Universal Robots Launches the World’s First Autonomous Bin Picking Kit for Machine Tending Applications
April 10, 2020 | Business WireEstimated reading time: 3 minutes
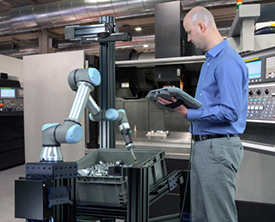
The complexity of automated bin picking is well-known throughout the industry, requiring huge efforts in both integration and programming. Today, most bin picking products are solely focused on the vision aspect of bin picking and often require hundreds of lines of additional programming to bridge the gap from “pick” to “place”—especially if the “place” is not just dropping into a box or tote but accurately inserting the part into a fixture for further processing. ActiNav Autonomous Bin Picking changes all that, allowing manufacturers with limited or no bin picking deployment expertise to quickly achieve high machine uptime and accurate part placement with few operator interventions.“Machine tending has always been one of the mainstay applications for our collaborative robot arms”
ActiNav combines real-time autonomous motion control, collaborative robotics, vision and sensor systems in one easy to use, fast to deploy and cost-effective kit. The system requires no vision or robotic programming expertise, but is instead based on a “teach-by-demonstration” principle using a six-step, wizard-guided setup process integrated into the UR cobot teach pendant. ActiNav can be easily and quickly deployed by manufacturers’ in-house automation teams or through assistance from a UR distributor or integrator to deliver increased productivity, quality and efficiency.
“Machine tending has always been one of the mainstay applications for our collaborative robot arms,” says VP of Product and Applications Management at Universal Robots, Jim Lawton. “We discovered a significant market need for a simple solution that enables UR cobots to autonomously locate and pick parts out of deep bins and place them precisely into a machine. This is not pick and drop; this is accurate pick and part-oriented placement.”
ActiNav is available through UR’s distribution channel and via the new UR+ Application Kits platform, an expansion of the cobot pioneer’s successful UR+ ecosystem of components certified to work seamlessly with UR cobots. Like other UR+ application kits, ActiNav is developed with in-depth application knowledge that eliminates the duplication of engineering efforts when deploying widely used applications. ActiNav works with UR’s UR5e and UR10e e-Series cobots, a UR+ component or user-defined end effector, and application-specific frame or fixture as needed. The kit includes the Autonomous Motion Module (AMM) and ActiNav URCap user interface software, along with a choice of 3D sensors.
While there is a variety of approaches to automating machine tending stations, many of which include implementing trays, bowl feeders or conveyors to get the parts to the machine, Lawton explains how ActiNav bypasses this step. “Parts are often already in bins, so the most flexible and scalable option is to deliver that bin of parts to the machine and then pick them directly from the bin and place them into the machine,” he says. “This minimizes floor space and reduces the need for part-specific tooling.”
ActiNav autonomously inserts parts into CNC or processing machines such as drilling, deburring, welding, trimming or tapping. The high-resolution 3D sensor and CAD matching enables high-accuracy picks powered by ActiNav’s Autonomous Motion Module (AMM) that determines how to pick the part, then controls the robot to pick the part and place it in a fixture each time. The autonomous motion control enables ActiNav to operate inside deep bins that hold more parts; something that standalone bin picking vision systems struggle to accomplish.
IDC’s Research Director covering robotics, Remy Glaisner, is closely following the market for automated machine tending solutions. “Today more than ever, technology users are looking to preserve the integrity and continuity of business operations,” he says. “In that context, simplifying the integration or redeployment of highly flexible robotic systems becomes a critical capability for manufacturers and other industrial users. In many ways, ActiNav will set a new level of operational expectations regarding the future of intelligent systems.”
Suggested Items
Excellon Installs COBRA Hybrid Laser at Innovative Circuits
06/23/2025 | ExcellonExcellon is pleased to announce the successful installation of a second COBRA Hybrid Laser System at Innovative Circuits, located in Alpharetta, Georgia. The Excellon COBRA Hybrid Laser System uniquely combines both UV and CO₂ (IR) laser sources on a single platform—making it ideal for high-density prototype and production printed circuit boards (PCBs).
Gorilla Circuits Elevates PCB Precision with Schmoll’s Optiflex II Alignment System
06/23/2025 | Schmoll MaschinenGorilla Circuits, a leading PCB manufacturer based in Silicon Valley, has enhanced its production capabilities with the addition of Schmoll Maschinen’s Optiflex II Post-Etch Punch system—bringing a new level of precision to multilayer board fabrication.
The Evolution of Picosecond Laser Drilling
06/19/2025 | Marcy LaRont, PCB007 MagazineIs it hard to imagine a single laser pulse reduced not only from nanoseconds to picoseconds in its pulse duration, but even to femtoseconds? Well, buckle up because it seems we are there. In this interview, Dr. Stefan Rung, technical director of laser machines at Schmoll Maschinen GmbH, traces the technology trajectory of the laser drill from the CO2 laser to cutting-edge picosecond and hybrid laser drilling systems, highlighting the benefits and limitations of each method, and demonstrating how laser innovations are shaping the future of PCB fabrication.
Sierra Circuits Boosts High Precision PCB Manufacturing with Schmoll Technology
06/16/2025 | Schmoll MaschinenSierra Circuits has seen increased success in production of multilayer HDI boards and high-speed signal architectures through the integration of a range of Schmoll Maschinen systems. The company’s current setup includes four MXY-6 drilling machines, two LM2 routing models, and a semi-automatic Optiflex II innerlayer punch.
Driving Innovation: Traceability in PCB Production
05/29/2025 | Kurt Palmer -- Column: Driving InnovationTraceability across the entire printed circuit board production process is an increasingly important topic among established manufacturers and companies considering new PCB facilities. The reasons are apparent: Automatic loading of part programs, connection with MES systems and collection of production data, and compliance with Industry 4.0 requirements