-
- News
- Books
Featured Books
- pcb007 Magazine
Latest Issues
Current IssueVoices of the Industry
We take the pulse of the PCB industry by sharing insights from leading fabricators and suppliers in this month's issue. We've gathered their thoughts on the new U.S. administration, spending, the war in Ukraine, and their most pressing needs. It’s an eye-opening and enlightening look behind the curtain.
The Essential Guide to Surface Finishes
We go back to basics this month with a recount of a little history, and look forward to addressing the many challenges that high density, high frequency, adhesion, SI, and corrosion concerns for harsh environments bring to the fore. We compare and contrast surface finishes by type and application, take a hard look at the many iterations of gold plating, and address palladium as a surface finish.
It's Show Time!
In this month’s issue of PCB007 Magazine we reimagine the possibilities featuring stories all about IPC APEX EXPO 2025—covering what to look forward to, and what you don’t want to miss.
- Articles
- Columns
Search Console
- Links
- Media kit
||| MENU - pcb007 Magazine
Countering Solder Mask Residue Production Concerns
August 22, 2018 | Rick Nichols, Sandra Heinemann, et al.Estimated reading time: 3 minutes
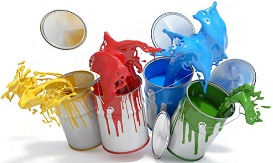
Abstract
The symbiotic relationship between solder masks and selective finishes is not new.
The solder mask application is one of the key considerations to ensure a successful application of a selective finish. The selective finish is the final chemical step of the PCB manufacturing process; this is when the panels are at their most valuable and are unfortunately not re-workable. Imperfections are not tolerated, even if they are wholly cosmetic. Quality issues often manifest themselves in the form of a ‘ping pong’ conversation between the fabricators, the solder mask suppliers and the selective finish suppliers. Without tangible evidence these discussions are difficult to resolve, and the selective finish process is usually regarded as responsible. Solder masks identified as ‘critical’ in the field have been tested using state-of-the-art technology to assess whether performance markers could be found. This article will focus on the chemical characteristics and use them to predict or identify potential issues before they occur rather than specifically name ‘critical’ solder masks. It is also the intention of this article to address the potential of a solder mask to react to common yield improvement practices such as UV bumping. It is hoped that this awareness will help fabricators to ensure maximum yields by asking the right questions.
Critical solder masks impacts all selective finishes. In this article, immersion tin will be used to highlight the relationship between critical solder masks and some of the issues seen in the field. The article will conclude with a novel approach to identify redeposited volatiles post reflow.
Background
The function of a solder mask is to provide protection to the active circuit and definition for the selective finish. These fundamental attributes include photosensitivity for lithographic imaging and sufficient production environment resistance to protect the active circuit. These functions are simple in principle, but the resultant implications can be far reaching. The impacts that will be focused on in this article will be surface imperfections and where relevant, immersion tin will be used as an example.
The hazards of a critical solder mask are primarily two-fold (excluding developing residues): Leach-out into process chemistries and solderability issues during multiple assembly steps.
Solder masks were originally designed to facilitate hot air solder leveling (HASL). The need for co-planarity has seen the introduction of chemical selective finishes such as ENIG, ENEPIG and immersion tin to name a few. This change in application has obvious implications attached. Whereas HASL is a hot solder shock for 10 seconds (approximately 260°C for eutectic solders and 280°C for lead-free solders), the wet chemical selective finishes introduce longer dwell times in harsh chemical environments, often at high temperatures. In an ideal world, the selection of the solder mask would be optimally coupled with the selective finish employed. In the real world, however, the cost factor is prevalent as a selection tool. To counter this notion, an attempt will be made in this article to raise awareness of the components within a solder mask that render it potentially ‘critical’ to production.
It is equally perplexing that in this day of high-tech six sigma process control, the quality of the solder mask process is still judged by weight gain, Stouffer wedges, breakpoint tests and the temperature of the baking ovens. Whilst all these controls ensure a good coating, they provide no information on the status of curing or the potential for volatile release during selective finish processing or assembly.
It must be stressed at this stage that solder masks fulfill a fundamental part of circuit manufacture and that, in the main, this is achieved very successfully. The virtual eradication of solder mask residues after developing is testament to the advancement in the imaging arena. For this article we will assume that resist residues have been totally eradicated and focus on the impact of leaching. Leaching of the solder mask into the chemistry has been shown to have lifetime and quality impacts. This is true of all the mainstream selective finishes.
This article will identify solder mask constituents that can be critical to production using state-of-the-art analysis equipment and demonstrate that traditional industry fixes such as UV bumping, if adopted, have little impact on eradicating the potential risks to yield. The solder masks selected as ‘critical’ are based on field experience.
To read the full version of this article which originally appeared in the July 2018 issue of PCB007 Magazine, click here.
Suggested Items
KYZEN Focuses on Aqueous Cleaning and Stencil Cleaning at SMTA Wisconsin
04/24/2025 | KYZEN'KYZEN, the global leader in innovative environmentally responsible cleaning chemistries, will exhibit at the SMTA Wisconsin Expo and Tech Forum, scheduled to take place Tuesday, May 6 at the Crowne Plaza Milwaukee Airport. KYZEN will be on-site to provide attendees with information about aqueous cleaning chemistry AQUANOX A4618 and stencil cleaner KYZEN E5631J.
SMTA Bridging the Skills Gap in Arizona
04/24/2025 | Marcy LaRont, I-Connect007One area where SMTA really excels is through its local chapters. On April 16, 2025, I-Connect007's Marcy LaRont attended the Workforce Breakfast during the SMTA Arizona Expo & Tech Forum in Mesa, which featured more than 50 electronics professionals from the local area, including defense OEMs, and others who were attending for the first time. Blackfox and Hyrel Technologies sponsored the event. The keynote presentation featured Sean Denny, a professor at Estrella Mountain Community College, who emphasized a clear need for skilled hand soldering technicians.
IPC Releases Version 2.0 of IPC-2591, Connected Factory Exchange, with Expanded Device Coverage and Smarter Data
04/23/2025 | IPCIPC announces the release of IPC-2591, Connected Factory Exchange (CFX), Version 2.0, the global standard for plug-and-play, machine-to-machine, and machine-to-system communication for digital manufacturing.
ViTrox Marks 25 Years of Innovation with Cutting-Edge Solutions at NEPCON China 2025 in Shanghai
04/18/2025 | ViTrox TechnologiesViTrox, which aims to be the World’s Most Trusted Technology Company, is proud to announce its participation in NEPCON China 2025, taking place from April 22–24, 2025, at Booth #1E45, Shanghai World Expo Exhibition & Convention Centre (SWEECC).
Indium Experts to Present on Power Electronics at PCIM Europe 2025
04/17/2025 | Indium CorporationAs one of the leading materials providers to the power electronics assembly and e-Mobility industries, Indium Corporation experts will share their technical insight and knowledge on a variety of industry-related topics throughout PCIM Europe, May 6-8, in Nuremberg, Germany.