-
- News
- Books
Featured Books
- smt007 Magazine
Latest Issues
Current IssueWhat's Your Sweet Spot?
Are you in a niche that’s growing or shrinking? Is it time to reassess and refocus? We spotlight companies thriving by redefining or reinforcing their niche. What are their insights?
Moving Forward With Confidence
In this issue, we focus on sales and quoting, workforce training, new IPC leadership in the U.S. and Canada, the effects of tariffs, CFX standards, and much more—all designed to provide perspective as you move through the cloud bank of today's shifting economic market.
Intelligent Test and Inspection
Are you ready to explore the cutting-edge advancements shaping the electronics manufacturing industry? The May 2025 issue of SMT007 Magazine is packed with insights, innovations, and expert perspectives that you won’t want to miss.
- Articles
- Columns
- Links
- Media kit
||| MENU - smt007 Magazine
Leveraging Data Analytics in Recall Scenarios
August 8, 2021 | Yuval Polishuk, Opcenter Intelligence Electronics, Sponsored Content*Estimated reading time: 8 minutes
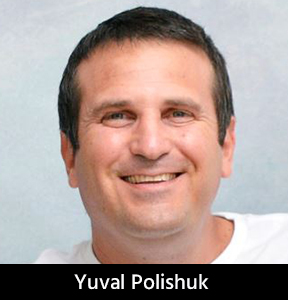
Minimize the impact of product recalls by using smart data to uncover the root cause.
Product recalls are extremely expensive. A study of hundreds of insurance claims stemming from product recalls in 28 countries across 12 industry sectors found that the average cost of a significant recall incident was upward of $12 million. However, the direct costs of the recalled products are not the full extent of the losses—a recall can cause enormous damage to a company’s brand and reputation, leading to further losses in the long term.
One of the most effective ways to minimize the impact of a recall is to define the root cause of the defect quickly and accurately, thereby minimizing the number of products that need to be recalled. For example, if a defect is related to a specific spike in temperature on the production line, only products that were produced during the spike need to be recalled: the rest of the products are not impacted. It sounds simple, but it isn’t always easy to accurately identify the root cause and products are often recalled when they don’t need to be.
As electronic components are mission critical to a wide variety of essential products—from toys and consumer electronics to medical equipment, automotive, aviation systems, and industrial robots—the electronics industry has a key role to play here. All electronics manufacturers today collect enormous amounts of data to meet compliance requirements. Analysis of this existing data can and should be a key tool in any recall investigation. However, although they have the data, manufacturers aren’t always able to utilize it effectively in recall inquiries.
In this article, we’ll cover key methods for efficiently analyzing manufacturing data to identify the root cause of a product defect in a recall scenario.
Recent Recall—Defective Airbags
In the automotive industry, the product is extremely expensive, and therefore a recall can cost many millions, if not billions of dollars. The infamous Volkswagen diesel recall is estimated to have cost the company $30 billion.
Let’s look at a recent recall in the automotive industry in which, unlike the Volkswagen scandal, the root cause wasn’t immediately apparent. In January 2020, Toyota Motor Corporation announced that it would recall 3.4 million vehicles due to a defect in an electronic control unit that caused incomplete or non-deployment of airbags. The defect was tied to a report of one fatal crash, although Toyota did not confirm a connection between the defect and the fatality.
After Toyota announced the recall, the U.S. National Highway Traffic Safety Administration (NHTSA) made a parallel announcement claiming that eight deaths could be tied to the defect. The NHTSA then expanded the probe, looking into 12.3 million potentially defective airbags from several automakers, including Fiat Chrysler Automobiles NV, Honda Motor Co., Hyundai Motor Co., Kia Motors Corp., and Mitsubishi, in addition to Toyota. All the vehicles under investigation were equipped with an airbag control unit initially produced by TRW Automotive Holdings Corp, which is now owned by ZF Friedrichshafen. The goal of the probe was to identify the root cause of the defect, and hopefully limit the recall. As part of the probe, the manufacturer of the PCB used in the airbag control unit that had malfunctioned was asked to assist in the investigation into the root cause of the defect.
What Can a PCB Manufacturer Do?
Having described the situation of this real recall, we are now leaving the realm of reported events. From here, using the real recall as a scenario for a hypothetical investigation, let’s look at the methodology a PCB manufacturer should follow in that type of situation. While the following describes a simulated investigation, with hypothetical results, the methodology and steps would all be relevant to any recall investigation.
To locate the root cause, the manufacturer must check for anomalies in the production data. If the data is held in multiple different systems and machines across the factory, this can be extremely time-consuming, involving numerous people, and potentially becoming disruptive to productivity.
However, if the data is accessible through a comprehensive analytics and reporting tool, the investigation can be conducted and documented relatively easily, quickly, and most importantly, accurately. The specific examples shown below are based on Siemens’ Opcenter™ Intelligence Electronics software, however the same three-stage methodology should be applied regardless of the analytics tool being used.
Stage 1: Zoom In
The first step in detecting a defect focuses on comparing the manufacturer specifications to the processes and environmental conditions undergone by a specific PCB board involved in the defective scenario. The objective of this step is to ensure that everything was done properly, according to the plan for that specific board.
First, to get the PCB serial number, we review the control unit system report. Through the Work-in-Progress report, which shows the progress of each work order, we can confirm that all required tests, including electrical tests, were performed, and that the product met all quality standards throughout the process.
In our example, we can see how many units were produced and how many defects were reported during the manufacturing process. Drilling down through the report, we can see what defects were found and their repair process. For example, we can see that a PCB failed automatic optical inspection (AOI). However, under further analysis at the repair station, the AOI failure was found to be a false defect.
Summary of stage 1 hypothetical findings: No defects were identified in this stage of the investigation.
Stage 2: Zoom Out
After comparing the manufacturing plan to what occurred with the specific, problematic PCB, the next step is to zoom out and look at unusual trends or events on the production line in general. This stage is important regardless of whether a defect was identified in stage 1, as there can be more than one problem that impacts a product.
Stage 2 relies heavily on statistical and Six Sigma methodology for monitoring and process control. It helps to identify the stability of the process, baseline historical performance and variation, and identify abnormal behavior in the process.
It charts data according to several KPIs to see if the process is stable and predictable, distributing results on a number curve. The Control Charts graph, which is part of SPC, visualizes the boundary values of a given process, and makes it easy to see deviations from the boundaries as well as abnormal behaviors within the boundaries.
The analysis may include data related to the environmental conditions of the manufacturing process, such as the humidity in the general environment and/or in a specific machine. It also evaluates quality measurements from the machines that do the testing, such as solder paste inspection (SPI). SPI checks several measurements for every point of solder paste on an individual board. If they are all within the defined tolerances, the board passes the check. If any fall above or below the limits, the board will fail. Next, a box plot report can illustrate the distribution of measurements for each point on the bare board across the entire batch. The QA engineer, or whoever is reviewing the material, can see if there were any changes in the numbers of a certain point over a series of boards, which could indicate a problem.
Summary of stage 2 hypothetical findings: There were no problems identified at this stage that could have influenced the PCBs placed in the defective airbags.
Stage 3: Materials and Components
Each assembled PCB is made up of multiple components. Therefore, the last step in the process is to review the material supply chain and processes for those components. The most efficient way to do this is to compare a PCB involved in the problematic scenario to one that was not involved.
If the problematic board includes components from a different supplier, the probe should include a deep dive into the history of those components. Elements that should be reviewed include:
- The work order from the ERP system
- What assembly units were produced
- The size of the batch
- How many units were completed
- How many defects were reported during the manufacturing process
- First pass yield (FPY)—how many units passed initial testing
- Defects found per number of units (DPU)
- The repair process
With our comprehensive analytics and reporting tool, we can see the reel ID for every component, which in turn enables us to know the manufacturer and all details relating to the reel.
With every PCB order, the PCB engineering team creates the bills of materials and approves all suppliers. However, there may be issues in an approved supplier’s own supply chain that could enable a substandard component to slip through. In our hypothetical investigation, the analysis uncovered that an approved supplier was using a component from an unapproved manufacturer. Further tracing revealed that the component was a counterfeit.
Summary of stage 3 findings: Analysis comparing the materials used in the PCB involved in the crash with the materials used in a PCB that had not been involved pinpointed a single defective component. In this hypothetical investigation, the counterfeit component was identified as the root cause of the PCB defect.
Benefits of an Effective Investigation
Having efficiently conducted the full analysis using its end-to-end analytics and reporting tool, and armed with the full supporting documentation, the PCB manufacturer would then be able to share the results with the NHTSA.
As a result, the recall could then focus solely on the airbags with the counterfeit components. This would enable the automobile manufacturer to limit the vehicles that needed to be recalled to only those in which those specific airbags were installed.
Without this analysis system the number of recalled vehicles would likely be much higher. The precise and accurate analysis can reduce the number of recalls and minimize the costs and reputation implications of the recall.
In any recall, the costs and impact do not stop at the manufacturer of the final product that was recalled. For PCB manufacturers, the traceability enabled by a powerful analytics tool like Opcenter Intelligence Electronics can be crucial to mitigating the potential costs to their business, both financial and in terms of reputation.
Yuval Polishuk is the product owner for Opcenter Intelligence Electronics. He is responsible for its strategic product development and roadmap as well as requirement definitions, based on years of experience in handling key electronics manufacturers implementation projects and solving customer pain points.
Sponsored Content