-
- News
- Books
Featured Books
- smt007 Magazine
Latest Issues
Current IssueWhat's Your Sweet Spot?
Are you in a niche that’s growing or shrinking? Is it time to reassess and refocus? We spotlight companies thriving by redefining or reinforcing their niche. What are their insights?
Moving Forward With Confidence
In this issue, we focus on sales and quoting, workforce training, new IPC leadership in the U.S. and Canada, the effects of tariffs, CFX standards, and much more—all designed to provide perspective as you move through the cloud bank of today's shifting economic market.
Intelligent Test and Inspection
Are you ready to explore the cutting-edge advancements shaping the electronics manufacturing industry? The May 2025 issue of SMT007 Magazine is packed with insights, innovations, and expert perspectives that you won’t want to miss.
- Articles
- Columns
- Links
- Media kit
||| MENU - smt007 Magazine
Reflections on 40 Years of Test and Measurement and What Lies Ahead
January 24, 2017 | James Truchard, PhD, National InstrumentsEstimated reading time: 8 minutes
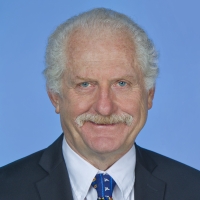
As I approach the end of my 40-year career as CEO of National Instruments, I am reminded of the great progress and innovations the test and measurement industry has witnessed since 1976. We have gone from an industry driven by vacuum tube technology in the era of General Radio to a time when the transistor ruled with Hewlett Packard to today, when software truly is the instrument—a transition that NI helped shepherd.
Moore’s law has taken us for a wild, fast ride to say the least, and just when you think it’s run its course, process innovations extend into new dimensions (literally) and push performance even further.
Just like the transistor, NI started from humble beginnings, but it has relentlessly focused on engineering great products and empowering world- changing innovation through our customers and platform technology. Allow me to reminisce on what the past 40 years have taught me and where I see this market heading as I shift into the next phase of my career.
Do for Test and Measurement What the Spreadsheet Did for Financial Analysis
When Jeff Kodosky, Bill Nowlin, and I started NI in 1976, we saw tremendous room for innovation in how engineers and scientists interacted with and built test and measurement equipment. We founded the company on the premise that there had to be a better way to serve the test and measurement needs that we, engineers and scientists, faced. We couldn’t buy it off the shelf but at least we wouldn’t have to build it from scratch.
The general purpose interface bus (GPIB, IEEE 488) was our gateway. Our vision, as stated in 1983, was to “do for test and measurement what the spreadsheet did for financial analysis.” Stated today, the sentence loses some of its power, but think about the early ’80s. At the time, the tools for financial analysis were “locked up” and too expensive for anyone without a big budget to access them. The early incarnations of spreadsheets turned this situation on its head, and that is exactly what we wanted to do. We wanted to make it so that any engineer or scientist could access the same tools or platform used by the R&D teams of the leading technology companies. It was a radically empowering view at the time and, in many ways, it still is.
The Software is the Instrument
While others might have seen GPIB as a hardware play, we recognized it for what it enabled in terms of software. As the PC industry evolved (as well as Apple’s Mac, which we had a special affinity for given its graphical user interface), that GPIB cable made it easy to analyze and present data in a customized way for our customers’ needs. They were no longer confined to the front panel of an instrument and their pencils and notepads for data acquisition. The opportunity to innovate then shifted to the software world, where programming languages needed instrument drivers for the connected boxes. Our strategy of writing and supporting those drivers offered a critical service that continues today as NI supports more than 10,000 drivers on the company’s Instrument Driver Network.
But that world still left engineers and scientists with the burden of using tools designed for computer science to perform engineering, test, and measurement tasks. Our answer was twofold: LabWindows/CVI, to offer engineering-specific tools in ANSI C programming, and LabVIEW, a graphical programming paradigm that took the way we think about solving a problem (in flowcharts and pictures) and turned it into compiled code. The story was simple: acquire, analyze, and present. Do it in software tools designed for a customer’s use case that were easy to learn yet extremely powerful. We coined the phrase ”The software is the instrument” to describe this approach, and seeing engineers and scientists save valuable time and get to results faster was all the market validation we ever needed.
Evolving With Moore's Law
People talk about Moore's law like it’s about hardware, but computational hardware exists only to run software (and maybe firmware). Once we made test and measurement all about software, we had effectively enlisted Intel, Xilinx, and many other billion dollar companies in our R&D staff. With customers and partners building proficiency with our software tools, we just had to follow the chips to deliver increasing value to test and embedded systems. This has happened, so far, along two key dimensions: multicore processors and FPGAs.
Because LabVIEW is graphical and, therefore, not obviously sequential, it is tailor-made for parallel processing. LabVIEW users were among the first programmers to easily migrate from single-core processors to multiple threads and multiple cores and see almost instant speed improvements. Obviously, it’s possible to take advantage of these trends with other languages, just like it’s still possible to write highly efficient code in machine or assembly language, but why would you? The pace of change in modern electronics means you can’t waste time doing by hand what a tool can easily do for you, and we hear that over and over from LabVIEW users.
That goes to an entirely different level with FPGAs. Some problems are just better solved in the highly parallel, deterministic world of silicon. But the toolchains and programming constructs were inaccessible to most mechanical engineers or medical researchers who were experts in their measurements and problems to solve (not digital design). We recognized this in the late 1990s with LabVIEW’s graphical paradigm. We were on a quest to deliver the power of FPGAs to LabVIEW programmers, and we’ve done that. A quick look at our Engineering Impact Awards winners demonstrates the power of this technology: applications ranging from regenerating and restoring organ function damaged by disease or trauma to setting a world record in 5G wireless spectrum efficiency with massive MIMO.
A Software-Centric Approach to Hardware Design
When you think about software as uniquely as we have, it’s easy to think differently about hardware, too. Modular, PC-based plug-in boards were a natural by-product. Make the hardware as lightweight and cost-effective as possible (no dedicated screens, power supplies, fixed buttons/knobs, and so on) and focus on ADCs, DACs, signal conditioning, and data movement.
I have yet to see a test and measurement vendor design a user interface better than a customer, for any specific task, that makes the customer more productive. Even the best front panels on box instruments are cluttered with unused buttons or menu structures. Many of our hardware products have size constraints dictated by the I/O connector. Can it get more efficient than that?
The reality is our strategy is more than just efficient; it’s right. Take the new Vector Signal Transceiver (VST), which combines an RF analyzer, RF generator, parallel and serial digital interfaces, and high-performance signal processing into a two-slot PXI module. This product delivers industry-leading bandwidth (1 GHz), amazing RF performance, and scalability for MIMO applications for one reason: software. We moved as many technical problems into the FPGA as we could, and Moore’s law (along with Xilinx) delivered a vehicle capable of handling the computation. We, in turn, passed the keys to that vehicle over to our customers by allowing them to customize that FPGA with LabVIEW. From 5G cellular technology development to automotive radar and driver assist algorithm development to reductions in the cost of Internet of Things (IoT) devices, the VST and LabVIEW are helping customers achieve goals conventional instruments quite simply prevent them from obtaining.
Page 1 of 2
Suggested Items
The Global Electronics Association Releases IPC-8911: First-Ever Conductive Yarn Standard for E-Textile Application
07/02/2025 | Global Electronics AssociationThe Global Electronics Association announces the release of IPC-8911, Requirements for Conductive Yarns for E-Textiles Applications. This first-of-its-kind global standard establishes a clear framework for classifying, designating, and qualifying conductive yarns—helping to address longstanding challenges in supply chain communication, product testing, and material selection within the growing e-textiles industry.
Magnalytix and Foresite to Host Technical Webinar on SIR Testing and Functional Reliability
06/26/2025 | MAGNALYTIXMagnalytix, in collaboration with Foresite Inc., is pleased to announce an upcoming one-hour Webinar Workshop titled “Comparing SIR IPC B-52 to Umpire 41 Functional & SIR Test Method.” This session will be held on July 24, 2025, and is open to professionals in electronics manufacturing, reliability engineering, and process development seeking insights into new testing standards for climatic reliability.
Defense Speak Interpreted: Is DARPA Still Around After CHIPS?
06/24/2025 | Dennis Fritz -- Column: Defense Speak InterpretedWhen I first published my Defense Speaks Interpreted column in January 2019 on the Defense Advanced Research Projects Agency (DARPA ERI), the agency advocated for an expanded Defense emphasis on closing the growing technology gap in microelectronics. The emphasis was on “resurgence.”
I-Connect007 Editor’s Choice: Five Must-Reads for the Week
06/13/2025 | Marcy LaRont, I-Connect007Today is Friday the 13th, and in much of Western folklore, this is a day when bad luck is lurking. But while Friday the 13th may top Western superstition charts, the global calendar is sprinkled with its own unlucky legends. In Spain and Greece, the bad juju lands on Tuesday the 13th—a day linked to Mars, the god of war, and naturally, chaos. In Italy, it’s Friday the 17th that is feared, thanks to the Roman numeral XVII, which can be rearranged to spell VIXI—Latin for “I have lived” (a poetic way of saying you’re dead).
TTCI Celebrates Melanie Rutkauskas’ 10-Year Anniversary and Her Leadership of New Training Division
06/12/2025 | TTCIThe Test Connection Inc. (TTCI), a leading provider of electronic test and manufacturing solutions, is proud to celebrate Melanie Rutkauskas on her 10-year anniversary with the company.