-
- News
- Books
Featured Books
- smt007 Magazine
Latest Issues
Current IssueWhat's Your Sweet Spot?
Are you in a niche that’s growing or shrinking? Is it time to reassess and refocus? We spotlight companies thriving by redefining or reinforcing their niche. What are their insights?
Moving Forward With Confidence
In this issue, we focus on sales and quoting, workforce training, new IPC leadership in the U.S. and Canada, the effects of tariffs, CFX standards, and much more—all designed to provide perspective as you move through the cloud bank of today's shifting economic market.
Intelligent Test and Inspection
Are you ready to explore the cutting-edge advancements shaping the electronics manufacturing industry? The May 2025 issue of SMT007 Magazine is packed with insights, innovations, and expert perspectives that you won’t want to miss.
- Articles
- Columns
- Links
- Media kit
||| MENU - smt007 Magazine
Dispensing EMI Shielding Materials: An Alternative to Sputtering
August 23, 2019 | Garrett Wong, Nordson Asymtek and Jinu Choi, Henkel Electronic Materials LlcEstimated reading time: 5 minutes
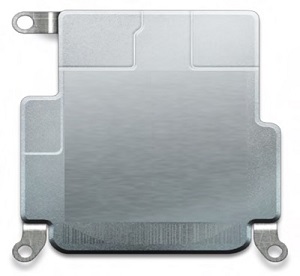
Abstract
Shielding electronic systems against electromagnetic interference (EMI) has become a hot topic. Technological advancements toward 5G standards, wireless charging of mobile electronics, in-package antenna integration, and system-in-package (SiP) adoption are driving the need to apply more effective EMI shielding and isolation to component packages and larger modules. For conformal shielding, EMI shielding materials for exterior package surfaces have mostly been applied with a physical vapor deposition (PVD) process of sputtering, leveraging front-end packaging technologies to back-end packaging applications. However, sputtering technology challenges in scalability and cost along with advancements in dispensable materials are driving considerations for alternative dispensing techniques for EMI shielding.
The authors will discuss the development of a spray coating process to apply EMI shielding materials to the exterior surfaces of individual components on strips and larger SiP packages. Using newly developed and enhanced materials and equipment for this industry, a process was demonstrated that provided uniform coating on packages in the sub-10-μm thickness range with consistent coating thicknesses around package corners and package sidewalls, producing a top surface-to-sidewall thickness ratio of 1:1. Further investigation showed decreased production costs for applying EMI shielding to component packages by increasing spray-coating productivity and by selectively applying the coating to specific areas of packages. Additionally, low capital-equipment expense and shorter lead times for spray coating equipment improved the ability to scale up production capacity compared to sputtering equipment.
In mobile electronics packaging, several SiP-module manufacturers are challenged to isolate components within the SiP from each other and from their exterior for EMI shielding. Trenches are cut around the interior components and conductive paste is dispensed into the trenches to form smaller Faraday cages within the package. As trench designs become narrower, it’s imperative to control both the volume and placement accuracy of the material filling the trenches. The latest, advanced jetting products provide control of the volume while the narrow, in-air stream width delivers accurate trench fill. In a final step, the tops of these paste-filled trenches are connected by applying exterior EMI shield coating. Spraying overcomes challenges faced when using sputtering equipment and harnesses the improvements in both the EMI shielding materials and the equipment for depositing it so that SiP packages can be manufactured using efficient back-end packaging techniques.
Introduction: Growth of EMI Shielding
EMI shielding has become a topic of significant interest in recent years. As 5G wireless technology is approaching mass-market acceptance and the future capabilities 5G standards will enable for the internet of things (IoT) and mission-critical communications, there is a significantly increasing need to effectively shield electronics and components from EMI. With the upcoming 5G wireless standards, signal frequencies of 600 MHz to 6 GHz and mmWave bands will become increasingly more common and powerful as the technology is adopted. Some of the proposed uses and implementations include window panels for office buildings or public transportation to help deal with shorter range communications.
Figure 1: Example SiP unit with sputter coating and integrated EMI shielding structures.
Other proposed implementations include home and office building repeaters to provide adequate coverage due to 5G frequencies having difficulties passing through walls and other solid objects. All of this activity will lead to an increased prevalence of signals in the 5G frequency range and a higher risk of exposure to EMI in these frequency ranges and their harmonics.
Fortunately, EMI can be shielded on component and system-in-package (SiP) devices through the application of thin coatings of conductive metal to the exteriors of such devices (Figure 1). Historically, EMI shielding has been applied through placing stamped metal cans around groups of components or by applying EMI shielding tapes to specific components. However, as packages and end devices continue to become miniaturized, such shielding methods become prohibitive due to size constraints as well as the flexibility to handle diverse, non-orthogonal packaging concepts that are becoming more common in mobile and wearable electronics.
Likewise, some leading-edge package designs are moving toward selective coating of only certain areas of a package for the EMI shielding rather than a complete shell over the full exterior of the package. In addition to the external coating for the EMI shielding, new SiP devices are further requiring additional integrated shielding to be built directly into the package to properly isolate individual components from each other in a single package.
Sputtering: A Method of Applying EMI Shielding
The predominant method for creating EMI shielding on molded component packages or molded SiP devices has been through sputtering multiple layers of metals over the surface. With sputtering, it has been possible to apply very thin, consistent coatings of pure metal or metal alloys to package surfaces in the 1-7μm thickness range. With the nature of the sputtering process capable of depositing metals at the angstrom level, the electrical performance of its coating layer has been effective thus far for typical shielding application.
However, as the need for shielding grows, sputtering has significant inherent drawbacks for it to be established as a scalable method for manufacturers and designers. Initial capital equipment costs for sputtering equipment are very high-in the million-dollar range. Sputter equipment lines require significant floor space due to its multi-chamber process, and further increases the need for additional real estate with full in-line conveyorized systems. With the inciting of plasma to sputter material from a sputter target to the substrate, typical sputter chamber environments could reach into the 400°C range; therefore, cooling of a substrate with a “cold plate” mounting fixture to reduce the experienced temperatures is needed. The sputtering process deposits metal on a given substrate but typically only produces up to 60% thickness coverage on the vertical sidewalls of a three-dimensional package compared to the thickness of the top surface layer.
Lastly, due to the nature of sputtering being a line-of-sight deposition process, metal particles cannot be selectively applied or necessarily applied under overhanging structures and topology and can result in significant material wastage in addition to material accumulation inside of the chamber walls; hence, this requires intensive maintenance. It is also necessary to pre-apply masking to substrates if there are specific areas of a given substrate that must remain exposed or do not require EMI shielding.
To read the full article, which appeared in the August 2019 issue of SMT007 Magazine, click here.
Suggested Items
IPC-CFX, 2.0: How to Use the QPL Effectively
07/02/2025 | Chris Jorgensen, Global Electronics AssociationIn part one of this series, we discussed the new features in CFX Version 2.0 and their implications for improved inter-machine communication. But what about bringing this new functionality to the shop floor? The IPC-CFX-2591 QPL is a powerful technical resource for manufacturers seeking CFX-enabled equipment. The Qualified Product List (QPL) helps streamline equipment selection by listing models verified for CFX compliance through a robust third-party virtual qualification process.
Technica USA Announces New Strategic Partnership with I.T.C. Intercircuit Production GmbH
06/24/2025 | Technica USATechnica USA is pleased to announce a new distribution and representative agreement with I.T.C. Intercircuit Production GmbH, a globally recognized manufacturer of advanced equipment for the PCB manufacturing industry.
Smart Automation: The Power of Data Integration in Electronics Manufacturing
06/24/2025 | Josh Casper -- Column: Smart AutomationAs EMS companies adopt automation, machine data collection and integration are among the biggest challenges. It’s now commonplace for equipment to collect and output vast amounts of data, sometimes more than a manufacturer knows what to do with. While many OEM equipment vendors offer full-line solutions, most EMS companies still take a vendor-agnostic approach, selecting the equipment companies that best serve their needs rather than a single-vendor solution.
Mesa West, Advanced West Announce Strategic Partnership
06/15/2025 | I-Connect007Mesa West is proud to announce that they have officially joined forces with Advanced West. This strategic partnership brings together two industry leaders, uniting strengths to better serve customers through enhanced capabilities, expanded offerings, and continued commitment to quality.
Evolve Manufacturing Celebrates 100 Years of Combined Leadership in Medical Device Manufacturing
05/26/2025 | Evolve ManufacturingEvolve Manufacturing Inc., a leading provider of end-to-end contract manufacturing services for medical device and life sciences instrument companies, proudly celebrates 100 years of combined medical device leadership among its expert team.