Industrial 3D Printing Goes Skateboarding
April 11, 2019 | Michigan State UniversityEstimated reading time: 3 minutes
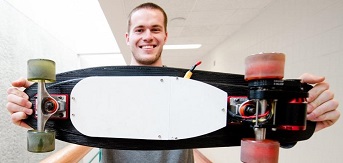
Kayak paddles, snowshoes, skateboards. Outdoor sporting goods used to be a tough market for 3D printing to break into, but fused particle fabrication (FPF) can change that.
A team led by engineers from Michigan Technological University and re:3D, Inc. developed and tested the Gigabot X, an open source industrial FPF 3D printer, which can use waste plastic particles and reform it into large, strong prints. Because of the unique challenges presented by sporting goods — size, durability, specificity — the team chose several Upper Peninsula-inspired items.
In their new paper, published in Additive Manufacturing the team lays out how fab labs, which are prototyping and technical workshops that allow personal digital fabrication, and other 3D printing hubs like makerspaces, public libraries or schools, can economically sustain themselves while printing environmentally friendly products using FPF. In some cases, the return on investment for a Gigabot X reached above 1,000% for high-capacity use paired with recyclable feedstock.
Recycle, Print, Repeat with Gigabot X
The Gigabot X is not the kind of 3D printer that fits on the kitchen table. Although these smaller printers also see a major return on investment for residential set-ups, the Michigan Tech Open Sustainability Technology (MOST) Lab saw a need beyond household prints.
“This isn’t a gadget to make toys for your kids; this is an industrial machine meant to make real, large, high-performance products. With well over 1,000 Fab Labs worldwide spreading fast and morphing into environmentally friendly ‘green fab labs’, the Gigabot X could be a useful tool to add to their services as well as other makerspaces,” said Joshua Pearce, Richard Witte Endowed Professor of Materials Science and Engineering and a professor in the Department of Electrical and Computer Engineering. “Of course, for our testing we wanted to use recycled plastic.”
That’s a hallmark of the Gigabot X — last year a Michigan Tech and re:3D collaborative study showed that it could be used with a wide range of plastics plucked from the waste stream to live on in a new productive life. The system is based on a previous design from the MOST Lab, the recyclebot, which makes waste plastic filament for 3D printers. Pearce’s team has looked deep into better ways to sort, sift and classify plastic to improve its 3D printability. Melting and extruding, however, does weaken plastic; it can withstand five cycles before it’s mechanically compromised. What’s new with the Gigabot X is a process called fused particle fabrication (FPF), or fused granular fabrication (FGF), that skips the step of making filament before 3D printing and saves one melt cycle. Basically, it prints directly from shredded waste. The Gigabot X’s size and versatility to use any material including waste is reflected in the machine’s economics.
Fab Lab Return on Investment
While not cheap by household standards — the Gigabot X runs around $18,500 — the upfront investment has greater potential return. The team used three case studies: a skateboard deck, double-bladed kayak paddle (both child-sized and adult-sized fitted on an aluminum pipe) and snowshoes.
Using their sporting goods prints, Pearce and his team compared costs of low-end and high-end options for commercially available products, prints with commercial filament, prints with commercial pellets and prints with recycled plastic. They ran these against four capacity scenarios: continuous printing, one new start per day, two new starts per day and printing once per week. The printed kayak paddle, which was the trickiest to produce and compare because of the metal pipe, was financially comparable to the least expensive off-the-shelf paddle. Skateboards and snowshoes were both easy to produce and significantly lower in cost than commercial products. FPF printing beat the economics of even the cheapest decks using commercial pellets and dropped in cost using waste plastic. Over their lifetime, if operated even only once a day, the Gigabot X could produce millions of dollars of sporting goods products.
“Once the capital costs are taken care of, which can often be less than a year, FPF or FGF machines have an enormous potential to make profit. Economically, they absolutely make sense,” said Pearce. “The bottom line is that Gigabot Xs pay for themselves under a reasonable load and provide double or triple digit returns on investment under most scenarios. Essentially, if you’re using it more than once a week, then you’re making money, easily.”
For green fab labs as well as the burgeoning makerspace scene around the world, the Gigabot X presents a customizable, open source, environmentally friendly and fun option to help sustain its 3D printing center.
Suggested Items
Electroninks Acquires Complete UTDots Advanced Materials Nanoinks Portfolio and IP
05/19/2025 | ElectroninksElectroninks, the leader in metal organic decomposition (MOD) inks for additive manufacturing and advanced semiconductor packaging, announced it has officially completed its full acquisition of UTDots products and IP into its portfolio, further expanding its offerings in digital printing for high-performance applications.
Happy’s Tech Talk #38: Novel Metallization for UHDI
05/07/2025 | Happy Holden -- Column: Happy’s Tech TalkI have been involved in high-density electronics substrates since 1970 when I joined Hewlett-Packard’s RF semiconductor group after college. Figure 1 shows the difference between trace/space lithography for substrates and silicon starting in 1970. My projects involved sapphire circuits for RF devices, but the figure displays the state of PCBs and integrated CMOS circuits and their packaging, not discreet RF devices. Even then, semiconductors were 50X higher density.
Real Time with... IPC APEX EXPO 2025: Emerging Trends in Design and Technology
04/16/2025 | Real Time with...IPC APEX EXPOAndy Shaughnessy speaks with IPC design instructor Kris Moyer to discuss emerging design trends. They cover UHDI technology, 3D printing, and optical data transmission, emphasizing the importance of a skilled workforce. The role of AI in design is highlighted, along with the need for understanding physics and mechanics as designs become more complex. The conversation concludes with a focus on enhancing math skills for better signal integrity.
Real Time with... IPC APEX EXPO 2025: Transition Automation Focusing on Security Coatings and Squeegee Technology
04/16/2025 | Real Time with...IPC APEX EXPOMark Curtin, President of Transition Automation, gives an update on recent innovations at his company. He highlights a record sales month and their new focus on security coatings to fight counterfeiting. Mark explains the engineering behind their durable squeegees, the importance of maintenance, and the value of considering overall costs over just price.
Elephantech: For a Greener Tomorrow
04/16/2025 | Marcy LaRont, PCB007 MagazineNobuhiko Okamoto is the global sales and marketing manager for Elephantech Inc., a Japanese startup with a vision to make electronics more sustainable. The company is developing a metal inkjet technology that can print directly on the substrate and then give it a copper thickness by plating. In this interview, he discusses this novel technology's environmental advantages, as well as its potential benefits for the PCB manufacturing and semiconductor packaging segments.