-
- News
- Books
Featured Books
- smt007 Magazine
Latest Issues
Current IssueMoving Forward With Confidence
In this issue, we focus on sales and quoting, workforce training, new IPC leadership in the U.S. and Canada, the effects of tariffs, CFX standards, and much more—all designed to provide perspective as you move through the cloud bank of today's shifting economic market.
Intelligent Test and Inspection
Are you ready to explore the cutting-edge advancements shaping the electronics manufacturing industry? The May 2025 issue of SMT007 Magazine is packed with insights, innovations, and expert perspectives that you won’t want to miss.
Do You Have X-ray Vision?
Has X-ray’s time finally come in electronics manufacturing? Join us in this issue of SMT007 Magazine, where we answer this question and others to bring more efficiency to your bottom line.
- Articles
- Columns
Search Console
- Links
- Media kit
||| MENU - smt007 Magazine
BTC and SMT Rework Challenges
October 5, 2017 | Joerg Nolte, Ersa GmbHEstimated reading time: 4 minutes
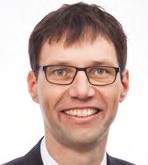
Rising customer demands in the field of PCB repair are a daily occurrence as the rapidly evolving electronics industry follows new trends in a blink of an eye. New strategies and technologies are required to fulfill those demands.
Out of the long list of today's customer demands for efficient BTC and SMT PCB repair, some subjects show up on a daily basis and are generally agreed upon as relevant for the coming years:
• BTC types with new effects: voidless treatment
• Smaller components: miniaturization (01005 capability)
• Large board handling: dynamic preheating for large board repair
• Repeatable processes: flux and paste application (dip and print), residual solder removal (scavenging), dispensing, multiple component handling, and traceability
• Operator support: higher automation, software guidance (human computer interface)
• Cost effectiveness: rework systems for different budgets and ROI situations
Some of the listed topics above have not shown their practical relevance yet. There have been a number of discussions about 01005 rework capabilities, but up to now there is no proven evidence that those technologies that claim to be capable, can truly run successful rework processes on this tiny component in a daily real-world rework situation. Many parameters need to be observed and controlled in precision line-production, including:
• desoldering and lifting of component without affecting very close neighbouring components
• new selective solder paste supply for the small joints
• picking, adjustment and placement of the component
• PCB coating
• PCB cleaning and others
Nevertheless, as the 01005 components exist, the challenge is set. While the component size is shrinking and integration as well as the packing density are rising, on the other hand the PCB size is growing. Mainly driven by telecommunication and internet data transmission (cloud computing, IOT), the processing power of today’s computer centers is increasing rapidly. And in the same way parallel processing computer boards are growing in size. One challenge that remains is, how to homogeneously preheat a fully populated 24” x 48” multilayer PCB during rework?
Other topics like tracing and documenting the individual board treatment in the rework area seem to become a must in times of soaring electronic production and as repair processes have become an acknowledged part of electronic assembly. Out of the above mentioned topics, which basically describe a roadmap for rework capabilities until 2021, three subjects will be introduced subsequently. Other than issues that will be important for future repair and rework feasibility they have already reached practical necessity since a while ago and thus need to be fully implemented or improved in today’s rework systems.
Voidless Treatment During a Rework Process
In the assembly of bottom terminated components (BTC), the formation of voids has become a serious problem in many applications. A definition for a void is given in the context of soldering defects as:
[…] then solder will quickly fill the opening of the fitting, trapping some flux inside the joint. This bubble of trapped flux is the void;
[…] the joint, preventing solder from occupying that space. An area inside a soldered joint where solder is unable to completely fill the fittings‘ cup, because flux has become sealed inside.
And in SMT, only one of the possible effects is explained as:
[…] The reliability of solder joints becomes more of a concern, as less and less solder is allowed for each joint. Voiding is a fault commonly associated with solder joints, especially when reflowing a solder paste in the SMT application. The presence of voids can deteriorate the joint strength and eventually lead to joint failure.
The following impacts of void formation inside a solder joint have been reported:
• reduced thermal transfer from component to the PCB with risk of overheating the component
• reduced mechanical strength of a solder joint
• possibility of spontaneous out gassing—creation of solder splashes
• impact to the ampacity of a solder joint—connection may overheat because of higher electrical resistance
• impact on the signal transmission—in high frequency applications voids may dampen the signals
Especially in power electronics, the formation of voids in the thermal pad (e.g., QFN packages) is currently an increasing problem. The necessary transfer of energy from the component into the PCB for cooling purposes might be disabled. The components lifetime will be drastically reduced.
Besides other methods like using low-voiding solder pastes, optimizing the reflow profile and applying the correct amount of solder paste with optimized stencils, a void reduction treatment of the entire assembly while the solder is in its liquid phase is an option to choose.
Figure 1: Voidless treatment of a PCB with piezo actuator.
So the question is, how is it possible to implement a void treatment technology into an open environment of a rework machine? The vacuum technology known from reflow ovens is not an option. The technique used is based on a sinusoidal actuation of the PCB substrate (Figure 1). Primarily the PCB is stimulated by a longitudinal wave with an amplitude of less than 10 μm on the PCB level. During this sinusoidal actuation of the PCB in a defined frequency range, the self-resonances of this area are stimulated regardless of the PCB layout and population. When the PCB is in sweep motion, the component remains in its location and the voids, trapped in the boundary layer, the liquid solder, have the ability to escape.
By this method, void reduction during new component installation down to void rates of 2% is possible. Even a significant void reduction can be achieved during a second reflow on an existing assembly. As in the case of a voidless rework treatment, only a selected area of the PCB is heated up to reflow and only this section is treated with the actuation, with no negative side effects to the assembly can be expected.
To read the full version of this article, which appeared in the September 2017 issue of SMT Magazine, click here.
Suggested Items
SolderKing’s Successful Approach to Modern Soldering Needs
06/18/2025 | Nolan Johnson, I-Connect007Chris Ward, co-founder of the family-owned SolderKing, discusses his company's rapid growth and recent recognition with the King’s Award for Enterprise. Chris shares how SolderKing has achieved these award-winning levels of service in such a short timeframe. Their secret? Being flexible in a changing market, technical prowess, and strong customer support.
Preventing Surface Prep Defects and Ensuring Reliability
06/10/2025 | Marcy LaRont, PCB007 MagazineIn printed circuit board (PCB) fabrication, surface preparation is a critical process that ensures strong adhesion, reliable plating, and long-term product performance. Without proper surface treatment, manufacturers may encounter defects such as delamination, poor solder mask adhesion, and plating failures. This article examines key surface preparation techniques, common defects resulting from improper processes, and real-world case studies that illustrate best practices.
Breaking Silos with Intelligence: Connectivity of Component-level Data Across the SMT Line
06/09/2025 | Dr. Eyal Weiss, CybordAs the complexity and demands of electronics manufacturing continue to rise, the smart factory is no longer a distant vision; it has become a necessity. While machine connectivity and line-level data integration have gained traction in recent years, one of the most overlooked opportunities lies in the component itself. Specifically, in the data captured just milliseconds before a component is placed onto the PCB, which often goes unexamined and is permanently lost once reflow begins.
BEST Inc. Introduces StikNPeel Rework Stencil for Fast, Simple and Reliable Solder Paste Printing
06/02/2025 | BEST Inc.BEST Inc., a leader in electronic component rework services, training, and products is pleased to introduce StikNPeel™ rework stencils. This innovative product is designed for printing solder paste for placement of gull wing devices such as quad flat packs (QFPs) or bottom terminated components.
See TopLine’s Next Gen Braided Solder Column Technology at SPACE TECH EXPO 2025
05/28/2025 | TopLineAerospace and Defense applications in demanding environments have a solution now in TopLine’s Braided Solder Columns, which can withstand the rigors of deep space cold and cryogenic environments.