-
- News
- Books
Featured Books
- pcb007 Magazine
Latest Issues
Current IssueThe Hole Truth: Via Integrity in an HDI World
From the drilled hole to registration across multiple sequential lamination cycles, to the quality of your copper plating, via reliability in an HDI world is becoming an ever-greater challenge. This month we look at “The Hole Truth,” from creating the “perfect” via to how you can assure via quality and reliability, the first time, every time.
In Pursuit of Perfection: Defect Reduction
For bare PCB board fabrication, defect reduction is a critical aspect of a company's bottom line profitability. In this issue, we examine how imaging, etching, and plating processes can provide information and insight into reducing defects and increasing yields.
Voices of the Industry
We take the pulse of the PCB industry by sharing insights from leading fabricators and suppliers in this month's issue. We've gathered their thoughts on the new U.S. administration, spending, the war in Ukraine, and their most pressing needs. It’s an eye-opening and enlightening look behind the curtain.
- Articles
- Columns
- Links
- Media kit
||| MENU - pcb007 Magazine
Laminate Suppliers Face Increasing Demands From Customers
June 4, 2019 | Nolan Johnson, I-Connect007Estimated reading time: 4 minutes
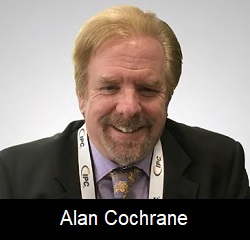
As a global laminate supplier with a large product offering, TUC is at the forefront of the growing customer demands that stem from a number of market segments pushing next-generation products. In an interview with Nolan Johnson, TUC North American President Alan Cochrane talks about the company’s shift toward trending areas—including HDI, halogen-free, and RF—and how strategies like the adoption of thinner glass styles have helped make it all possible.
Nolan Johnson: Alan, please give us some background on yourself and TUC.
Alan Cochrane: I’ve been with TUC for a little over eight years, and I’ve been in the industry since 1978. I started in research and development at TRW (now Northrop Grumman). I was on the fabricator side until 2010 when I joined TUC. We’ve seen a substantial amount of growth, including $425 million in 2016, $525 million in 2017, and $630 million in 2018.
TUC has been in business since ‘97, making copper-clad laminates. TUC started with mid- Tg materials and quickly moved up to high Tg as well as halogen-free products in the mid-loss range. Since the marketplace keeps having more and more needs, we moved into low-loss and super low-loss categories. We break things down into a few different market segments: high-speed digital and HDI applications in that marketplace. We also have product offerings for the RF and the millimeter-wave applications as well as a small segment that is the high-Dk specialty materials.
The biggest focus these days is mainly in the high-speed digital and RF areas. And there’s some crossover between the two of them. We have a product offering in the high-speed digital that’s for the 56-Gbps applications that are out there, which is pretty well entrenched. That’s the 12.5–14.5-GHz range that we’ve been servicing with a number of products. It’s an APPE-based product lineup with different fillers, etc. We’ve done a lot of interesting testing with large OEMs to meet their needs.
We are releasing a product soon called T4 for 25–28-GHz applications. The magic number, from an OEM standpoint, seems to be a 0.7dB loss per inch at 25 GHz with a 5-mil trace. So, as we get up into the 25–28-GHz applications, we have to look not just at our dielectric material but also at coppers that are starting to play a very big role in the overall loss of the product.
Johnson: What are some of the market dynamics that you’re currently seeing?
Cochrane: Almost six years ago, it used to be low Dk to try to get thinner. Everything is shrinking and there’s more miniaturization. Packages are getting smaller and smaller. To maintain that proverbial 50-ohm characteristic impedance or 100-ohm differential applications, we wanted thinner dielectrics with lower Dk so that we could maintain 50–100-ohm applications. However, we started getting into too low of a line width with resultant resistance to the overall losses, which became a major problem. Our focus for the last five years has been to look at lower loss for our high-speed digital customers.
Loss is the big driver followed by skew. The skew from trace to trace with differential pairs is determined a great deal by the glass weave that is utilized. What used to be a single-ply construction with a flat glass is evolving into multiple ply. The magic-ply count seems to be about a three-ply construction and to get into 5-mil dielectrics that we’re looking at for a 5-mil trace, that means we have to use a thinner glass.
Now, we’re crossing over to HDI. The 1027 glass—one and a half mils in overall thickness—used to be for laser applications for thin, stacked microvias. Today, we’re using a lot more of that in high-speed digital. Within the last two years, we’ve gone from the standard glass being a 1078, for example, to a 1035 and now down to a 1027. We’re getting thinner and thinner glasses to support that skew requirement as well as the loss requirements now even moving to 1017 and 1010 glass styles.
Johnson: Where do you see TUC’s current sweet spot in your product portfolio?
Cochrane: We have two main areas right now. We’ve gotten very close to the magic number of the 0.70 dB loss per inch at 25 GHz, which is for the next generation of chips that are out there for the 112-Gbps or 400-Gbps switch. That’s the lowest loss material that we have that is not in the PTFE range. We’re getting a lot of traction in that area because of that need.
We’re also seeing a resurgence of halogen-free. With the offering that we have in the halogen-free world, we still have a very low-loss material. We’re seeing a lot more utilization of the super low-loss, halogen-free materials. There may not be a corporate mandate to use halogen-free, but designers are finding that they can get the kind of performance out of a halogen-free that they couldn’t a number of years ago.
Johnson: Does the drive for the halogen-free seem to be customer demand?
Cochrane: Yes, in addition to their ability to have very low-loss and super low-loss materials. Then, we can easily get good performance in the 56-Gbps applications and the 14.5-GHz area. They’re being good corporate citizens. We see demand coming out of Europe, Canada, and North America as well.
To read the full article, which appeared in the May 2019 issue of PCB007 Magazine, click here.
Suggested Items
Copper Price Surge Raises Alarms for Electronics
07/15/2025 | Global Electronics Association Advocacy and Government Relations TeamThe copper market is experiencing major turbulence in the wake of U.S. President Donald Trump’s announcement of a 50% tariff on imported copper effective Aug. 1. Recent news reports, including from the New York Times, sent U.S. copper futures soaring to record highs, climbing nearly 13% in a single day as manufacturers braced for supply shocks and surging costs.
I-Connect007 Editor’s Choice: Five Must-Reads for the Week
07/11/2025 | Andy Shaughnessy, Design007 MagazineThis week, we have quite a variety of news items and articles for you. News continues to stream out of Washington, D.C., with tariffs rearing their controversial head again. Because these tariffs are targeted at overseas copper manufacturers, this news has a direct effect on our industry.I-Connect007 Editor’s Choice: Five Must-Reads for the Week
Digital Twin Concept in Copper Electroplating Process Performance
07/11/2025 | Aga Franczak, Robrecht Belis, Elsyca N.V.PCB manufacturing involves transforming a design into a physical board while meeting specific requirements. Understanding these design specifications is crucial, as they directly impact the PCB's fabrication process, performance, and yield rate. One key design specification is copper thieving—the addition of “dummy” pads across the surface that are plated along with the features designed on the outer layers. The purpose of the process is to provide a uniform distribution of copper across the outer layers to make the plating current density and plating in the holes more uniform.
Trump Copper Tariffs Spark Concern
07/10/2025 | I-Connect007 Editorial TeamPresident Donald Trump stated on July 8 that he plans to impose a 50% tariff on copper imports, sparking concern in a global industry whose output is critical to electric vehicles, military hardware, semiconductors, and a wide range of consumer goods. According to Yahoo Finance, copper futures climbed over 2% following tariff confirmation.
Happy’s Tech Talk #40: Factors in PTH Reliability—Hole Voids
07/09/2025 | Happy Holden -- Column: Happy’s Tech TalkWhen we consider via reliability, the major contributing factors are typically processing deviations. These can be subtle and not always visible. One particularly insightful column was by Mike Carano, “Causes of Plating Voids, Pre-electroless Copper,” where he outlined some of the possible causes of hole defects for both plated through-hole (PTH) and blind vias.