-
- News
- Books
Featured Books
- smt007 Magazine
Latest Issues
Current IssueWhat's Your Sweet Spot?
Are you in a niche that’s growing or shrinking? Is it time to reassess and refocus? We spotlight companies thriving by redefining or reinforcing their niche. What are their insights?
Moving Forward With Confidence
In this issue, we focus on sales and quoting, workforce training, new IPC leadership in the U.S. and Canada, the effects of tariffs, CFX standards, and much more—all designed to provide perspective as you move through the cloud bank of today's shifting economic market.
Intelligent Test and Inspection
Are you ready to explore the cutting-edge advancements shaping the electronics manufacturing industry? The May 2025 issue of SMT007 Magazine is packed with insights, innovations, and expert perspectives that you won’t want to miss.
- Articles
- Columns
- Links
- Media kit
||| MENU - smt007 Magazine
Alpha's Revolutionary Approach to Low-Temp Soldering
August 7, 2018 | Patty Goldman, I-Connect007Estimated reading time: 5 minutes
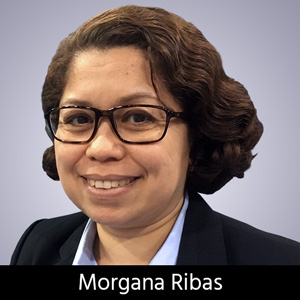
In this interview, Morgana Ribas discusses the new technology on low-temperature solder that she has developed at Alpha Assembly Solutions.
Patty Goldman: Morgana, before we get into the details of this new low-temp solder, please tell me a bit about yourself and your background at Alpha.
Morgana Ribas: I have been working for Alpha more than six years at our Research Centre located in Bangalore, India, where I manage our Metals Technology Group. I began my career in Brazil, and have lived in Japan and the United States before moving to India.
Goldman: Now to the good stuff: Alpha’s new low-temp solder product, HRL1. Tell me about that.
Ribas: We have developed low-temperature soldering using tin-bismuth alloys. Alpha has been working on this topic for several years and we have commercialized other Sn-Bi solder products before. However, we believe that our latest product, OM-550 HRL1 solder paste, will revolutionize the use of low temperature soldering.
It requires reflow temperatures below those used for Sn-Ag-Cu solder alloys. There are several drivers for using low temperature solders, including technical and economic advantages. For example, cost reduction can be achieved from lowering energy costs, increasing SMT yield margins and reducing material costs, for example by switching to cheaper substrates and packages.
Goldman: And that is because many solders need special substrates because they are so hot, correct?
Ribas: Yes, when the electronics industry moved on to Pb-free soldering, there was also a change in the materials used for substrates and packages due to the increased reflow temperatures required by Sn-Ag-Cu solders. We believe that low temperature soldering is potentially a new inflection point in the industry, considering the significant cost reduction from energy and materials savings when the peak reflow temperature is reduced below 200°C. Most importantly, they can fulfil an important technical requirement from the latest generation of ultra-thin microprocessors as reflow temperatures below 200°C considerable reduce dynamic warpage of flip chip ball grid arrays. And, by the reducing dynamic warpage there is also significant increase in SMT yields, when compared to SAC305.
Goldman: Is that unusual or common?
Ribas: Alpha has been offering low temperature eutectic Sn-Bi solder pastes for over a decade, such as CVP-520 42Sn-57.6Bi-0.4Ag. During this period, we have improved upon the mechanical shock reliability and printing performance of our solder pastes. More recently, we have been offering OM-535 SBX02, which is recommended for applications that require higher mechanical reliability than 42Sn-57.6Bi-0.4Ag, but still lower than alloys such as SAC305. However, with the widespread adoption of portable devices like cellphones, tablets, and laptops, which are very sensitive to drop and shock, there was a need for developing new solder alloys that would match SAC305 performance. That is why we have developed ALPHA OM-550 HRL1 solder paste, which is especially recommended for low temperature soldering of devices that require mechanical shock resistance similar to SAC305.
Goldman: I'm sure that requirement goes beyond some consumer products and spreads into things like automobile and military and everything else.
Ribas: Indeed, the iNEMI roadmap predicts that the use of low temperature solder paste will grow from the current less than 1% to 20% by 2027. This is probably the largest growth that the industry has seen for one type of soldering alloy since the switch to Pb-free solders.
Goldman: If it is low cost and it has better shock resistance, then everyone will want it, whether they need it or not, because they will want the best properties possible. I can see how that would grow.
Ribas: There is one additional requirement and that's the environmental requirement. In the Paris Agreement, several governments have committed to reduce greenhouse emissions and are therefore trying to push the corporations in each country to fulfill their corporate social responsibility by reducing greenhouse emissions. There are several ways of doing that, like finding ways to mitigate the negative impacts on the environment and reducing energy consumption that directly reduces greenhouse emissions.
By reducing the reflow temperature, we are going to have a considerable reduction in CO2 and more efficient use of materials, and that's why we are proposing using low-temperature soldering materials that can be more efficient and can considerably reduce the cost for the equipment manufacturers.
Goldman: What are the materials in this new solder?
Ribas: We are offering OM-550 HRL1 solder paste, which uses a proprietary alloy called HRL1. This alloy is basically a non-eutectic tin-bismuth, lead-free solder alloy with about 2% additives. We have found that this combination of Bi content and additives yield the right combination of melting behavior, mechanical properties, drop-shock performance, and thermal cycling performance.
Goldman: What, if any, are the downsides to it?
Ribas: The downside is that the electronics industry is constantly evolving and launching new designs of microprocessors. We believe low temperature soldering is here to stay, but technical requirements for soldering electronics packages tend to grow with fast miniaturization and increased complexity of these packages. Thus, in the future it is natural to expect that additional thermal and mechanical reliability requirements will drive the development of new soldering materials. That is why it is important for customers to associate themselves with soldering material suppliers like Alpha Assembly Solutions who have a long tradition of R&D and keeps researching new materials for the next generation of soldering requirements.
Goldman: Well, I don't see that as a downside. (Laughs)
Ribas: The downside side is that it can take a long time for developing such products, so we must continue working on it! (Laughs). But another downside is that tin-bismuth is a brittle material that has poor mechanical shock resistance. However, brittleness is what gives it strength, and strength is a desirable property, but it has to come with a certain minimum level of ductility. The elongation property of this solder can be improved and the brittleness decreased by reducing bismuth content. But reducing only the bismuth content is not enough to improve drop-shock performance of the solder joint. That is why we use alloying additions that close this gap and deliver the required performance.
Goldman: You have to get it just right.
Ribas: Yes. There is yet another point that is very interesting about using Sn-Bi low temperature solder paste; it can be used to assemble flip-chip ball grid arrays of Sn-Ag-Cu solder balls. For example, if SAC305 starts melting at 217°C, which is its solidus temperature, how could it form a bond with the Cu pads when it is reflowed at 195 –200oC? That is a very important question.
Alpha’s HRL1 solder alloy has a very high degree liquid phase even before it touches its liquidus temperature, and then it increases the inter-diffusion with the SAC during the reflow, maximizing the formation of this mixed area between the SAC and the low-temperature solder, and giving the desired strength.
When there is a soldering product that that can reduce manufacturing costs, keep the necessary reliability levels and contribute for the environment by reducing greenhouse emissions, I think it is just a win-win situation.
Goldman: That's certainly sounds like the right way to go. Morgana, thank you very much for your time.
Ribas: Thank you.
Suggested Items
Hands-On Demos Now Available for Apollo Seiko’s EF and AF Selective Soldering Lines
06/30/2025 | Apollo SeikoApollo Seiko, a leading innovator in soldering technology, is excited to spotlight its expanded lineup of EF and AF Series Selective Soldering Systems, now available for live demonstrations in its newly dedicated demo room.
SolderKing’s Successful Approach to Modern Soldering Needs
06/18/2025 | Nolan Johnson, I-Connect007Chris Ward, co-founder of the family-owned SolderKing, discusses his company's rapid growth and recent recognition with the King’s Award for Enterprise. Chris shares how SolderKing has achieved these award-winning levels of service in such a short timeframe. Their secret? Being flexible in a changing market, technical prowess, and strong customer support.
E-tronix Announces Upcoming Webinar with ELMOTEC: Optimizing Soldering Quality and Efficiency with Robotic Automation
05/30/2025 | E-tronixE-tronix, a Stromberg Company, is excited to host an informative webinar presented by Raphael Luchs, CEO of ELMOTEC, titled "Optimize Soldering Quality and Efficiency with Robotic Automation," taking place on Wednesday, June 4, 2025 at 12:00 PM CDT.
SMTA Releases Final Batch of Training Resources Donated by Bob Willis
05/29/2025 | SMTAThe Surface Mount Technology Association (SMTA) announces the release of several more webinars, poster sets, and photo libraries to conclude a generous donation from renowned industry expert Bob Willis.
Altus Supports Phoenix Systems in Advancing THT Assembly with Robotic Soldering
05/27/2025 | Altus GroupAltus Group, a leading distributor of capital equipment in the UK and Ireland, has successfully supported Phoenix Systems UK Ltd in its investment in robotic soldering technology to further enhance its through-hole technology (THT) assembly processes.