What It Takes to Be a Milaero Supplier, Part 3
April 28, 2020 | Anaya Vardya, American Standard CircuitsEstimated reading time: 4 minutes
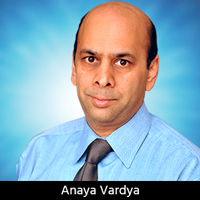
Introduction
The decision to pursue military and aerospace (milaero) certification impacts every facet of the organization, and not every shop is prepared to make this transformation. This is the third article in a four-part series, breaking down what it takes in sales and customer service, engineering and CAM, purchasing and quality, and manufacturing. Part 3 will explore what it takes to be a milaero supplier in the areas of purchasing and quality.
Purchasing Impact
Purchasing is perhaps the most critical business process as far as the milaero industry is concerned. Normally, the processes examined during AS9100 surveillance audits are rotated so that the entire QMS is covered over the course of the three-year certification period—except purchasing. Purchasing will be audited each and every time, and the auditor will focus on traceability through the entire process from quoting to shipping. The auditor will typically request a number of your aerospace customer POs, which will be comprehensively reviewed for product requirements.
This class of customer will normally have its own specification that can contain anywhere from 10 to 40 pages of quality requirements. This auditor review will entail establishing which quality requirements apply to each order, based on the PO callouts, and then verify that each of them has been addressed (added to the traveler, special customer requirement sheets, test plans, etc.). Many of the quality requirements are “flow down” requirements, meaning that you also need to communicate these requirements to any applicable suppliers. The part-number travelers will be reviewed for process accuracy, proper signoff, and raw material traceability along with any inspection and test reports. The auditor will verify that not only has this been done, but they will look for evidence that the suppliers have met the requirements. The process for MIL-PRF-31032 will be the same stringent review of military customer POs.
Another interesting requirement with aerospace products is the requirement regarding nonconforming material. Typical practice with PCB fabricators is to mark each nonconforming scrap PCB with an “X” in permanent ink, which are referred to as X-outs. Aerospace requires that companies take an extra step, no pun intended, by requiring: “Product dispositioned for scrap shall be conspicuously and permanently marked, or positively controlled, until physically rendered unusable.” This can be accomplished in a number of ways as long as the PCB will no longer be functional.
Quality Impact
Aerospace products require some additional documentation, such as AS9102 first article inspection reports. While companies normally perform first article inspections, this version is considerably more detailed and comprehensive. Many organizations task the quality team to participate in the contract review process and be responsible for the review and implementation of customer quality requirements on each order.
MIL-PRF-31032 orders are where the impact on quality is extremely high in more than one area. Microsectioning is absolutely the most taxing to the quality department and often requires additional personnel to handle the workload. Many commercial shops utilize an AQL sample methodology with regard to microsection frequency. Military orders require a 200% microsection frequency (one each in the X- and Y-axis per panel), plus numerous other sections for solderability and thermal shock testing. Further, most shops perform in-process plating sections for process control on military orders as additional copper thickness is often required.
There are also special Defense Logistics Agency (DLA) reporting that needs to be done for military orders. Special inspection forms need to be completed for each order, and coupons from the most complex military products produced each month must be sent out to an approved third-party lab for analysis. Each traveler must be reviewed for accuracy and reconciliation of build quantities (number started, shipped, scrapped. and reworked). All of the above become part of an annual report that must be submitted to the DLA for review and approval.
The organization must also establish a technical review board (TRB) that meets regularly to review the performance of the company. The responsibilities of the TRB are closely scripted and include the approval of all changes, new suppliers, the review of performance metrics, any new technology added onto military products, the number of military orders produced and inspection results, and the results of the third-party lab inspections.
Conclusion
In these two departments, becoming a milaero manufacturer changes the game significantly, adding new processes and a much higher degree of complexity when dealing with milaero orders. Milaero products demand some of the most technically challenging PCBs in the industry and, in many cases, will require the expansion of your staff. Part 4 will explore what it takes in the area of manufacturing.
Editor’s Note: Read Part 1, Part 2 and Part 4.
Anaya Vardya is president and CEO of American Standard Circuits. Vardya is also co-author of The Printed Circuit Designer’s Guide to… Fundamentals of RF/Microwave PCBs and Flex and Rigid-Flex Fundamentals. Visit I-007eBooks.com to download these and other free, educational titles.
Suggested Items
Trump Copper Tariffs Spark Concern
07/10/2025 | I-Connect007 Editorial TeamPresident Donald Trump stated on July 8 that he plans to impose a 50% tariff on copper imports, sparking concern in a global industry whose output is critical to electric vehicles, military hardware, semiconductors, and a wide range of consumer goods. According to Yahoo Finance, copper futures climbed over 2% following tariff confirmation.
Happy’s Tech Talk #40: Factors in PTH Reliability—Hole Voids
07/09/2025 | Happy Holden -- Column: Happy’s Tech TalkWhen we consider via reliability, the major contributing factors are typically processing deviations. These can be subtle and not always visible. One particularly insightful column was by Mike Carano, “Causes of Plating Voids, Pre-electroless Copper,” where he outlined some of the possible causes of hole defects for both plated through-hole (PTH) and blind vias.
Trouble in Your Tank: Can You Drill the Perfect Hole?
07/07/2025 | Michael Carano -- Column: Trouble in Your TankIn the movie “Friday Night Lights,” the head football coach (played by Billy Bob Thornton) addresses his high school football team on a hot day in August in West Texas. He asks his players one question: “Can you be perfect?” That is an interesting question, in football and the printed circuit board fabrication world, where being perfect is somewhat elusive. When it comes to mechanical drilling and via formation, can you drill the perfect hole time after time?
The Evolution of Picosecond Laser Drilling
06/19/2025 | Marcy LaRont, PCB007 MagazineIs it hard to imagine a single laser pulse reduced not only from nanoseconds to picoseconds in its pulse duration, but even to femtoseconds? Well, buckle up because it seems we are there. In this interview, Dr. Stefan Rung, technical director of laser machines at Schmoll Maschinen GmbH, traces the technology trajectory of the laser drill from the CO2 laser to cutting-edge picosecond and hybrid laser drilling systems, highlighting the benefits and limitations of each method, and demonstrating how laser innovations are shaping the future of PCB fabrication.
Day 2: More Cutting-edge Insights at the EIPC Summer Conference
06/18/2025 | Pete Starkey, I-Connect007The European Institute for the PCB Community (EIPC) summer conference took place this year in Edinburgh, Scotland, June 3-4. This is the third of three articles on the conference. The other two cover Day 1’s sessions and the opening keynote speech. Below is a recap of the second day’s sessions.