-
- News
- Books
Featured Books
- pcb007 Magazine
Latest Issues
Current IssueThe Hole Truth: Via Integrity in an HDI World
From the drilled hole to registration across multiple sequential lamination cycles, to the quality of your copper plating, via reliability in an HDI world is becoming an ever-greater challenge. This month we look at “The Hole Truth,” from creating the “perfect” via to how you can assure via quality and reliability, the first time, every time.
In Pursuit of Perfection: Defect Reduction
For bare PCB board fabrication, defect reduction is a critical aspect of a company's bottom line profitability. In this issue, we examine how imaging, etching, and plating processes can provide information and insight into reducing defects and increasing yields.
Voices of the Industry
We take the pulse of the PCB industry by sharing insights from leading fabricators and suppliers in this month's issue. We've gathered their thoughts on the new U.S. administration, spending, the war in Ukraine, and their most pressing needs. It’s an eye-opening and enlightening look behind the curtain.
- Articles
- Columns
- Links
- Media kit
||| MENU - pcb007 Magazine
Cerambus Discusses the Next Generation in PCB Plating
July 12, 2018 | Stephen Las Marias, I-Connect007Estimated reading time: 11 minutes
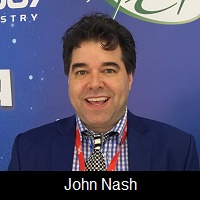
Cerambus Technology Inc. President John Nash sat down with I-Connect007 for a discussion on the latest developments in plating technology, challenges and opportunities in the China market, and their strategy for sustaining growth in a highly competitive industry.
Stephen Las Marias: John, please start by giving our readers an overview on Cerambus Technology.
John Nash: We’re a specialty chemical manufacturer focused on metal finishing. We were founded in San Jose, California, in 2002, and we moved into the China market shortly after that. We’ve been in China, including manufacturing there, for more than 10 years.
Las Marias: What are the trends that you’re seeing in this market, and in particular, PCB production?
Nash: More and more, the key word is miniaturization. There are more wearable devices today and medical technology—medical devices that go into the body. For example, we’re seeing cameras that sit on top of a PCB. Miniaturization is also present in automotive, and of course, personal electronics and smartphones. For instance, as cameras and other devices become smaller and smaller, PCBs are becoming much smaller, with more high-density interconnections.
Las Marias: What are the challenges there?
Nash: We’re seeing through-holes on the boards that are becoming increasingly smaller and harder to plate. We’re seeing more blind vias that either require half-filling, 3/4-filling, or full-filling—and that is a real challenge to do in conjunction with the through-holes that have been there forever. And the designers want those done at the same time. That’s a real challenge.
Las Marias: Where does Cerambus come in?
Nash: Well, the challenges have been wonderful; they’ve given us an opportunity to develop new plating chemistries that are well-suited for HDI and through-hole technology in this miniaturization. The through-hole is getting to be higher aspect ratio, which means that the hole size is becoming smaller relative to the thickness of the boards, and the high-density interconnectivity, like the blind vias for example, is becoming deeper and narrower, so the aspect ratio on those is becoming more difficult. We think we have the very best chemistry in the industry for plating these and for solving these kinds of challenges.
Las Marias: What makes your plating solutions unique in the market?
Nash: We get asked that a lot. From the early stages, we realized that plating chemistry for electronics originally came from the general metal finishing industry years ago, and they took those solutions and tried to make them work for electronics. Initially, there was no problem because the hole sizes were big, and the features were very big. We're talking about double-sided boards that have big holes and you could use those general metal finishing baths with very little tweaking to get them to work for electronics at that time. Also, the functional properties of the deposit didn’t need to meet the same industry specifications that are in effect today. We recognized even almost 20 years ago that the challenges were changing rapidly. At that time, we were looking at back panels and daughter cards for servers and the telecommunication industry, where we had aspect ratios that were greater than 20:1. Again, that's the diameter of the hole relative to the thickness of the panel.
We recognized the limitations to these general metal finishing formulas that were tweaked—by everybody. Of course, there were some additions made to those early plating baths that came into place, but really you could only tweak so far. We recognized this trend at a very early stage. So, we set out on a course to develop our own unique accelerators, leveling agents, wetting agents and other additives that would be better suited towards essentially what we have today—miniaturization.
Las Marias: Are you seeing an increase in the use of HDI in the industry?
Nash: Absolutely. That’s everywhere. This is the number one challenge, and I mentioned four different markets: automotive, medical technology, cellphone technology, and wearable devices. Across the board, we’re seeing this miniaturization that requires more HDI; absolutely, if I were to name all the challenges, I would say that the biggest one that we see is more HDI; it’s more than anything else right now.
Las Marias: How is Cerambus positioned to address the HDI issue?
Nash: Kind of taking a step back, there are probably three different types of plating challenges, maybe more. But we talk about high-aspect ratio plating; HDI plating, which would be some type of filling of these microvias; and then a third area, vertical continuous plating, or VCP plating. VCP entails a combination of through-hole plating—whether it be high-aspect ratio plating, HDI, or both together. VCP plating, without getting into the equipment too much, uses about half the amount of water, and hence, generates about half the amount of wastewater. Doing deeper blind vias, for example, more difficult HDI work, and through-hole plating, especially higher aspect ratio through hole plating, together, and then doing it with VCP plating, which saves water and labor, is a real challenge.
And everybody wants to take on these challenges now with VCP as opposed to hoist plating, which is a more traditional type of plating. And that is our forte. That's really our forte.
Las Marias: You've been in China for more than 10 years. What changes have you seen from your perspective as a chemical solutions provider?
Nash: We started even before we had the Wholly Foreign Owned Enterprise [WOFE] in China. We were in Hong Kong originally, and then we set up the WOFE in 2008. At that time, people talked about—and in fact we were one of the drivers of this—looking at how better throwing power would give you copper metal savings. It was simple in terms of the way people thought in terms of testing solutions; that’s one of the major things they looked at.
We have a whole line of PCB products—but plating is certainly the most challenging thing, I think. So, at that time, people would say, if it passes three solder floats, if it’s got good throwing power, it’s a good product. Today, there’s so many more categories that people look at, like having the balance, doing all the things at the same time, the same solution, and doing it quickly. That’s the other thing. Plating a decade ago was done at 18 to 20 ASF, which is current density, amps per square foot. Today, we’re plating in some cases over 40 ASF, and with insoluble anode technology we’re plating at 80 ASF or even higher.
People want to go faster, and I think this is being driven especially by our automotive customers and their customers, and the requirements that they have in terms of their testing are much more challenging than what we ever did before, in terms of the thermal cycling, the amount of thermal cycles, and the ramp times from the high temperature on the thermal cycling to the low temperature. So, very fast, in some cases, much faster than years ago. I think the IPC thermal cycling test was 100 cycles, and they were very slow ramps; they weren’t thermal shocking the board in the same way that they do today.
Today, it is 10 seconds, ramp up, ramp down, and higher and lower temperature extremes, and many more cycles. Forget the 100 cycles. We have some customers doing 2,000 cycles. Some customers in the LED industry are talking about going to 4,000 cycles. Our chemistry solutions are very unique, and well-suited to meet these new challenges. The grain structure of our deposit is very different, and it stretches, and it holds up to this kind of testing, a long and much more intense thermal cycling test.
It's been wonderful for us and I think we have a great future because of the challenges. And it takes up a lot of our time. I am not saying we’re out of commodity chemistries, but we don’t do as much as we used to because we’re so focused on these challenges. And obviously, they’re more lucrative than some of the other commodity chemistries that we used to do more of, like oxides, for example.
Page 1 of 2
Suggested Items
Knocking Down the Bone Pile: Addressing End-of-life Component Solderability Issues, Part 4
07/15/2025 | Nash Bell -- Column: Knocking Down the Bone PileIn 1983, the Department of Defense identified that over 40% of military electronic system failures in the field were electrical, with approximately 50% attributed to poor solder connections. Investigations revealed that plated finishes, typically nickel or tin, were porous and non-intermetallic.
SHENMAO Strengthens Semiconductor Capabilities with Acquisition of PMTC
07/10/2025 | SHENMAOSHENMAO America, Inc. has announced the acquisition of Profound Material Technology Co., Ltd. (PMTC), a premier Taiwan-based manufacturer of high-performance solder balls for semiconductor packaging.
KYZEN to Highlight Understencil and PCB Cleaners at SMTA Querétaro Expo and Tech Forum
07/09/2025 | KYZEN'KYZEN, the global leader in innovative environmentally responsible cleaning chemistries, will exhibit at the SMTA Querétaro Expo & Tech Forum, scheduled to take place Thursday, July 24, at Centro de Congresos y Teatro Metropolitano de Querétaro.
Driving Innovation: Direct Imaging vs. Conventional Exposure
07/01/2025 | Simon Khesin -- Column: Driving InnovationMy first camera used Kodak film. I even experimented with developing photos in the bathroom, though I usually dropped the film off at a Kodak center and received the prints two weeks later, only to discover that some images were out of focus or poorly framed. Today, every smartphone contains a high-quality camera capable of producing stunning images instantly.
Hands-On Demos Now Available for Apollo Seiko’s EF and AF Selective Soldering Lines
06/30/2025 | Apollo SeikoApollo Seiko, a leading innovator in soldering technology, is excited to spotlight its expanded lineup of EF and AF Series Selective Soldering Systems, now available for live demonstrations in its newly dedicated demo room.