-
- News
- Books
Featured Books
- pcb007 Magazine
Latest Issues
Current IssueThe Hole Truth: Via Integrity in an HDI World
From the drilled hole to registration across multiple sequential lamination cycles, to the quality of your copper plating, via reliability in an HDI world is becoming an ever-greater challenge. This month we look at “The Hole Truth,” from creating the “perfect” via to how you can assure via quality and reliability, the first time, every time.
In Pursuit of Perfection: Defect Reduction
For bare PCB board fabrication, defect reduction is a critical aspect of a company's bottom line profitability. In this issue, we examine how imaging, etching, and plating processes can provide information and insight into reducing defects and increasing yields.
Voices of the Industry
We take the pulse of the PCB industry by sharing insights from leading fabricators and suppliers in this month's issue. We've gathered their thoughts on the new U.S. administration, spending, the war in Ukraine, and their most pressing needs. It’s an eye-opening and enlightening look behind the curtain.
- Articles
- Columns
- Links
- Media kit
||| MENU - pcb007 Magazine
PCB Fabricators’ Tech Capabilities Exceed OEMs’ Needs in Many Areas
June 6, 2019 | Dennis Fritz, Fritz ConsultingEstimated reading time: 1 minute
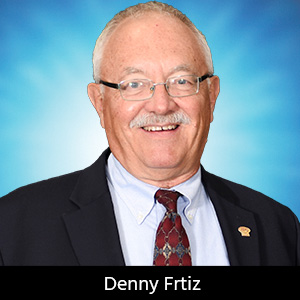
Some interesting differences showed up in the board property data reported by the OEMs and PCB fabricators that participated in IPC’s PCB Technology Trends 2018 study. By and large, those differences indicate that PCB fabricators are well positioned to meet many of their OEM customers’ technical needs today, and their projections indicate their belief that they can stay ahead of the curve through 2023.
One example is the average maximum number of drilled holes per panel. The participating PCB fabricators are drilling more than twice as many holes as the participating OEMs reported specifying.
PCB fabricators reported minimum conductor line widths and spaces that averaged 25−30% smaller than those currently specified by the participating OEMs. Perhaps more significantly, the participating PCB fabricators predict the minimum line width and spacing in five years will approach 50 microns, while the OEMs in the survey said line/space requirements would not even get as small as 90 microns.
Fabricators reported that they are building boards to mount finer surface mount features than the participating OEMs are specifying. Fabricators reported a minimum pitch of 0.5 millimeters on average for surface-mount packages, while the participating OEMs averaged current minimum pitch above 1.0 millimeter. Board fabricators estimate that by 2023, they will have to make boards to mount 0.3-millimeter pitch on average. OEMs were much less demanding in their expected 2023 specifications.
Differences in the samples of participating companies could explain these differences in part. The data might also reflect differences between the roles of the respondents. More than half the OEM respondents work in product development, design or R&D, while the PCB fabricator respondents represented a balanced mix of top management, production, design, quality assurance and engineering.
In many cases, OEM and PCB fabricators’ data averages were close, such as in board thickness, maximum number of layers, percentages of boards by layer count, rigid-flex layers, and the use of blind and buried vias. Both segments predict increases in the maximum number of layers and in the use of blind and buried vias over the next five years.
Do you think OEMs and board fabricators are singing from the same song-book?
Suggested Items
TRI Unveils New platform for Diverse Board Sizes Search Submit
07/14/2025 | TRITest Research, Inc. (TRI), the leading test and inspection systems provider for the electronics manufacturing industry, proudly introduces a new size configuration for SPI and AOI Models.
Seeing a Future in Mexico
07/09/2025 | Michelle Te, I-Connect007The Global Electronics Association (formerly known as IPC) has been instrumental in fostering a partnership with Guanajuato, a state north of Mexico City with 12 industrial clusters and close to 150 companies involved in electronics. This past spring, Alejandro Hernández, the undersecretary for investment promotion in Guanajuato, attended IPC APEX EXPO 2025 at the invitation of IPC Mexico Director Lorena Villanueva, where he met with several companies to discuss the opportunities available in Mexico. He is inviting electronics-related companies seeking long-term investment in a centrally located area with access to highways, railways, and ports.
The Global Electronics Association Releases IPC-8911: First-Ever Conductive Yarn Standard for E-Textile Application
07/02/2025 | Global Electronics AssociationThe Global Electronics Association announces the release of IPC-8911, Requirements for Conductive Yarns for E-Textiles Applications. This first-of-its-kind global standard establishes a clear framework for classifying, designating, and qualifying conductive yarns—helping to address longstanding challenges in supply chain communication, product testing, and material selection within the growing e-textiles industry.
IPC-CFX, 2.0: How to Use the QPL Effectively
07/02/2025 | Chris Jorgensen, Global Electronics AssociationIn part one of this series, we discussed the new features in CFX Version 2.0 and their implications for improved inter-machine communication. But what about bringing this new functionality to the shop floor? The IPC-CFX-2591 QPL is a powerful technical resource for manufacturers seeking CFX-enabled equipment. The Qualified Product List (QPL) helps streamline equipment selection by listing models verified for CFX compliance through a robust third-party virtual qualification process.
The Knowledge Base: A Conference for Cleaning and Coating of Mission-critical Electronics
07/08/2025 | Mike Konrad -- Column: The Knowledge BaseIn electronics manufacturing, there’s a dangerous misconception that cleaning and coating are standalone options, that they operate in different lanes, and that one can compensate for the other. Let’s clear that up now. Cleaning and conformal coating are not separate decisions. They are two chapters in the same story—the story of reliability.