Domestic Supply Chain Shuffle: Increasing the Value of Local Content in Semiconductor Equipment
November 6, 2017 | SEMIEstimated reading time: 2 minutes
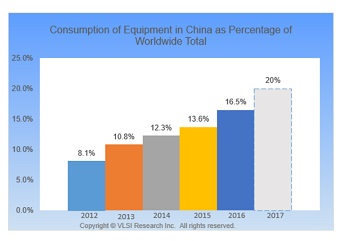
“Quality first, cost second.” This was the clear “take home” message for Chinese materials, subsystems and components suppliers attending an invitational event organised by ICMTIA in Ningbo on October 23. In the first meeting of its kind, almost 300 delegates from across the Chinese semiconductor equipment supply chain gathered to discuss the challenges and opportunities for Chinese suppliers to become innovators and leaders in global semiconductor manufacturing.
Over 20% of all semiconductor equipment will be shipped to China in 2017, yet Chinese OEMs account for only 2% of worldwide fab equipment. This percentage is even lower for Chinese subsystems and components suppliers. At the current rate of growth, China is soon expected to eclipse even Taiwan and Korea as the largest regional consumer of semiconductor equipment. The gap between Chinese equipment consumption and the value of locally supplied parts will continue to increase unless something changes.
Rapid growth in Chinese equipment consumption is set to continue, however, only a very small amount of equipment worldwide is actually supplied by Chinese OEMs.
The disparity between equipment consumption and production presents a clear opportunity for Chinese suppliers to increase their share of market within China. The question “Does it make sense to go head-to-head against the large U.S., European, and Japanese players or to take a softer approach by encouraging foreign suppliers to source more of their subcomponents and assembly services from Chinese suppliers?” The softer approach appears to be gaining favour as it carries lower risk of failure and allows Chinese suppliers to learn the quality processes required to develop advanced technology products and improve workforce skills and talent needed to compete at the cutting-edge of semiconductor chip manufacturing.
Foreign subsystems and components suppliers such as Advanced Energy, MKS and others have been manufacturing their products in China for many years proving that the infrastructure already exists to make high-quality subsystems. Foreign OEMS are now following their lead by actively seeking Chinese subcontract partners. Applied Materials is spearheading this move by making large investments and developing programs to help Chinese suppliers qualify. As a consequence, Chinese subcontract manufacturers are already learning and quickly developing their own IP
A significant portion of total global subsystems and components are manufactured in China demonstrating that it is already possible to manufacture high-quality products for semiconductor manufacturing in China.
In the short term, however, it is unlikely that a large Chinese OEM or subsystems supplier could rival the well-established incumbents – even with generous governmental policy and support. The significant barriers to entry are still present, including: large R&D costs; finding and retaining talented industry professionals and most importantly building the long-term trust and reputation with chip makers to displace the established equipment suppliers.
Nevertheless, with the backing of the Chinese government, semiconductor subsystems and component manufacturing in China is set to make a step change in strategy moving forwards. A major focus on improving quality and collaboration across the Chinese supply chain will both improve the reputation of Chinese suppliers and facilitate the development of innovative IP within China. Full domestication of the supply chain will in turn force foreign companies to increase the Chinese content of their equipment made in China. It is clear that China is organising to become one of the leading players of semiconductor manufacturing technology – the only question is “when,” not “if.”
Suggested Items
Hon Hai Education Foundation Continues to Promote Quantum Education
07/04/2025 | FoxconnHon Hai Education Foundation has long been committed to promoting forward-looking technology education in Taiwan's high schools, and held the "High School Quantum Teacher Training Camp" in Tainan City on July 1.
Incap UK Achieves JOSCAR Zero Accreditation
07/04/2025 | IncapIncap Electronics UK has been accredited under JOSCAR Zero, a new sustainability-focused extension of the defence and aerospace sector’s supplier assurance system.
Kitron Secures Contract for Components Supporting Unmanned Aerial Systems
07/04/2025 | KitronKitron has received a contract with an estimated value between EUR 4 and 8 million for the production and supply of advanced electronic components used in unmanned aerial systems (UAS).
NOTE Receives Order Worth 132 MSEK and Expands Collaboration with Customer within Security & Defense
07/04/2025 | NOTENOTE has received an order worth SEK 132 million from one of its existing customers operating within Security & Defense. NOTE thereby strengthens its long-term collaboration with the industry-leading customer.
Delta SEA Partner Event 2025 Unites Regional Partners to Embrace a “Future Ready” Vision
07/03/2025 | Delta ElectronicsDelta Electronics (Thailand) Public Company Limited, successfully hosted its Delta SEA Partner Event 2025: Future Ready at Delta Chungli Plant 5, Taiwan on June 10 – 11 , 2025.