Hardware and Software in Smart Factories
March 27, 2019 | Happy Holden, I-Connect007Estimated reading time: 2 minutes
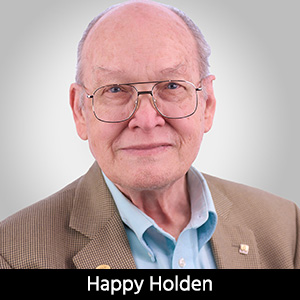
As smart factories become a part of the present rather than a thing of the future, we will all need to become familiar with related concepts and components. This article is dedicated to various automation protocols, including some new ones just coming on the market. The messages and recipe data needed for production scheduling to machine connections has evolved over the years. I will cover hardware, including programmable logic controllers (PLCs) and machine interfaces, as well as software and network protocols, such as MAPS™, SECS/GEM, OML, CFX, IPC-2541, and custom software.
Hardware
Industry 4.0 Initiatives
Industry 4.0 originates from a project in the high-tech strategy of the German government that provides for the computerization of manufacturing. The first industrial revolution mobilized the mechanization of production using water and steam power. The second industrial revolution introduced mass production with the help of electrical power, followed by the digital revolution and the use of electronics and IT to further automate production. Also, the term “Industrie 4.0” was first used at the Hannover Fair. In October 2012, the working group on Industry 4.0 chaired by Siegfried Dais and Henning Kagermann presented a set of Industry 4.0 implementation recommendations to the German federal government. On April 8, 2013, the final report of the working group on Industry 4.0 was presented.
PLCs
Today, there are multiple lights-out factory and Industry 4.0 initiatives. Much of this progress is the result of the automotive industry’s application of PLCs and robots to manufacturing. Figure 1 shows what the Germans foresaw for Industry 4.0 [1]. I was first introduced to PLCs by Allen-Bradley, as Hewlett-Packard (HP) had sold them its new CNC machines tool controller. PLCs became a major device in machine control (Figure 1).
PLCs are the most abundant smart controllers on the factory floor today. They come in all sizes, capabilities, and price ranges; some start at $60 USD. Many are hardened for harsh environments or outdoor use. Further, the flexibility of PLCs comes from the variety of units that can be plugged into them, such as conveyors, robots, PID process controllers, inspection, and test. Figure 2a shows an Ethernet group controller, and Figure 2b demonstrates a typical PLC and display monitor.
Software and Network Protocols
For factory automation software, HP developed CAD tools for PCB design and mechanical engineering that had data acquisition, SCADA, and test systems. The business computer division developed MRP and ERP software. In 1982, HP acquired Genesis Corporation, including IC-10 and six others, such as PC-10 and software products for factory control. HP had a complete software solution for factory automation connectivity that they developed for General Motors and the MAPSTM implementation. As this new software group was made into a division, they expanded their product line to include quality, test, and inspection systems; a CNC system; materials handling software; and an industrial process control system licensed from Mount Isa Mines. HP’s products were intended for typical factory automation networks typified by the four-level hierarchies seen in prior publications and by the ISA-95 standard. Application software can be much more complex, as shown with the seven-level ISO model.
To read the full article, which appeared in the March 2019 issue of PCB007 Magazine, click here.
Suggested Items
AI Helps Build Smarter, More Resilient Power Grids
05/16/2025 | BUSINESS WIREAs society’s reliance on electricity deepens, artificial intelligence (AI) is reshaping how we manage power grids and optimize energy sources.
Join the Conversation: MESI 4.0 Summit 2025
05/15/2025 | Critical ManufacturingThe MES and Industry 4.0 International Summit 2025 (MESI 4.0 Summit), hosted by Critical Manufacturing, will bring together manufacturing leaders, technology experts, and industry pioneers in Porto on June 12-13, offering a unique platform to explore practical strategies for digital transformation and smart manufacturing.
Roca Printed Circuits Joins Forces with Epec Engineered Technologies, NetVia
05/14/2025 | Epec Engineering TechnologiesRoca Printed Circuits and Epec Engineered Technologies announced today that Roca has joined forces with Epec’s NetVia Group PCB division in Dallas, expanding the combined organization's ability to deliver a broader range of high-quality printed circuit boards and electronic solutions.
Innovative Technology Advancements in Test: HATS² Technology and Its Impact on Reliability Testing
05/14/2025 | Barry Matties, I-Connect007Ensuring the reliability of printed circuit boards (PCBs) has become increasingly difficult and critical, yet the development of advanced testing methodologies is essential to meeting industry demands and addressing persistent challenges. One significant innovation is the High Acceleration Thermal Shock (HATS²) test system, which transforms how reliability testing is conducted. After 40 years in the testing business at Microtek, Bob Neves is beginning a new journey with his company, Reliability Assessment Solutions Inc. (RAS).
EWPTE 2025: Wire Processing Innovation Driving Technical Dialogue
05/13/2025 | Brittany Martin, I-Connect007From cutting-edge automation to advanced testing and harness assembly solutions, the 2025 Electrical Wire Processing Technology Expo (EWPTE) delivered a packed exhibit floor, robust technical programming, and valuable peer-to-peer connections.