-
- News
- Books
Featured Books
- smt007 Magazine
Latest Issues
Current IssueWhat's Your Sweet Spot?
Are you in a niche that’s growing or shrinking? Is it time to reassess and refocus? We spotlight companies thriving by redefining or reinforcing their niche. What are their insights?
Moving Forward With Confidence
In this issue, we focus on sales and quoting, workforce training, new IPC leadership in the U.S. and Canada, the effects of tariffs, CFX standards, and much more—all designed to provide perspective as you move through the cloud bank of today's shifting economic market.
Intelligent Test and Inspection
Are you ready to explore the cutting-edge advancements shaping the electronics manufacturing industry? The May 2025 issue of SMT007 Magazine is packed with insights, innovations, and expert perspectives that you won’t want to miss.
- Articles
- Columns
- Links
- Media kit
||| MENU - smt007 Magazine
Book Excerpt: The Printed Circuit Assembler’s Guide to Process Validation
December 24, 2020 | Graham Naisbitt, Gen3 SystemsEstimated reading time: 2 minutes
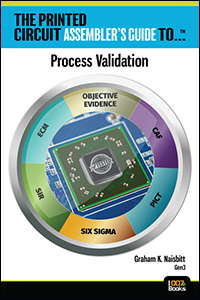
It is assumed that readers are familiar with manufacturing electronic circuit assemblies in accordance with IPC-J-STD-001 or IEC 61189-1; both are titled “Requirements for Soldered Electrical and Electronic Assemblies.” In October 2018, IPC-J-STD-001 Revision G was amended and released with a new Section 8 of the document titled “Cleaning.” The change was primarily the removal of a “cleanliness” level of 1.56 mg/square cm of NaCl equivalence. This small change has great significance in relation to how companies ensure the electrochemical reliability of their products because many have employed this measure as the sole arbiter of their entire production process.
Given the current trends towards smart infrastructures, connected vehicles, electric vehicles, and their need for ubiquitous charging points, industrial IoT (IIoT), and others, electronic circuit assemblies are deployed into humid and potentially corrosive environments arguably to a greater extent than ever before; hence, they are at greater risk of failures due to electrochemical migration (ECM) in the form of dendrites (Fig. 0.1). On the other hand, the operation of electronic devices with self-heating, the designed housing concepts, and the impact by a large thermal mass, like in automotive applications, are already known and applied countermeasures for lowering the risk of ECM as they are influencing the local humidity on an electronic level.
There are two very distinct processes going on: electrophoretic and electrochemical. Dendrites have been described as a mini plating bath. Electroplating requires a conductive electrolyte, whereas electrophoretic processes tend to be used in a dielectric fluid (although some processes add an electrolyte as well). Initially, the condensate is neither a great electrolyte nor dielectric; therefore, both processes contribute to the corrosion process.
Figure 0.1: Dendrites are formed from different processes.
The electrophoretic separates and migrates ionic particles toward the cathode, a distance between the electric charge depending on the electrostatic force and retardation force of the particles (think DNA). In most cases, the material appears first like white cigarette smoke, centrally between the polarities. Typically, this white material is flux residues dispersed with tin, and the more contaminated the board, the more pronounced this material becomes. When hydrogen gas bubbles are observed at the cathode, this indicates the current flowing and rising pH levels forming a conductive electrolyte; the process is now electrochemical, and dendrites begin to form from the cathode.
The withdrawal of the IPC cleanliness level now encourages the industry to adopt a better and more rigorous approach to ensuring electrochemical reliability. Beginning by examining the original IPC requirement and the reasons for its removal, this book provides a guide regarding electrochemical reliability testing as to surface insulation resistance (SIR) and conductive anodic filament (CAF) testing, and presents the new IEC 61189-5-504 “Process Ionic Contamination Test (PICT)” as a practicable methodology for monitoring process control in volume production.
To download The Printed Circuit Assembler’s Guide to Process Validation, click here. You can also view other titles in our full library.
Suggested Items
Intervala Hosts Employee Car and Motorcycle Show, Benefit Nonprofits
08/27/2024 | IntervalaIntervala hosted an employee car and motorcycle show, aptly named the Vala-Cruise and it was a roaring success! Employees had the chance to show off their prized wheels, and it was incredible to see the variety and passion on display.
KIC Honored with IPC Recognition for 25 Years of Membership and Contributions to Electronics Manufacturing Industry
06/24/2024 | KICKIC, a renowned pioneer in thermal process and temperature measurement solutions for electronics manufacturing, is proud to announce that it has been recognized by IPC for 25 years of membership and significant contributions to electronics manufacturing.
Boeing Starliner Spacecraft Completes Successful Crewed Docking with International Space Station
06/07/2024 | BoeingNASA astronauts Barry "Butch" Wilmore and Sunita "Suni" Williams successfully docked Boeing's Starliner spacecraft to the International Space Station (ISS), about 26 hours after launching from Cape Canaveral Space Force Station.
KIC’s Miles Moreau to Present Profiling Basics and Best Practices at SMTA Wisconsin Chapter PCBA Profile Workshop
01/25/2024 | KICKIC, a renowned pioneer in thermal process and temperature measurement solutions for electronics manufacturing, announces that Miles Moreau, General Manager, will be a featured speaker at the SMTA Wisconsin Chapter In-Person PCBA Profile Workshop.
The Drive Toward UHDI and Substrates
09/20/2023 | I-Connect007 Editorial TeamPanasonic’s Darren Hitchcock spoke with the I-Connect007 Editorial Team on the complexities of moving toward ultra HDI manufacturing. As we learn in this conversation, the number of shifting constraints relative to traditional PCB fabrication is quite large and can sometimes conflict with each other.