Best Practices to Achieve Zero Defects
August 14, 2018 | Stephanie Weaver, Zentech Manufacturing Inc.Estimated reading time: 2 minutes
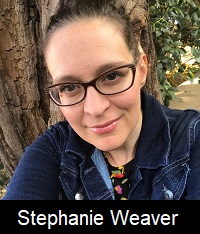
The following checks and balances ensure that a complex electronics build can be completed on time, on budget and with zero defects. Each practice in this process allows for adjustments or corrections to occur real time, instead of discovering them at the end of the build or worse, when it's already arrived at the end user.
1. New Product Introduction
To make your product a success, you need to ensure reliability and optimum functionality of the final product. If your company simply takes the data provided and immediately fabricates the product with no careful study of the data, materials or process, it will most likely result in faulty products and leaves you with unhappy customers. Careful review of the data before the manufacturing begins is extremely important.
2. Planning and Scheduling
The following planning and scheduling processes are essential:
- Assembly Instructions (AI): actual detailed instructions used to assemble the product. These are generated during the New Product Introduction process.
- Production Lot Traveler (PLT): This process is like a road map, containing the consecutive operations required to fabricate/assemble/inspect/test each item.
- Master Schedule: The process flow is outlined in the Master Schedule for each assembly. There should be a standard production flow from Kit Pull through End Item Delivery. Each item must be defined through company work instructions, standard operating procedures, and other command media.
3. Multiple Inspections, Testing and Reporting
Inspections and testing should be multiple and strategically placed throughout the manufacturing process. Inspections that should be considered:
- Incoming component inspections
- FAI – First Article Inspection
- AOI – Automated Optical Inspection
- 4D Flying Probe
- Other Testing such as ICT (In Circuit Test), functional and environmental testing
- During the assembly process, problems resulting from in process and final inspections must be recorded on Inspection Defect Reports. Production reports showing yield rates, types of defects, and number of defects should also be generated.
4. QMS
All quality functions should be controlled under a Quality Management System (QMS) which is certified to ISO 9001-2015, ISO 13485 or AS9100 Standards. These systems should also be audited by outside auditors two times each year to ensure that all manufacturing processes meet the latest ISO requirements.
5. Certifications and Compliance
Certifications demonstrate the commitment to excellence of a contract manufacturer. Certifications provide a level of (objective) accountability and ensure that the contract manufacturer remains compliant with current industry standards, regulations, and best-practices which directly impact the quality and reliability of the products and services that the electronics contract manufacturer provides. The following is a list of key certifications and compliance standards that allow your company to stand out from the others.
- NIST 800-171 compliance
- AS5553 Counterfeit Mitigation Compliant
- ITAR registered
- AS9100
- IPC-A-610 Qualified Manufacturers Listing
- IPC-J-STD-001 Space Addendum
- ISO 13485
- ISO 9001
Stephanie Weaver is a business development manager at Zentech Manufacturing. To read her article on the best practices in task order execution in contract manufacturing, which was published at the July 2018 issue of SMT007 Magazine, click here.
Suggested Items
IPC Hall of Fame Spotlight Series: Highlighting Lionel Fullwood
07/15/2025 | Dan Feinberg, I-Connect007Many IPC members who have contributed significantly to IPC and our industry have been awarded the IPC Raymond E. Pritchard Hall of Fame (HOF) Award. Though many early HOF members have passed away and are unknown to today’s IPC membership, their contributions still resonate. This special series on IPC Hall of Fame members provides a reminder of who was honored and why. As a bonus, for those who are still around, we get to find out what these talented individuals are up to today.
TRI Unveils New Platform for Diverse Board Sizes Search Submit
07/14/2025 | TRITest Research, Inc. (TRI), the leading test and inspection systems provider for the electronics manufacturing industry, proudly introduces a new size configuration for SPI and AOI Models.
Seeing a Future in Mexico
07/09/2025 | Michelle Te, I-Connect007The Global Electronics Association (formerly known as IPC) has been instrumental in fostering a partnership with Guanajuato, a state north of Mexico City with 12 industrial clusters and close to 150 companies involved in electronics. This past spring, Alejandro Hernández, the undersecretary for investment promotion in Guanajuato, attended IPC APEX EXPO 2025 at the invitation of IPC Mexico Director Lorena Villanueva, where he met with several companies to discuss the opportunities available in Mexico. He is inviting electronics-related companies seeking long-term investment in a centrally located area with access to highways, railways, and ports.
The Global Electronics Association Releases IPC-8911: First-Ever Conductive Yarn Standard for E-Textile Application
07/02/2025 | Global Electronics AssociationThe Global Electronics Association announces the release of IPC-8911, Requirements for Conductive Yarns for E-Textiles Applications. This first-of-its-kind global standard establishes a clear framework for classifying, designating, and qualifying conductive yarns—helping to address longstanding challenges in supply chain communication, product testing, and material selection within the growing e-textiles industry.
IPC-CFX, 2.0: How to Use the QPL Effectively
07/02/2025 | Chris Jorgensen, Global Electronics AssociationIn part one of this series, we discussed the new features in CFX Version 2.0 and their implications for improved inter-machine communication. But what about bringing this new functionality to the shop floor? The IPC-CFX-2591 QPL is a powerful technical resource for manufacturers seeking CFX-enabled equipment. The Qualified Product List (QPL) helps streamline equipment selection by listing models verified for CFX compliance through a robust third-party virtual qualification process.