras
08/24/2025 | P. Kay Metal, Inc.This year MS2 Technologies has turned their focused to the growing electronics market in Central America. With that focus came the adaptation of MS2 and the Akila System from a Honduras-based corporation with manufacturing plants in both Honduras and Mexico.
BEST Inc. Provides High-Reliability BGA Reballing and Component Rework Services
08/22/2025 | BEST Inc.BEST Inc., a leader in electronic component services, is pleased to announce its component rework services are available for all types of area array devices including ball grid array, land grid array and quad flat no-lead SMT packages.
Indium Corporation Promotes Two Leaders in EMEA (Europe, Middle East, and Africa) Markets
08/05/2025 | Indium CorporationWith its commitment to innovation and growth through employee development, Indium Corporation today announced the promotions of Andy Seager to Associate Director, Continental Sales (EMEA), and Karthik Vijay to Senior Technical Manager (EMEA). These advancements reflect their contributions to the company’s continued innovative efforts with customers across Europe, the Middle East, and Africa (EMEA).
MacDermid Alpha Electronics Solutions Unveils Unified Global Website to Deepen Customer, Talent, and Stakeholder Engagement
07/31/2025 | MacDermid Alpha Electronics SolutionsMacDermid Alpha Electronics Solutions, the electronics business of Elements Solutions Inc, today launched macdermidalpha.com - a unified global website built to deepen digital engagement. The launch marks a significant milestone in the business’ ongoing commitment to delivering more meaningful, interactive, and impactful experiences for its customers, talent, and stakeholders worldwide.
KOKI to Showcase Analytical Services and New HF1200 Solder Paste at SMTA Guadalajara 2025
07/31/2025 | KOKIKOKI, a global leader in advanced soldering materials and process optimization services, will exhibit at the SMTA Guadalajara Expo & Tech Forum, taking place September 17 & 18, 2025 at Expo Guadalajara, Salón Jalisco Halls D & E in Guadalajara, Mexico.