-
-
News
News Highlights
- Books
Featured Books
- pcb007 Magazine
Latest Issues
Current IssueThe Hole Truth: Via Integrity in an HDI World
From the drilled hole to registration across multiple sequential lamination cycles, to the quality of your copper plating, via reliability in an HDI world is becoming an ever-greater challenge. This month we look at “The Hole Truth,” from creating the “perfect” via to how you can assure via quality and reliability, the first time, every time.
In Pursuit of Perfection: Defect Reduction
For bare PCB board fabrication, defect reduction is a critical aspect of a company's bottom line profitability. In this issue, we examine how imaging, etching, and plating processes can provide information and insight into reducing defects and increasing yields.
Voices of the Industry
We take the pulse of the PCB industry by sharing insights from leading fabricators and suppliers in this month's issue. We've gathered their thoughts on the new U.S. administration, spending, the war in Ukraine, and their most pressing needs. It’s an eye-opening and enlightening look behind the curtain.
- Articles
- Columns
- Links
- Media kit
||| MENU - pcb007 Magazine
Vertical Conductive Structures, Part 3: Design Tool Techniques
August 23, 2019 | Ed Hickey and Mike Catrambone, Cadence Design Systems, and Joan Tourné, Nextgin TechnologyEstimated reading time: 3 minutes
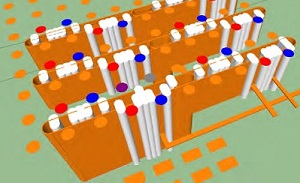
Editor’s Note: This article is part three of a series on vertical conductive structures. Click here to read Part 1 and Part 2.
As design complexity and density increases, it sometimes requires the designer to leverage different via technologies to successfully route into larger pin count devices while maintaining the highest level of signal integrity. Using through-hole vias can take up a lot of valuable board space; moving to smaller blind vias reduces the via size but will require larger buried vias to complete the connections deeper in the board. Another costly alternative is using every layer interconnect (ELIC) technology with each layer pair having its own copper-filled, laser-drilled microvias. Stacking these microvias on top of each other between layer pairs can extend the connection between any two layers in the board. These via technologies may successfully route the design but could cause the layer count to rise, and if not done correctly, could lead to signal integrity issues.
New vertical conductive structure (VeCS) technology can reduce layer count and improve signal integrity without the need for sequential technologies. VeCS is different than traditional through-hole vias, microvias, and ELIC designs, which are more expensive and require a high number of laminations, drilling, and plating cycles to build up a reasonable number of layers. Using VeCS combines routing channels for better utilization of the channel, escaping out large pin count devices. The larger routing channels allow more routes to escape with a more reliable/solid plane reference without the swiss-cheese effect normally seen with other via technologies.
In Allegro 17.2, VeCS structures are nothing more than a mechanical symbol that can be free-placed or placed inside of a ball grid array (BGA) field to take advantage of this new routing escape technology. No major changes were required to support these new structures in Allegro PCB Designer except for a manufacturing output update to generate limited depth (blind) drill files for pins in support of VeCS-2 blind depth structures. 17.2 Padstack Editor supports by-layer keepouts as well as adjacent layer keepouts to ensure manufacturability when these structures are used in a layout. These structures are created as library objects, so they can be easily leveraged across many designs for commonly used device escapes. If a structure requires a change, it can be made in one place with all instances refreshed in the layout.
VeCS
At the moment, we distinguish two “slot” technologies: VeCS-1, where the slots go through the board, and VeCS-2, where we do multi-level blind slots (Figure 1).
Figure 1: The front slot on the left side shows a VeCS-1, and the right shows VeCS-2.
In practice, we will see more hybrid constructions of VeCS-1 and VeCS-2 in one slot. The advantage is that we can connect GND and powers to multiple layers using VeCS-1, and the adjacent signal only connects to layer 4, for example. The VeCS-2 part of the slot creates a stubbles connection, minimizing capacitance and the dispersion of a higher speed signal.
At the moment, NextGIn Technology is very much focused on next-generation products, such as very high bandwidth applications where signal transitions between layers can be tuned such that the impedance of the vertical trace matches the impedance of the signal layer as it transits from one layer and connects to next. This enables layer transitions with minimum loss, enabling more efficient use of routing real estate compared to the ineffective and costly point-to-point routing used today using traditional via technology.
VeCS can be combined with through-hole, buried/blind vias, and microvia/HDI technology. There is no limitation. For example, a VeCS core/multilayer can be sandwiched between a set of microvias on top and bottom.
The process flow used right now is as follows:
1. Build board per standard flow.
2. Form slots (optional at mechanical drill stage): VeCS-1 and VeCS-2 from front and back.
3. Complete plating (standard).
4. Fill slots and holes (optional).
5. Form second route and bottom route.
6. Fill slots (second route).
7. Drill through-holes (optional).
8. Complete surface plating similar to a plated over-filled via (POFV).
9. Finish the panel as standard.
To read the full article, which appeared in the August 2019 issue of PCB007 Magazine, click here.
Suggested Items
The Evolution of Picosecond Laser Drilling
06/19/2025 | Marcy LaRont, PCB007 MagazineIs it hard to imagine a single laser pulse reduced not only from nanoseconds to picoseconds in its pulse duration, but even to femtoseconds? Well, buckle up because it seems we are there. In this interview, Dr. Stefan Rung, technical director of laser machines at Schmoll Maschinen GmbH, traces the technology trajectory of the laser drill from the CO2 laser to cutting-edge picosecond and hybrid laser drilling systems, highlighting the benefits and limitations of each method, and demonstrating how laser innovations are shaping the future of PCB fabrication.
Day 2: More Cutting-edge Insights at the EIPC Summer Conference
06/18/2025 | Pete Starkey, I-Connect007The European Institute for the PCB Community (EIPC) summer conference took place this year in Edinburgh, Scotland, June 3-4. This is the third of three articles on the conference. The other two cover Day 1’s sessions and the opening keynote speech. Below is a recap of the second day’s sessions.
Day 1: Cutting Edge Insights at the EIPC Summer Conference
06/17/2025 | Pete Starkey, I-Connect007The European Institute for the PCB Community (EIPC) Summer Conference took place this year in Edinburgh, Scotland, June 3-4. This is the second of three articles on the conference. The other two cover the keynote speeches and Day 2 of the technical conference. Below is a recap of the first day’s sessions.
Preventing Surface Prep Defects and Ensuring Reliability
06/10/2025 | Marcy LaRont, PCB007 MagazineIn printed circuit board (PCB) fabrication, surface preparation is a critical process that ensures strong adhesion, reliable plating, and long-term product performance. Without proper surface treatment, manufacturers may encounter defects such as delamination, poor solder mask adhesion, and plating failures. This article examines key surface preparation techniques, common defects resulting from improper processes, and real-world case studies that illustrate best practices.
RF PCB Design Tips and Tricks
05/08/2025 | Cherie Litson, EPTAC MIT CID/CID+There are many great books, videos, and information online about designing PCBs for RF circuits. A few of my favorite RF sources are Hans Rosenberg, Stephen Chavez, and Rick Hartley, but there are many more. These PCB design engineers have a very good perspective on what it takes to take an RF design from schematic concept to PCB layout.