-
- News
- Books
Featured Books
- smt007 Magazine
Latest Issues
Current IssueSupply Chain Strategies
A successful brand is built on strong customer relationships—anchored by a well-orchestrated supply chain at its core. This month, we look at how managing your supply chain directly influences customer perception.
What's Your Sweet Spot?
Are you in a niche that’s growing or shrinking? Is it time to reassess and refocus? We spotlight companies thriving by redefining or reinforcing their niche. What are their insights?
Moving Forward With Confidence
In this issue, we focus on sales and quoting, workforce training, new IPC leadership in the U.S. and Canada, the effects of tariffs, CFX standards, and much more—all designed to provide perspective as you move through the cloud bank of today's shifting economic market.
- Articles
- Columns
- Links
- Media kit
||| MENU - smt007 Magazine
High-Volume Test Strategies
June 19, 2017 | Stephen Las Marias, I-Connect007Estimated reading time: 5 minutes
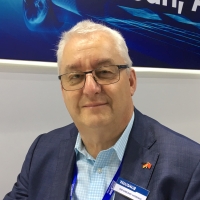
Teradyne is one of the leading providers of test solutions for applications such as component tests, board tests or final product tests. Siegmund Hornig is the director of global sales for Europe and Asia, for production board test division at Teradyne. In an interview with I-Connect007 during the recent NEPCON China event in Shanghai, China, he discusses the new testing demands from customers, and strategies to help them address their high-volume test requirements.
Stephen Las Marias: What are the new testing requirements you are seeing right now from your customers?
Siegmund Hornig: A few years ago, the industry discussed with us about future test requirements, test features and so on. What we see is that the market is drastically changing. Of course, our customers' expectation is that we have all the technology in place to be able to test today's boards and future boards. The focus, however, is on productivity.
We did a research a couple of years ago to understand where the market was going. Surprisingly, we did not get confronted with any technical requirements, but with aspects such as less floor space, higher throughput, and higher level of automation. So, from that point of view, what we did is we worked with some key customers to implement it. We created a so-called building block, which consists of single testers that can be stacked up. A tester has always enough pins, and if we add a second tester to it, then the goal is to double the capacity of the unit. We have significantly reduced floor space, and we have multiple testers in machines to deliver very, very high throughput.
The reason we can provide that is that we also offer very high pin count solutions. We are offering test systems that can go beyond 15,000 pins per machine. To achieve that, we developed a very high-density card, which we use on regular machines to make them significantly smaller. What helps us at the high end to be able to test big boards also helps us on the lower end to make machines very, very small and to be able to add incremental testers to duplicate or triple the speed of the machines.
That helps high volume manufacturers to be able to put machines in as part of the SMT line because they do not run into any volume issues or throughput issues. Today, we do that predominantly with, for example, automotive customers. We build our building block into our own handling machines, but we also have a lot of automotive customers who work with system integrators, where the system integrator tries to combine in-circuit testing, flushing, depanelization, marking—all in one unit. So they do very customized solutions for the OEM to optimize his manufacturing floor, and due to the fact that we offer our equipment with different kinds of electrical interfaces, we are easy to get integrated into these machines.
Today, we are already working with integrators here in China. There's a lot of integrators that use our equipment to put into their machinery. And that is what I see as a trend in the future, to be able to accommodate the productivity requirement and accommodate the request for significant smaller floor space. In Asia, floor space is important, but not as important as you can imagine in Europe, where everybody runs out of space. The management usually says, “We are not extending any factory. If you want to improve, increase productivity, you have to do it with the given floor space or you have to move manufacturing outside.” In Europe, nobody builds a new factory. Here in China, you see a lot of new factories, so that is the difference. The floor space requirement in Europe is even harsher than here in Asia.
Las Marias: How do you address the high-volume requirements here in China?
Hornig: We have two solutions. We have one system which is a dedicated in-line machine. The building blocks testers we move into that in-line machine can be of different configurations, analog only or hybrid, which means digital and analog. With two testers in such a machine, we can do the highest level of throughput. We have done such a machine for an EMS customer who is manufacturing notebooks—they are doing 9,000 notebooks per day with one of our machines in one SMT line. So that’s very, very high volume.
For customers who are also interested in throughput but don't go to that extreme, we have an off-line machine combined with a collaborative robot. Two years ago, Teradyne acquired a Danish company named Universal Robots, which provide robot solutions for the industry. We use these machines also to automate our offline machines. We have several customers already, where they use our robots together with our machines to automate their manufacturing. So we can offer different kinds of automation solutions, totally in-line or as a test cell, if you want, being operated by robots.
Las Marias: What is your Industry 4.0 strategy?
Hornig: The Industry 4.0 strategy comes one level up. What we need to do when we go into an SMT line is the communication between our machine and the MES, the manufacturing execution system. That has been standard for some years. What we added to that one now is the ability to calibrate or control our machine, depending on the information from the MES systems. We have customers that require changing test parameters depending on the product to be tested, which we identify via barcode. We read the barcode, we go on the server to get the information from the MES system, the MES system says whether the port should be tested, and then downloads the set of parameters we test against. After test, we feedback the parameters that are programmed to the unit and whatever. So, there's a complete set of communication in terms of what parameter to test or what kind of software to load, and we then give the calibration data back and the test results back.
Las Marias: What do you think are the most important factors to consider when selecting a test solution?
Hornig: For me, the most important is that you fit into the customer’s environment in terms of space and speed. That is number one. Number two is you need to have interfaces available and you need to have engineers available to adapt to their environment. Because with Industry 4.0 today, not every customer has the same or common solution. All customers are doing certain things special, and you have to have the knowledge in-house and in the field to tweak and adapt to these specific requirements. And that is what I'm very glad here in China, because in the past, we only had that intelligence in Europe. Over the last years, we’ve moved that here to China as well, so that with my team here locally, I can do all the adaptations directly for the customer—and that helps them to fully integrate our machines in their manufacturing process.
Las Marias: Siegmund, thank you very much for this opportunity.
Hornig: Thank you.
Testimonial
"We’re proud to call I-Connect007 a trusted partner. Their innovative approach and industry insight made our podcast collaboration a success by connecting us with the right audience and delivering real results."
Julia McCaffrey - NCAB GroupSuggested Items
Atg Launches Latest Large Format Test System, A9XL, with 8 Heads and 48” x 26” Panel Capability
08/01/2025 | atg Luther & Maelzer GmbHatg Luther & Maelzer GmbH (a Mycronic company) is proud to roll out a new large format test system generation based on the latest high speed atg A9 (board size up to 24” x 21”) and A9L platform.
Magnalytix’s Dr. Mike Bixenman to Guide PDC at SMTA High-Reliability Cleaning and Conformal Coating Conference
07/31/2025 | MAGNALYTIXMagnalytix, providing real-time reliability solutions for electronics manufacturing, is excited to announce that Dr. Mike Bixenman will present the professional development course “The Effects of Flux Residues and Process Contamination on the Reliability of the Electronic Assembly” on Wednesday, Aug. 13 at 9:00 AM CST to open the second day of the STMA High-Reliability Cleaning and Conformal Coating Conference.
TRI to Exhibit at SMTA Queretaro Expo 2025
07/16/2025 | TRITest Research, Inc. (TRI), the leading provider of test and inspection systems for the electronics manufacturing industry, is pleased to announce plans to exhibit at the SMTA Querétaro Expo 2025, scheduled to take place on July 24, 2025, at the Querétaro Centro de Congresos y Teatro Metropolitano.
Knocking Down the Bone Pile: Addressing End-of-life Component Solderability Issues, Part 4
07/16/2025 | Nash Bell -- Column: Knocking Down the Bone PileIn 1983, the Department of Defense identified that over 40% of military electronic system failures in the field were electrical, with approximately 50% attributed to poor solder connections. Investigations revealed that plated finishes, typically nickel or tin, were porous and non-intermetallic.
Meet the Author Podcast: Martyn Gaudion Unpacks the Secrets of High-Speed PCB Design
07/16/2025 | I-Connect007In this special Meet the Author episode of the On the Line with… podcast, Nolan Johnson sits down with Martyn Gaudion, signal integrity expert, managing director of Polar Instruments, and three-time author in I-Connect007’s popular The Printed Circuit Designer’s Guide to... series.