-
- News
- Books
Featured Books
- pcb007 Magazine
Latest Issues
Current IssueThe Hole Truth: Via Integrity in an HDI World
From the drilled hole to registration across multiple sequential lamination cycles, to the quality of your copper plating, via reliability in an HDI world is becoming an ever-greater challenge. This month we look at “The Hole Truth,” from creating the “perfect” via to how you can assure via quality and reliability, the first time, every time.
In Pursuit of Perfection: Defect Reduction
For bare PCB board fabrication, defect reduction is a critical aspect of a company's bottom line profitability. In this issue, we examine how imaging, etching, and plating processes can provide information and insight into reducing defects and increasing yields.
Voices of the Industry
We take the pulse of the PCB industry by sharing insights from leading fabricators and suppliers in this month's issue. We've gathered their thoughts on the new U.S. administration, spending, the war in Ukraine, and their most pressing needs. It’s an eye-opening and enlightening look behind the curtain.
- Articles
- Columns
- Links
- Media kit
||| MENU - pcb007 Magazine
Learning to Be More Flexible: Case Studies on Improving FPC Design
May 14, 2019 | Todd MacFadden, Bose CorporationEstimated reading time: 3 minutes
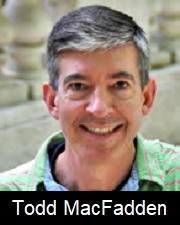
Like most kids, I spent my childhood dreaming that someday when I grew up I would get to optimize the design and manufacturability of flexible printed circuits. I envisioned the fantastical circuit outlines that would look like a squashed tarantula in 2D, but would origami intricately and elegantly into impossibly small 3D spaces. And, like other kids, I imagined the rigorous training I would receive in school and on the job to teach me exactly what materials to select and what parameters to use to achieve magnificent, robust bends that would (obviously) conform generously to IPC bend radius guidelines.
OK, not really. As a child, I dreamed of being a famous musician, until I learned more about the supply and demand curves for mediocrity. And, as many of us who have done this know, there is no formal training and often no right answer or perfect solution for FPC design. The IPC design standards—such as IPC-2223: Sectional Design Standard for Flexible/Rigid-Flexible Printed Circuits and IPC-6013: Qualification and Performance Specification for Flexible/Rigid-Flexible Printed Boards—provide indispensable guidance and are justifiably the go-to starting place. But the authors of these standards are careful to distinguish between requirements and guidelines, and they acknowledge that the standards cannot possibly encompass all use cases.
This is increasingly true as miniaturization requirements force us to pack more functionality into ever-smaller packages, and it becomes more difficult to conform to IPC construction recommendations. Achieving robust FPCs requires frequent, iterative interaction internally among the mechanical, electrical, and PCB design teams, as well as with the fabricators and assemblers. The sooner in the design cycle we can engage the supplier and assembler, the better.
This article will present three case studies of early prototype designs that didn’t go so well, and the lessons learned from each to highlight some of the challenges we faced and the steps we took to overcome them.
Note: no tarantulas were harmed during the writing of this article or in the design of any circuits.
1. Bend Radius Recommendations—You’re Joking, Right?
The bend radius recommendations from IPC-2223 (Table 1) provide a valiant starting place. But, increasingly, we are so far from these guidelines that design teams ask if we’re joking when we suggest them. It is now more common than not for us to exceed them, and over time, we have learned to accommodate much tighter bends than what IPC recommends. But there have been painful lessons along the way; these recommendations exist for a reason.
Figure 1 illustrates one particularly cringeworthy example. This is a 3-layer circuit (for simplicity, only Layer 2 is shown in the graphic) that is reduced to two layers in the bend regions. The conductors in the bend region were cracking at high rates during assembly. In hindsight, the design mistakes are glaring:
- The tight bend radii are uncontrolled: The two bends are respectively 1.0x and 1.5x the circuit thickness or about 10 times tighter than IPC guidelines. These are effectively creases. It is possible to crease 2-layer flexes, but the creasing operation must be well-controlled and only occur one time—creased circuits must never be reopened. Such care was not taken during this assembly process
Figure 1: Design renderings of a recent FPC failure due to cracked traces, including a 3D illustration of the tight bends (L), and a snapshot of the Layer 2 routing (R), showing some of the features that contributed to the failure.
- The bends begin right at the stiffened region: This is not recommended because it concentrates stress on the conductors. Ideally, there should be 0.5–1.0 mm of length after the stiffened region before a bend.
- Solder mask in the bend region: The solder mask (3) extends beyond the stiffener (1) and into the flex region to accommodate a trace on Layer 1 (not shown in this graphic). Solder mask should always be supported by a stiffener with at least a 0.2-mm overlap to accommodate registration tolerance of both solder mask image and stiffener location. While the solder mask formulations used by most FPC fabricators are referred to as “flexible,” they are not in fact designed to bend, particularly not this sharp. Having solder mask in the bend area increased circuit stiffness precisely where the bend began.
Fortunately, these failures occurred during an early prototype run, so there was time to respond. The circuit was redesigned to address each of these issues; no subsequent failures were encountered.
To read the full article, which appeared in the April 2019 issue of Flex007 Magazine, click here.
Suggested Items
Knocking Down the Bone Pile: Addressing End-of-life Component Solderability Issues, Part 4
07/15/2025 | Nash Bell -- Column: Knocking Down the Bone PileIn 1983, the Department of Defense identified that over 40% of military electronic system failures in the field were electrical, with approximately 50% attributed to poor solder connections. Investigations revealed that plated finishes, typically nickel or tin, were porous and non-intermetallic.
SHENMAO Strengthens Semiconductor Capabilities with Acquisition of PMTC
07/10/2025 | SHENMAOSHENMAO America, Inc. has announced the acquisition of Profound Material Technology Co., Ltd. (PMTC), a premier Taiwan-based manufacturer of high-performance solder balls for semiconductor packaging.
KYZEN to Highlight Understencil and PCB Cleaners at SMTA Querétaro Expo and Tech Forum
07/09/2025 | KYZEN'KYZEN, the global leader in innovative environmentally responsible cleaning chemistries, will exhibit at the SMTA Querétaro Expo & Tech Forum, scheduled to take place Thursday, July 24, at Centro de Congresos y Teatro Metropolitano de Querétaro.
Driving Innovation: Direct Imaging vs. Conventional Exposure
07/01/2025 | Simon Khesin -- Column: Driving InnovationMy first camera used Kodak film. I even experimented with developing photos in the bathroom, though I usually dropped the film off at a Kodak center and received the prints two weeks later, only to discover that some images were out of focus or poorly framed. Today, every smartphone contains a high-quality camera capable of producing stunning images instantly.
Hands-On Demos Now Available for Apollo Seiko’s EF and AF Selective Soldering Lines
06/30/2025 | Apollo SeikoApollo Seiko, a leading innovator in soldering technology, is excited to spotlight its expanded lineup of EF and AF Series Selective Soldering Systems, now available for live demonstrations in its newly dedicated demo room.