TIM: Thermal Interface Material in Power Electronics
June 2, 2021 | Jeff Brandman, Aismalibar North AmericaEstimated reading time: 1 minute
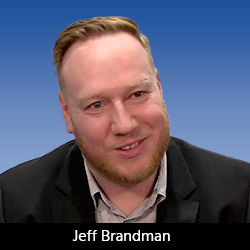
The omnipresent trend in power electronics for higher performance in smaller spaces requires a quick, effective, and cost-efficient heat transfer, within and out of, highly compact power modules. A well-designed, heat management concept from the beginning of a new design guarantees a longer lifetime of the electronic components and, by that, higher quality of the whole electronic power module.
In numerous electronic applications, especially in the field of power electronics, it is no longer sufficient to just transfer the heat generated by the electronic components to the ambient air via the printed circuit board. Instead, additional cooling of the components is required, which is achieved using an external, active, or passive cooled heat sink.
The metal housing of the application is quite often used to provide an additional cooling element for the power electronics. Therefore, protection against accidental shock because of dielectric breakdown is required as an additional safety precaution to guarantee personal protection.
TIM dielectric eliminates or minimizes air inclusions to enable efficient heat transfer from the heat source to the heat sink. An efficient solution for the thermal and insulation challenges in power electronics, both technically and commercially, can be found in an electrically insulating, heat-conducting dielectric layer such as the thermal conductive prepreg either in a typical B- or C-stage cured dielectric film.
The thermal conductive prepreg consists of a glass fiber base, enriched with mineral fillers. This thermal interface achieves a thermal conductivity of 2.2 W/mK with dielectric strengths greater than 4 kV (70 µm dielectric) or 6 kV (100 µm dielectric thickness). Utilizing a thin film thickness (70 or 100 µm), a low thermal resistance (Rth) of 0.315 or 0.45 Kcm2/W is achieved, which efficiently dissipates the heat generated by the power components to the attached cooling element for dissipation to the ambient air.
To read this entire article, which appeared in the May 2021 issue of SMT007 Magazine, click here.