-
- News
- Books
Featured Books
- smt007 Magazine
Latest Issues
Current IssueWhat's Your Sweet Spot?
Are you in a niche that’s growing or shrinking? Is it time to reassess and refocus? We spotlight companies thriving by redefining or reinforcing their niche. What are their insights?
Moving Forward With Confidence
In this issue, we focus on sales and quoting, workforce training, new IPC leadership in the U.S. and Canada, the effects of tariffs, CFX standards, and much more—all designed to provide perspective as you move through the cloud bank of today's shifting economic market.
Intelligent Test and Inspection
Are you ready to explore the cutting-edge advancements shaping the electronics manufacturing industry? The May 2025 issue of SMT007 Magazine is packed with insights, innovations, and expert perspectives that you won’t want to miss.
- Articles
- Columns
- Links
- Media kit
||| MENU - smt007 Magazine
Which Matters Most: Unit Cost or Total Cost of Supply?
August 9, 2019 | Neil Sharp, JJS ManufacturingEstimated reading time: 3 minutes
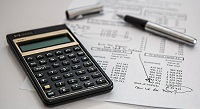
The primary objective for any original equipment manufacturer (OEM) is to design, manufacture, and deliver high-quality products in the most cost-effective way possible. When demand patterns change, or there is an increase in competition, it can be easy to rely on the calculation of unit cost to relieve the price pressure.
Achieving the lowest possible price is an important element of the negotiation process. But there is also the challenge of ensuring that any potential saving is going to be sustainable over the long-term—and that it doesn't come at the expense of the quality, service, or delivery of the end product.
The Over-reliance on Unit Cost
Calculating unit cost has long been the dominant price model when it comes to working out the cost of an electronics manufacturing project. Unit cost takes into account all of the “tangibles”—the fixed and variable costs, such as materials, labor, overheads, margins, etc.—and then divides this total by the number of units being produced. On the face of it, it’s a straightforward enough way for an OEM to identify their break-even point. But, as many manufacturers are discovering, choosing to base their outsourcing decisions purely on unit cost may not always reap the expected benefits in the long term.
Calculating the Total Cost of Supply
Considering the total cost of supply means taking into account all of the associated expenses that contribute to the creation of that item—from the ordering of raw materials through to the delivery to the end user. Establishing an accurate assessment of cost can often require looking beyond what’s immediately visible, and on being able to identify the indirect or less visible factors that can all contribute to the overall cost of the project. Calculating the total cost of supply is also about budgeting for the unknowns—being prepared for the fact that things don’t always go to plan, and that there may be additional inter-departmental expenses, such as travel, administration, extra supervisory time, etc.—that may not be directly visible, or accounted for, in the P&L.
The Maturing OEM/EMS Relationship
In more recent years, there has been a greater realization among U.K. electronics manufacturers of the relevance of total cost of supply rather than purely the calculation of unit cost. And according to the findings of the latest U.K. EMS Industry Report 2016–2022, published by Reed Electronics Research, many EMS providers are seeing that their own customers are becoming more receptive to the concept. A contributing factor in this shift of focus is believed to be down to the deepening relationship between OEMs and their EMS partners—and particularly as the role of EMS provider moves from one of purely sub-contract manufacturer to that of design and manufacturing expert.
Reaping the Benefits of Value-added Services
An experienced EMS partner is often best placed to offer an OEM a range of value-added services, such as problem-solving, assembly, packaging, kitting, warehousing, etc., that can all help reduce the time to market, improve productivity, and save the manufacturer money over the product’s lifetime. By choosing to involve their EMS provider much earlier on in the project, OEMs can also draw on their manufacturing partner’s extensive knowledge and experience when it comes to areas, such as board design, product functionality, testing efficiencies, or through-life product services.
As the U.K. EMS Industry report highlights, EMS are designing and manufacturing a diverse range of products and their level of expertise is constantly evolving and growing. By harnessing their EMS provider’s knowledge of new design protocols and manufacturing techniques and processes, OEMs can ensure they stay at the forefront of efficiencies in electronics assembly.
Neil Sharp is the director of marketing for JJS Manufacturing.
Suggested Items
NEPCON ASIA 2025: Innovating Smart Manufacturing Ecosystems and Bridging Global Opportunities
07/11/2025 | PRNewswireTaking place from October 28 to 30, 2025 at the Shenzhen World Exhibition & Convention Center (Bao'an), NEPCON ASIA is the premier platform to discover the latest technologies and market trends, connect with new suppliers and products, and explore potential partnerships and distribution opportunities.
Mycronic Delivers Strong Q2 Performance and Raises 2025 Outlook to SEK 7.5 Billion
07/11/2025 | MycronicMycronic reported a 35% increase in Q2 net sales and a 27% EBIT margin, prompting an upward revision of its full-year 2025 revenue forecast to SEK 7.5 billion.
Kitron Reports Strengthening Momentum in Q2 2025
07/10/2025 | KitronKitron reported solid quarterly sales and profits, particularly driven by the Defence & Aerospace market sector.
Seeing a Future in Mexico
07/09/2025 | Michelle Te, I-Connect007The Global Electronics Association (formerly known as IPC) has been instrumental in fostering a partnership with Guanajuato, a state north of Mexico City with 12 industrial clusters and close to 150 companies involved in electronics. This past spring, Alejandro Hernández, the undersecretary for investment promotion in Guanajuato, attended IPC APEX EXPO 2025 at the invitation of IPC Mexico Director Lorena Villanueva, where he met with several companies to discuss the opportunities available in Mexico. He is inviting electronics-related companies seeking long-term investment in a centrally located area with access to highways, railways, and ports.
Webinar Review: A Global Trade and Economy in Flux
07/09/2025 | I-Connect007 Editorial TeamIn a July 8 webinar, Global Electronics Association Chief Economist Shawn DuBravac provided a comprehensive analysis of the evolving international trade environment, its implications for inflation, monetary policy, and labor dynamics, and a sober assessment of market valuations. In “Navigating a Shifting Landscape” DuBravac painted a picture of a global economy in flux, where shifting trade alliances and tariff structures are redrawing the supply chain map and influencing the broader economic landscape, while also conveying an overall bullish market outlook.